4140 alloy steel is a chromium-molybdenum alloy steel that is widely used in many industrial applications due to its combination of high strength, toughness, and fatigue resistance. 4140 alloy steel is a versatile high-strength steel with an excellent combination of strength, toughness, and fatigue resistance after heat treatment. This makes it an ideal choice for many critical components and high-stress applications.
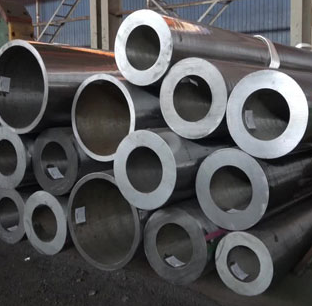
What Is 4140 Alloy Steel Used For?
Here are some of the most common uses and applications of 4140 alloy steel:
- – Shafts: 4140 is commonly used to make shafting for industrial CNC machines and equipment like compressors, pumps, and mixers due to its ability to withstand high torque.
- – Gears: The high strength and toughness of 4140 allow it to be used to manufacture high-powered gearing, such as in transmissions, machine tools, and presses.
- – Aircraft parts: 4140 is used to construct structural aircraft components like landing gear, frames, and hydraulic cylinders that require strength and fatigue resistance.
- – Oil and gas industry – Drill collars, casings, tool joints, and other well drilling tools are made from 4140 due to their combination of strength, toughness, and corrosion resistance.
- – Construction and mining equipment: Excavator and loader pins and bushings, crane hooks, and mine plow blades are fabricated from 4140 steel.
- – Automotive: 4140 can be found in automotive applications like axle shafts, steering knuckles, connecting rods, rollers, and spindles.
- – Railways: Rail car components including couplers, yokes, and side frames are made from 4140 steel.
- – Pumps and processing equipment: The steel is used to make pump shafts, impellers, press plates, extrusion barrels, and screw conveyors.
- – Bolts: High-strength tensioned bolts and studs are manufactured from 4140 alloy steel.
Typical Heat Treatment Processes Used for 4140 Alloy Steel
- 1. Normalizing
-Done by heating the steel to 1650°F (900°C) and then air cooling.
-Refines the grain structure and improves machinability and uniformity.
- 2. Full Annealing
-Heating to about 1550°F (845°C), soaking, and slow cooling in the furnace.
-Produces a fine pearlitic structure and maximum softness and ductility.
- 3. Stress Relieving
-Heating to 1100-1200°F (595-650°C), soaking, and slow cooling.
-Removes stresses from prior cold working to prevent potential distortion or cracking.
- 4. Hardening
-Austenitizing at 1500-1525°F (815-830°C), followed by quenching in oil or water.
-Produces a martensitic structure with high hardness and strength.
- 5. Tempering
-Reheating quenched steel to 1100-1200°F (595-650°C) and holding for 1-3 hours.
-Decreases brittleness and increases toughness and ductility. Multiple tempering stages may be applied.
What Are the Properties of 4140 Alloy Steel?
Property | Value |
Carbon (C) | 0.38% – 0.43% |
Chromium (Cr) | 0.8% – 1.1% |
Molybdenum (Mo) | 0.15% – 0.25% |
Manganese (Mn) | 0.75% – 1.0% |
Silicon (Si) | 0.15% – 0.30% |
Sulfur (S) | ≤ 0.040% |
Phosphorus (P) | ≤ 0.035% |
Tensile Strength | 830 – 1000 MPa |
Yield Strength | ≥ 655 MPa |
Elongation | 17% |
Reduction of Area | ≥ 50% |
Hardness | 217 – 255 HB |
Normalizing | 1650°F (900°C), air cool |
Annealing | 1500°F (650°C), slow furnace cool |
Hardening | 1500-1525°F (815-830°C), oil quench |
Tempering | 1100-1200°F (595-650°C) |
Weldability | Welds well using manual and automatic methods. Preheating may be required. |
Machinability | 65-95% of 1% carbon steel |