A357 aluminum alloy is a widely used casting alloy known for its high strength, excellent corrosion resistance, and good machinability. It finds applications in aerospace, automotive, and industrial sectors where durability and lightweight properties are essential. As a professional A357 aluminum casting supplier, today we provide a detailed overview of A357 aluminum alloy, including its composition, properties, types, equivalent grades, applications, and a comparison with A356 aluminum alloy.
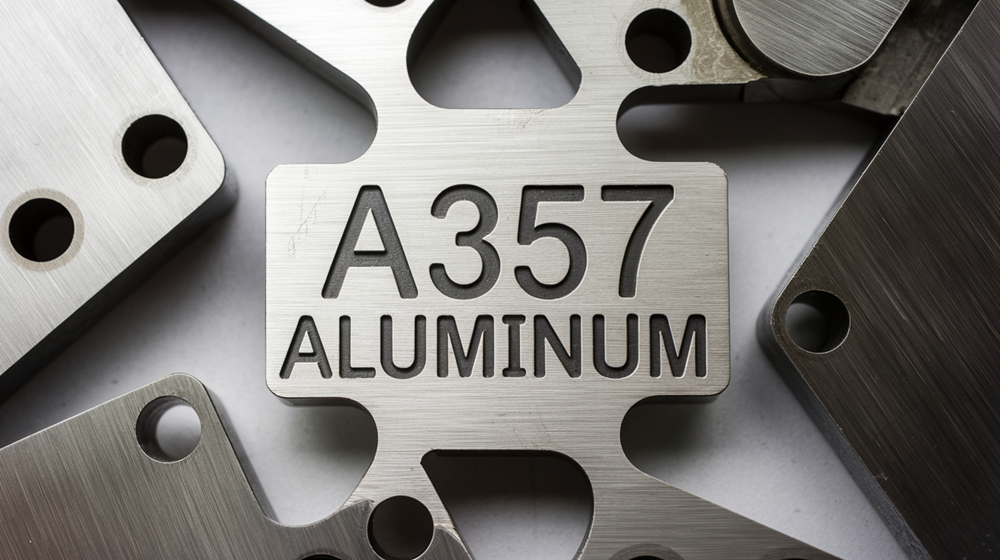
What is A357 Aluminum Alloy?
A357 aluminum alloy is an aluminum-silicon-magnesium (Al-Si-Mg) casting alloy known for its high strength, good corrosion resistance, and excellent thermal conductivity. It is commonly used in aerospace and automotive industries for manufacturing structural components that require both durability and lightweight properties.
This alloy was developed as an improvement over ZL101A by increasing its magnesium content, resulting in enhanced mechanical strength and performance. A357 can be processed using casting, extrusion, and forging techniques, and it can be further strengthened through heat treatment.
A357 Aluminum Composition (ASTM Standard)
The primary elements in A357 aluminum alloy include:
Element | Content Range (wt%) | Function |
---|---|---|
Si (Silicon) | 6.5 – 7.5 | Improves fluidity, reduces hot cracking tendency |
Mg (Magnesium) | 0.45 – 0.6 | Forms Mg₂Si phase for strengthening |
Cu (Copper) | ≤ 0.2 | Minor strengthening, but reduces corrosion resistance |
Fe (Iron) | ≤ 0.12 | Impurity control (prevents brittle phases) |
Others | Ti ≤ 0.2, Zn ≤ 0.1 | Grain refinement, improves casting performance |
A357 Aluminum Properties
A357 aluminum alloy is known for its high strength, excellent corrosion resistance, and good thermal conductivity. It is widely used in aerospace, automotive, and industrial applications where durability and lightweight properties are essential.
Mechanical Properties
Property | Value Range |
---|---|
Ultimate Tensile Strength (UTS) | 310-350 MPa |
Yield Strength (YS) | 250-280 MPa |
Elongation | 2-5% |
Brinell Hardness (HB) | 90-100 |
Fatigue Strength | ~110 MPa (10⁷ cycles) |
1. High Strength
A357 aluminum alloy exhibits excellent mechanical strength, making it suitable for load-bearing structural components. Its tensile and yield strength allow it to withstand high stress, making it a preferred choice for aerospace and automotive applications.
2. Good Corrosion Resistance
The alloy shows strong resistance to oxidation and corrosion, allowing it to perform well in harsh environments, including exposure to moisture and chemicals. This property extends the lifespan of components made from A357 aluminum.
