Aluminum alloy die casting is a kind of casting technology that uses molten aluminum alloy melt at high temperature and high speed to inject into the mold cavity. The characteristics of this casting method are that the products are formed precisely and the production efficiency is high. However, there are some defects in the conventional die-casting process, because the gas in the mold cavity can not be effectively eliminated during high-speed injection, resulting in the formation of porosity defects, resulting in poor mechanical properties of the casting. In order to solve this problem, people use the vacuum die casting method, that is, the gas in the mold cavity is drawn out to form a certain vacuum or negative pressure state, so as to reduce the porosity defects in the casting. In this article, we introduce the effect of vacuum die casting technology on the appearance, quality and mechanical properties of aluminum alloy die castings.
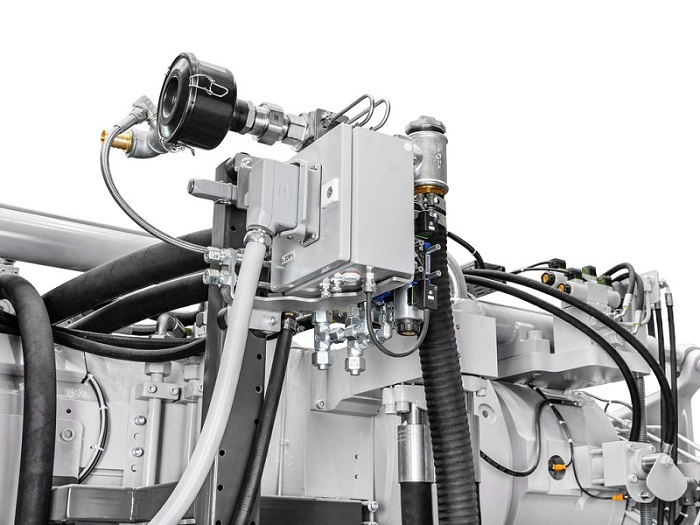
What Is Vacuum Die Casting?
For a long time, in order to broaden the application range of die castings and improve the mechanical properties of die castings, some new die casting methods have been studied, such as ultra-low speed die casting, oxygen filling die casting and vacuum die casting. The main purpose of the above methods is to reduce the air entrainment in the filling process of liquid metal, so as to improve the mechanical properties of castings. Due to the low production efficiency of low-speed die-casting method and the disadvantages of oxygen filled die-casting method, such as complex operation procedures and difficult control of process parameters, the two methods are not widely used in actual production. The principle of vacuum die casting is that the gas in the cavity is extracted and the liquid metal is filled in the cavity under vacuum state, so the gas involved is less and the mechanical properties of the casting are improved. And the vacuum die casting method is the same as the ordinary die casting method, the operation is convenient, and the production efficiency is not reduced. Therefore, since the emergence of vacuum die casting, it has shown strong vitality, with the development of related technology, its application will be more and more widely.
What Are The Impacts Of Vacuum Die Casting Technology On Aluminum Alloy Die Castings
We aim at the problems of poor appearance quality, poor mechanical properties and low average pass rate of aluminum alloy quick joint (OPW) produced by common die casting method in a certain company, we add it on the basis of the original mold. And through several steps: test, test results and analysis, the appearance quality of the aluminum die casting sample, the mechanical properties of the aluminum alloy die casting sample, the average qualified rate comparison, we’ve got the following conclusion.
1. After the tensile strength test, compared with the ordinary die casting sample, the cross-section grain of the vacuum die casting sample is finer and the color is closer to the original color of aluminum alloy. After T6 heat treatment, the surface blister of the vacuum die casting sample is less, the diameter of the same part of the sample is measured, and the diameter of the common die casting sample is increased by 0.1 compared with that before heat treatment. However, there is little change in vacuum die casting samples.
2. As cast, the mechanical properties of vacuum die casting samples are slightly better than those of ordinary die casting samples. The tensile strength increased by 6.67%, elongation increased by 25%, and hardness increased by 4.34%. After T6 heat treatment, the mechanical properties of vacuum die casting samples are still in good condition, and the elongation is increased by 180% compared with as cast samples, while the mechanical properties of ordinary die casting samples decrease greatly.
3. Using vacuum die casting technology can not only improve the quality of aluminum alloy die casting surface, but also reduce the average porosity. Among them, the average qualified rate of 633f-2 type quick coupling can reach 89%, and the qualified rate of 633f-2 type quick coupling is increased by 28% compared with ordinary die casting process.