A heat sink is a passive heat exchanger that is used to cool electronic or mechanical devices by dissipating heat into the surrounding environment.
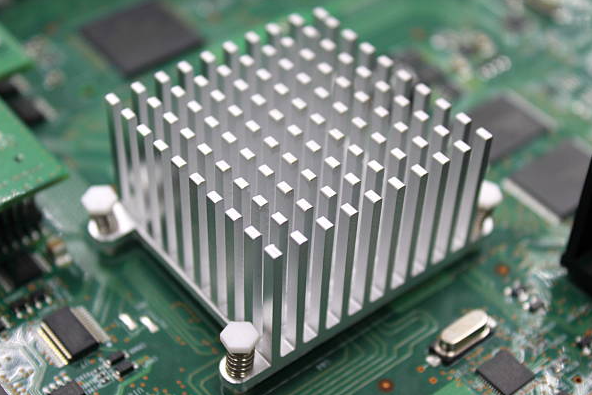
How Does It Work
A heat sink is a passive cooling device that is commonly used to cool electronic components and systems. It is made of a highly thermally conductive metal like aluminum and contains fins or ridges to increase surface area. A heat sink is attached to a hot component using thermal adhesive or grease to promote heat transfer. As the electronic component operates, it generates heat which is conducted into the base of the heat sink. The heat travels through the conductive metal base and into the fins. The large surface area of the fins allows more heat to be dissipated into the surrounding air through convection and radiation. Cooler ambient air circulates the fins, absorbing the dissipated heat. This air warms up and rises due to convection, allowing new cooler air to flow in and continue removing heat from the fins. Fans are often used to maximize airflow over the fins and cooling capacity. Overall, the high conductivity and large surface area allow the heat sink to absorb heat from the component and efficiently dissipate it into the moving air around it, keeping the component within safe operating temperatures.
Key Components of Heat Sink
The key aspects are the conductive base plate contacting the heat source and the large surface area fins dissipating heat into the surroundings. Getting heat into and then out of the heat sink through these components allows maintaining safe operating temperatures.
- – Base plate
This is the flat portion that comes into direct contact with the heat source. It is usually made of a highly thermally conductive metal like aluminum or copper to allow heat transfer. The base spreads heat outwards toward the fins.
- – Fins
These thin slices of metal extrude from the base plate and provide a large surface area to dissipate heat. More numerous and longer fins increase surface area for heat dissipation. Fins are made of metals like aluminum and copper for good thermal conductivity.
- – Mounting hardware
This includes screws, clamps, adhesives, or mounting brackets to affix the base plate securely to the heat source. Proper contact ensures efficient heat transfer. Thermal interface materials like grease or pads can be used too.
- – Fan
An active cooling fan attached to the heat sink improves airflow over the fins. This significantly enhances convection heat transfer from the fins to the air, improving cooling performance.
- – Shroud
Plastic enclosures that funnel air onto specific areas of the fins to maximize blowing efficiency. Improves targeted airflow.
- – Base plate coatings
Special black anodized or composite coatings can enhance radiation heat dissipation from the base plate in some cases.
- – Heat pipes
Used to transfer heat to fins that are not directly attached to the base plate. Heat pipes contain liquid coolant that evaporates and carries heat to the fins.
What Materials Are Heat Sinks Made of
Aluminum, copper, and their alloys are the most popular heat sink materials due to their high conductivity, low cost, and ease of fabrication. However many material types are used for tailored performance.
- – Aluminum
This is the most widely used material for heat sinks. Aluminum has high thermal conductivity, is lightweight, easy to extrude into complex shapes, and is cost-effective. Heat sinks made of aluminum fins and base plates can handle low-to-moderate heat levels.
- – Copper
Has excellent thermal conductivity, nearly twice that of aluminum. This allows copper heat sinks to manage very high heat loads. However, copper is substantially heavier than aluminum and more expensive. Copper heat sinks tend to be used only when extreme cooling capacity is needed.
- – Aluminum Alloys
Alloys are made by mixing aluminum with metals like silicon, magnesium, or zinc to improve specific properties. Allows tailoring heat sinks to requirements. Common alloys are 6061 and 5052.
- – Carbon Composites
Lightweight carbon materials like graphite or carbon fibers in a matrix. Used when weight is a big concern along with thermal performance. More expensive than aluminum.
- – Ceramics
Ceramic materials like aluminum nitride, boron nitride, and silicon carbide have high thermal conductivity. They are used in specialized high-power or high-temperature applications.
- – Thermal Adhesives
Used to attach and thermally interface the heat sink to the heat source. Popular types are epoxy, polyurethane, and silicone-based adhesives that are thermally conductive.
- – Heat Pipes
Made of thermally conductive metals like copper or aluminum. Heat pipes transfer heat between the source and the sink. They contain liquid coolant that evaporates and condenses to move heat.
Types of Heat Sinks
- – Extruded Heat Sinks
These are made by extruding aluminum or copper through a die to create fins on a base plate. Simple and inexpensive to produce. Fins can be straight or tapered.
- – Stamped Heat Sinks
Made by stamping fins out of sheet metal and bonding them onto a base plate. Allows more flexibility and customization of fin shapes and layouts.
- – Bonded Fin Heat Sinks
Fins are bonded onto the base plate using adhesives or thermal epoxy for high mechanical strength. Allows using dissimilar metals for fins and base.
- – Folded Fin Heat Sinks
Fins are cut, punched, or folded out of the base plate material itself. No bonding is required. Common in aluminum extruded heat sinks.
- – Skived Heat Sinks
Fins are shaved off the base plate using skiving machines. Provides strong fin-to-base junctions.
- – Machined Heat Sinks
Heat sinks are precision CNC machined out of metal blocks. Allows complex fin geometries but is expensive.
- – Pin Fin Heat Sinks
Cylindrical pins are bonded or pressed into the base plate instead of flat fins. Enhances surface area and turbulence.
- – Thermoelectric Heat Sinks
Use thermoelectric modules that electrically pump heat. No moving parts. Used in appliances.
- – Heat Pipe Heat Sinks
Heat pipes transfer heat from the source to the fins. The liquid inside evaporates and condenses to move heat.
- – Active Heat Sinks
Use cooling fans or liquid pumping to forcibly enhance heat dissipation from fins.
Applications of Heat Sinks
Heat sinks are used extensively in electronics cooling across all industries. Well-known brands cater to specific applications based on factors like performance, cost, customization needs, and operating conditions.
- – Computers/CPUs: Noctua, Cooler Master, Corsair, NZXT, Thermaltake, ARCTIC
- – Consumer Electronics: Sunon, Delta, EBM-Papst, Sanyo Denki, Foxconn
- – Automotive: Honeywell, Boyd Corporation, Dana Incorporated, Modine Manufacturing
- – LED Lighting: Cree, Lumileds, Bridgelux, Nichia
- – Power Supplies: Aavid Thermalloy, Advanced Thermal Solutions, Alpha, Ohmite, Fischer Elektronik
- – Industrial Equipment: Wakefield-Vette, Aavid Thermalloy, Columbia-Staver, HS Marston
- – Appliances: GE, Whirlpool, Panasonic, Samsung, LG
- – Laboratory/Medical Equipment: Wakefield-Vette, Aavid Thermalloy, Boyd, Lytron
- – Aerospace/Military: Boyd Corporation, Aavid Thermalloy, Thermacore, Lytron – Telecommunications: Aavid Thermalloy, Alpha, Wakefield-Vette, Ohmite