ADC14 is a high-performance aluminum alloy widely used in industries like automotive, electronics, and marine applications. Known for its excellent castability, wear resistance, and corrosion resistance. But how does ADC14 compare to other popular aluminum alloys, such as ADC12? This article explores the composition, properties, equivalent and uses of ADC14 and highlights the differences between ADC14 and ADC12 to help you choose the right alloy for your needs.
What is ADC14 Aluminum Alloy?
ADC14 Aluminum Alloy is a high-pressure die-casting aluminum alloy widely used in the automotive and engineering industries due to its excellent mechanical properties and castability. It is part of the ADC (Aluminum Die Casting) series, standardized primarily in Japan, and is equivalent to the A383 alloy in global standards.
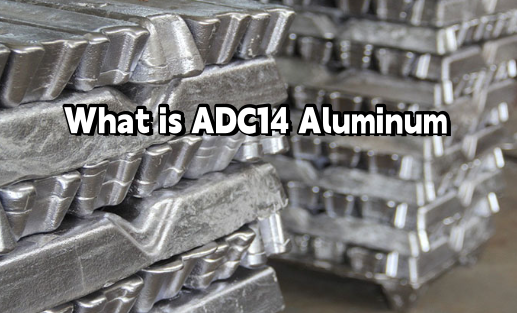
Characteristics of ADC6 Alloy
Composition: ADC14 primarily consists of aluminum and is alloyed with silicon (Si), copper (Cu), magnesium (Mg), and other trace elements to enhance its strength, durability, and resistance to wear and corrosion. The high silicon content improves flowability and reduces shrinkage during casting.
Lightweight: As with other aluminum alloys, ADC14 is lightweight, making it suitable for components where weight reduction is crucial, such as in automotive applications.
High Strength and Durability: It offers excellent strength and resistance to mechanical stress, making it ideal for structural and load-bearing parts.
Corrosion Resistance: It provides good resistance to corrosion, especially in harsh environments, which is critical for automotive and outdoor applications.
Thermal and Electrical Conductivity: Aluminum alloys, including ADC14, possess good thermal and electrical conductivity, making them suitable for heat sinks and electrical components.
Ease of Casting: ADC14 exhibits good fluidity and low shrinkage, allowing for intricate designs and high-precision manufacturing in high-pressure die-casting processes.
ADC14 Aluminum Equivalent
ADC14 aluminum alloy is part of the Japanese JIS standard (Japanese Industrial Standard) for die-casting aluminum alloys. Its equivalents in other international standards are commonly used for comparison and substitution purposes. Below are the equivalents of ADC14 in different standards:
Standard | Equivalent Alloy |
JIS (Japan) | ADC14 |
ASTM (USA) | A383 |
ISO (International) | Al-Si11Cu3(Fe) (226) |
EN (Europe) | EN AC-46500 |
DIN (Germany) | G-AlSi10Cu3(Fe) |
GB (China) | YL113 |
ADC14 Aluminum Chemical Composition
The chemical composition of ADC14 aluminum alloy is regulated to achieve its desired mechanical properties and casting performance. Below is the standard composition range for ADC14.
Element | Weight Percentage (%) |
Silicon (Si) | 11.0 – 13.0 |
Copper (Cu) | 1.5 – 3.5 |
Magnesium (Mg) | 0.10 – 0.30 |
Zinc (Zn) | ≤ 1.0 |
Iron (Fe) | ≤ 1.3 |
Manganese (Mn) | ≤ 0.50 |
Nickel (Ni) | ≤ 0.50 |
Tin (Sn) | ≤ 0.20 |
Lead (Pb) | ≤ 0.10 |
Other Elements | ≤ 0.30 (each) |
Aluminum (Al) | Balance |
Aluminum ADC14 Material Properties
The material properties of ADC14 aluminum alloy make it a popular choice for high-pressure die-casting applications, especially in industries like automotive and electronics. Below are its key properties:
- Mechanical Properties
High Tensile Strength: Provides excellent durability for load-bearing parts.
Moderate Elongation: Offers limited ductility, typical of high-pressure die-cast alloys.
Good Hardness: Ensures resistance to wear and abrasion. - Physical Properties
Lightweight: Its low density makes it ideal for weight-critical applications like automotive components.
Good Thermal Conductivity: Suitable for heat-dissipating components, such as heat sinks.
Moderate Electrical Conductivity: Often used in electrical enclosures and low-power applications.
Common ADC14 Aluminum Applications & Uses
- Automotive Industry: ADC14 aluminum is widely used in the automotive sector due to its lightweight, strength, and ability to handle mechanical stress. It is ideal for components like engine blocks, cylinder heads, transmission housings, brackets, and wheels. Its high thermal resistance also makes it suitable for heat-dissipating parts like radiator tanks and heat exchangers, contributing to fuel efficiency and performance in vehicles.