3. Excellent Machinability
A357 aluminum alloy can be easily processed through various manufacturing techniques, including casting, extrusion, forging, and welding. This versatility enables the production of complex parts with precise dimensions.
4. High Temperature Stability
A357 retains its mechanical properties even at elevated temperatures, maintaining structural integrity and performance in high-heat environments such as engines and aerospace applications.
5. Low Density & Lightweight
Compared to steel, A357 aluminum alloy has a lower density, reducing the overall weight of components. This contributes to improved fuel efficiency in vehicles and aircraft while maintaining high strength.
By balancing strength, corrosion resistance, and workability, A357 aluminum alloy proves to be a reliable material for demanding engineering applications.
A357 Aluminum Types & Their Properties
A357 aluminum alloy can undergo various heat treatment processes to enhance its mechanical properties, including strength, hardness, and durability. The most common heat treatment conditions for A357 are T5 and T6, each offering distinct advantages depending on the application.
A357-T5 Properties
- Cooled from the casting process and then artificially aged.
- Provides moderate strength with improved stability.
- Offers better resistance to deformation at elevated temperatures.
- Typically used in applications requiring good dimensional stability and moderate mechanical strength.
A357-T6 Properties
- Solution heat-treated, quenched, and then artificially aged.
- Achieves higher tensile and yield strength compared to T5.
- Provides better elongation and improved fatigue resistance.
- Widely used in aerospace and automotive applications where high strength and durability are required.
Comparison of A357-T5 and A357-T6
Heat Treatment | Strength | Ductility | Fatigue Resistance | Application |
---|---|---|---|---|
A357-T5 | Moderate | Lower than T6 | Good | Structural components requiring stability |
A357-T6 | High | Better than T5 | Excellent | Aerospace, automotive, and high-stress applications |
A357 Aluminum Equivalent Standards
A357 aluminum alloy is recognized under multiple international standards:
Standard | Equivalent Grade |
---|---|
China (GB/T1173) | ZL114A |
International (ISO 3522) | AlSi7Mg |
Japan (JIS H5202) | AC4C |
France (NF A57-105) | A-S7G-03 |
USA (ASTM B179) | A357 |
UK (BS 1490) | LM25 |
Germany (DIN 1725.2) | G-AlSi7Mg(Fe) |
A357 Aluminum Applications
A357 aluminum alloy is widely used across different industries due to its high strength, corrosion resistance, and lightweight properties. Major application fields include:
- Aerospace: Used in aircraft engine parts and structural components due to its strength and lightweight characteristics.
- Automotive: Commonly found in engine cylinders, body frames, and other critical parts to reduce weight and improve fuel efficiency.
- Military: Utilized in tank and armored vehicle components for its durability and resistance to harsh environments.
- Electronics: Applied in heat sinks and housings due to its excellent thermal conductivity.
- Construction & Home Furnishings: Used in doors, windows, furniture, and decorative materials for its corrosion resistance and aesthetic appeal.
A356 vs. A357 Alloy – What are the Differences?
A356 and A357 are similar aluminum-silicon-magnesium casting alloys, but they have key differences:
Property | A356 Alloy | A357 Alloy |
---|---|---|
Silicon (Si) Content | 6.5-7.5% | 6.5-7.5% |
Magnesium (Mg) Content | 0.2-0.45% | 0.45-0.6% |
Titanium (Ti) Content | ≤0.15% | 0.10-0.2% |
Strength | Moderate | Higher than A356 due to increased Mg content |
Elongation | Higher ductility | Slightly lower elongation than A356 |
Corrosion Resistance | Good | Slightly better due to higher Mg content |
Heat Treatment | Can be heat-treated (T5, T6) | Can be heat-treated (T5, T6) |
Applications | General-purpose casting, automotive, and structural components | Aerospace, high-performance automotive, and heavy-duty applications |
Cost | Lower | Higher due to increased magnesium content and improved properties |
A356 vs. A357 Alloy – Which is Better?
The choice between A356 and A357 depends on the specific requirements of the application:
- Choose A356 if:
- Higher elongation and ductility are needed.
- The application does not require extremely high strength.
- Cost-effectiveness is a priority for general-purpose casting.
- Choose A357 if:
- Higher strength and load-bearing capacity are required.
- The component will be exposed to high stress or extreme environments (e.g., aerospace, military, or high-performance automotive parts).
- Improved corrosion resistance is necessary.
Ultimately, A357 is more suitable for applications requiring higher strength and durability, while A356 remains a versatile option where extreme strength is not the primary concern.