Aluminum alloy A206 is a remarkable material prized for its exceptional strength, durability, and corrosion resistance. This high-performance alloy finds widespread use in critical applications across industries, from aerospace to automotive to heavy machinery. But the properties of A206 are not solely inherent – they are greatly influenced by the manufacturing process used to produce it. In this article, we will explore the properties, components, and applications of A206 aluminum, while diving into a detailed comparison of A206-T4 vs. A206-T7 to help you determine the best option for your project.
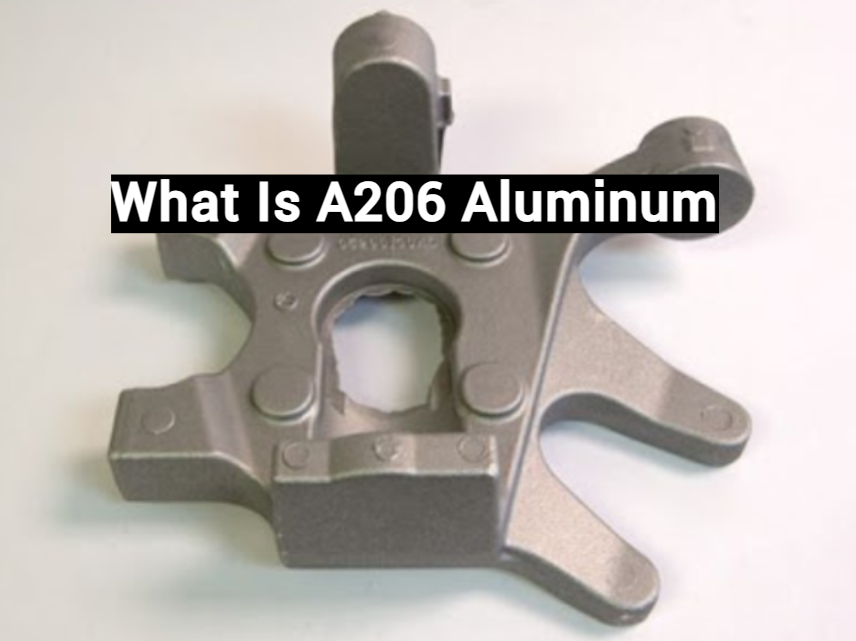
What Is A206 Aluminum?
A206 aluminum is a high-strength, high-performance aluminum casting alloy primarily used in aerospace, automotive, and industrial applications. It is known for its excellent mechanical properties, including high tensile and yield strength, corrosion resistance, and good machinability. A206 is typically heat-treated to enhance its strength, often using T4 or T7 tempering processes, which also improve its fatigue resistance. This alloy’s superior strength-to-weight ratio makes it ideal for critical structural components such as engine blocks, aircraft fittings, and high-load-bearing parts, where durability and reliability are essential.
The Properties Of Aluminum Alloy A206
A206 aluminum is highly regarded for its excellent mechanical and physical properties, making it a preferred material for high-performance applications. Below are its key properties:
1. Mechanical Properties
High Tensile Strength: A206 offers tensile strengths ranging from 310 to 455 MPa (45–66 ksi) depending on the temper (e.g., T4 or T7).
High Yield Strength: The alloy typically exhibits yield strengths between 275 and 345 MPa (40–50 ksi).
Excellent Fatigue Resistance: It performs well under cyclic loads, suitable for dynamic applications.
Good Elongation: A206 has moderate ductility with elongation percentages ranging from 2% to 5%.
2. Corrosion Resistance
A206 is highly resistant to atmospheric and chemical corrosion, making it reliable for outdoor and harsh environmental conditions.
3. Heat Treatability
A206 can be heat-treated to improve strength and performance. Common tempers include:
T4: Offers a balance of strength and ductility.
T7: Provides higher strength and resistance to stress corrosion cracking.
4. Machinability and Weldability
Machinability: A206 has good machinability, allowing for precise and complex designs.
Weldability: While not as weldable as other aluminum alloys, it can be joined with care and appropriate techniques.
5. Lightweight
With a low density of approximately 2.7 g/cm³, A206 provides a high strength-to-weight ratio, ideal for aerospace and automotive applications.
The Components Of A206 Aluminum Alloy
A206 aluminum alloy is a high-strength aluminum-copper casting alloy designed for applications requiring excellent mechanical properties. Its composition is carefully balanced to achieve superior strength, durability, and performance. Below are the main components and their roles:
1. Aluminum (Base Metal)
Aluminum serves as the primary component, typically comprising over 90% of the alloy. It provides a lightweight foundation, excellent corrosion resistance, and good machinability. The base metal’s low density makes A206 suitable for applications demanding a high strength-to-weight ratio, such as aerospace, automotive, and industrial components.
2. Copper (4.2%–4.6%)
Copper is the principal alloying element in A206 and significantly enhances its strength and hardness. It contributes to the alloy’s superior tensile and yield strengths while maintaining good fatigue resistance. However, the addition of copper slightly reduces corrosion resistance, necessitating proper surface treatments for certain applications.