- Electronics and Electrical Industry: The good electrical and thermal conductivity of ADC14 makes it a popular material for electronics. It is used to manufacture heat sinks for cooling devices, enclosures for protecting electrical components, and connectors or switches. Its durability and corrosion resistance ensure reliability in challenging environments.
- Industrial Machinery and Equipment: In industrial applications, ADC14 is valued for its durability and precision. It is used for pump housings, gears, cams, and structural frames in machinery. Its wear resistance and ability to maintain dimensional stability even under stress make it ideal for heavy-use components.
- Consumer Goods: ADC14 is also used in consumer products due to its light weight and durability. It finds applications in appliance components for refrigerators, washing machines, and air conditioners, as well as in power tool casings and hardware for furniture. Its corrosion resistance ensures longevity in daily-use items.
- Aerospace Applications: Although not as common as in the automotive sector, ADC14 is used in aerospace for secondary components requiring lightweight and durable materials. Its strength-to-weight ratio and resistance to corrosion allow it to be employed in structural parts where weight reduction is critical.
- Marine Applications: ADC14’s corrosion resistance, especially when treated with protective coatings, makes it suitable for marine environments. It is used in boat structural parts and marine engine housings, where durability and resistance to saltwater exposure are essential for long-term performance.
ADC14 Aluminum Alloy Hardness & Density
The hardness of ADC14 aluminum alloy typically ranges between 85 and 110 HB (Brinell Hardness), depending on the casting process and heat treatment. Its density is approximately 2.7 g/cm³, which is characteristic of aluminum alloys, making it lightweight and suitable for applications where weight reduction is essential, such as in automotive and aerospace industries. These properties contribute to its strength, wear resistance, and overall versatility.
ADC14 vs ADC12, What’s the Difference?
- Chemical Composition
Alloy | Silicon (Si) | Copper (Cu) | Magnesium (Mg) | Zinc (Zn) | Iron (Fe) | Other Elements |
ADC14 | 11.0 – 13.0 | 1.5 – 3.5 | 0.10 – 0.30 | ≤ 1.0 | ≤ 1.3 | Slightly higher Cu |
ADC12 | 9.6 – 12.0 | 1.5 – 3.5 | ≤ 0.30 | ≤ 1.0 | ≤ 1.3 | Slightly higher Si |
- Mechanical Properties
Property | ADC14 | ADC12 |
Tensile Strength | ~250 – 310 MPa | ~260 – 320 MPa |
Yield Strength | ~140 – 160 MPa | ~150 – 160 MPa |
Elongation | ~1.5 – 3.0% | ~1.0 – 3.5% |
Hardness (HB) | ~85 – 110 | ~80 – 100 |
- Castability
ADC14: The higher silicon content enhances castability, making it ideal for complex shapes and thin-walled components.
ADC12: Good castability but slightly less fluid than ADC14. It is still widely used in die-casting processes for large-scale production. - Corrosion Resistance
ADC14: Better corrosion resistance due to higher silicon content, making it more suitable for harsh environments or marine applications.
ADC12: Slightly less corrosion-resistant but still performs well in most environments. - Applications
ADC14 Applications | ADC12 Applications |
Automotive: Engine blocks, heat exchangers | Automotive: Transmission housings, brackets |
Electronics: Heat sinks, enclosures | Consumer goods: Appliance parts, casings |
Marine: Structural components, housings | General-purpose die-cast parts |
ADC14 treatment process is usually not heat-treated; its properties are designed to perform well in the as-cast state. ADC12 treatment process can undergo some heat treatment (e.g., stress-relief annealing or aging) to enhance strength and stability, but drastic changes are limited due to its high silicon content.
Price
ADC14 has higher cost due to better castability, wear resistance, and corrosion resistance. While ADC12 has more affordable and preferred for general-purpose applications where extreme properties are not required.
Which is Better, ADC12 vs ADC14 Aluminum?
ADC12 and ADC16 are both popular aluminum alloys used in die-casting applications, but they differ in terms of composition and performance. ADC12 is known for its excellent castability, good corrosion resistance, and ease of machining, making it ideal for producing intricate parts with complex geometries, such as automotive and electronics components. It typically contains a higher percentage of silicon, which enhances fluidity during casting but makes it less strong compared to ADC16. ADC16, on the other hand, has a higher copper content, providing better mechanical strength, hardness, and wear resistance. It is often preferred for parts that require greater durability, such as engine components or structural parts. Overall, ADC12 is better for applications where casting precision and surface finish are crucial, while ADC16 is more suitable for parts requiring higher strength and resistance to wear. The choice between the two depends on the specific requirements of the application.