3. Magnesium (0.15%–0.35%)
Magnesium acts as a secondary strengthening agent. It improves the alloy’s response to heat treatment, allowing the material to achieve high mechanical properties through tempering processes. Magnesium also enhances ductility, ensuring that the alloy remains functional under dynamic and cyclic loads.
4. Manganese (0.2%–0.4%)
Manganese contributes to the alloy’s resistance to cracking during solidification and casting processes. It refines the grain structure and improves toughness, particularly in demanding environments. Manganese also plays a role in enhancing corrosion resistance.
5. Iron and Silicon (Trace Elements)
Small amounts of iron and silicon are present as impurities or incidental additions, typically under 0.2% each. These elements may slightly affect machinability and casting characteristics, but their content is controlled to minimize adverse effects on mechanical properties.
6. Other Trace Elements (e.g., Zinc, Titanium)
Other elements like zinc and titanium may be present in minute quantities. These trace elements are generally kept under strict limits to avoid compromising the alloy’s mechanical performance and corrosion resistance.
The Applications Of A206 Aluminum
Aluminum alloy A206 is a type of aluminum alloy that is known for its high strength, toughness, and corrosion resistance. It is a versatile material with a wide range of applications in various industries. Here are some of the common applications of aluminum alloy A206:
Automotive Industry:
Automotive components: Aluminum alloy A206 is used in the production of various automotive components, such as engine blocks, transmission cases, and suspension components, due to its high strength-to-weight ratio and corrosion resistance.
Wheels and wheels hubs: A206 alloy is also used in the manufacture of lightweight and durable wheels and wheel hubs for vehicles.
Aerospace Industry:
Aircraft structural components: Aluminum alloy A206 is a popular choice for aircraft structural components, such as wing and fuselage parts, due to its high strength and low weight.
Aerospace fasteners and fittings: This alloy is also used in the production of aerospace fasteners, fittings, and other hardware components.
Marine and Shipbuilding Industry:
Marine equipment and components: Aluminum alloy A206 is used in the manufacture of marine equipment and components, such as boat hulls, propellers, and deck fittings, owing to its corrosion resistance and strength.
Industrial Equipment and Machinery:
Heavy machinery components: A206 alloy is used in the production of various heavy machinery components, such as gears, shafts, and other load-bearing parts, due to its high strength and durability.
Industrial tools and equipment: This alloy is also used in the manufacture of industrial tools and equipment, where its combination of strength, corrosion resistance, and lightweight properties make it a suitable choice.
Consumer and Household Products:
Household appliances: Aluminum alloy A206 is used in the production of household appliances, such as refrigerators, washing machines, and cooking utensils, due to its corrosion resistance and ease of fabrication.
Sports and leisure equipment: This alloy is also used in the manufacture of various sports and leisure equipment, such as bicycles, golf clubs, and outdoor furniture, where its lightweight and strong properties are desirable.
Manufacturing A206 Aluminum Alloy by Step Sand Casting
The study investigates the effect of solidification time on the grain size, mechanical properties, hardness, wettability, and corrosion resistance of A206-T7 aluminum alloy. A step sand casting process with varying section thicknesses was used to achieve different solidification times.
The experimental results showed that increasing the casting thickness, and thereby the solidification time, led to an increase in the average grain size from 80 to 124 micrometers. The wettability study revealed that the contact angle values ranged between 71 and 87 degrees. The corrosion experiment demonstrated a correlation between solidification time and corrosion resistance, with the corrosion current decreasing by 73% as the section thickness increased from 0.75 to 2 inches. The dominant corrosion mechanism in this alloy was identified as intergranular corrosion, which is influenced by the solidification time and resulting microstructure. The simulation results were consistent with the experimental findings, confirming the effect of solidification time on the properties of the A206 aluminum alloy.
A206.0-T4 vs A206.0–T7 Aluminum, Which Is Better?
The choice between A206.0-T4 and A206.0-T7 aluminum depends on the specific requirements of your application, as each temper has distinct properties optimized for different conditions. Here’s a comparison to help you decide:
1. A206.0-T4 Aluminum
Heat Treatment: The T4 temper is achieved by solution heat treating the alloy, followed by natural aging (aging at room temperature).
Properties:
High ductility and moderate strength.
Excellent toughness and resistance to cracking.
Superior machinability compared to the T7 temper.
Applications: T4 is ideal for applications where formability and toughness are more critical than maximum strength, such as components subjected to complex machining or moderate stress.
2. A206.0-T7 Aluminum
Heat Treatment: The T7 temper involves solution heat treating followed by overaging (artificial aging at elevated temperatures).
Properties:
Higher tensile and yield strength than T4, making it more suitable for applications requiring maximum load resistance.
Reduced ductility and toughness compared to T4.
Increased resistance to stress corrosion cracking, making it better suited for harsh environments.
Applications: T7 is preferred for high-strength structural applications, especially in aerospace and automotive sectors, where weight savings and performance under stress are crucial.
Which Is Better?
If your application prioritizes ductility, machinability, and toughness, the A206.0-T4 is a better choice. It is well-suited for parts that will undergo significant machining or formability challenges. If your application demands maximum strength and stress resistance, particularly in challenging environments, the A206.0-T7 temper is the superior option.