Aluminum is one of the most widely used materials for die casting, and ADC3 is a prominent aluminum alloy in the Al-Si-Mg system. This alloy includes aluminum, silicon, and magnesium as its primary components. ADC3 aluminum alloy die castings are known for their high impact resistance, endurance, and corrosion resistance. However, it is also recognized for having lower castability compared to other alloys. In this article, we will explore the composition, properties, and applications of ADC3, as well as compare it with ADC12.
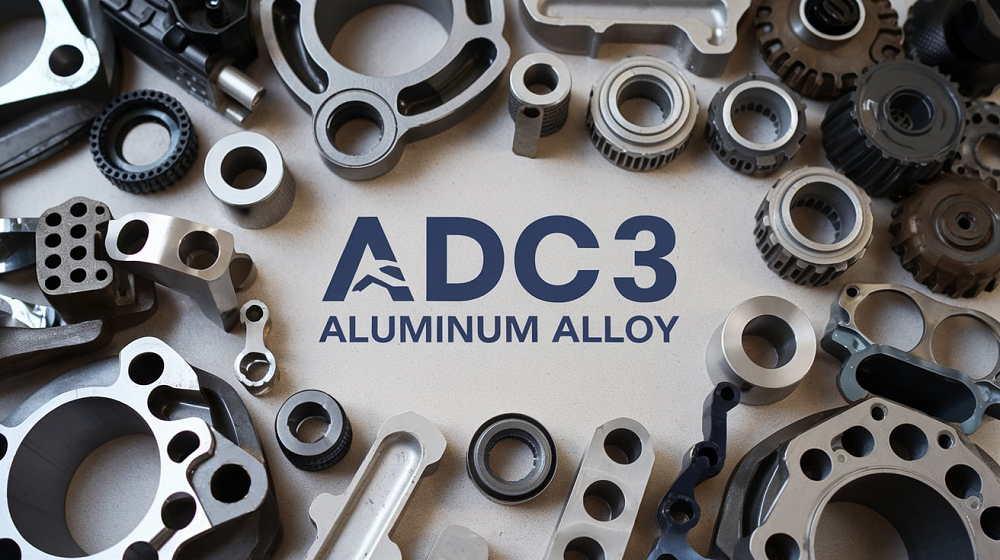
1. What is ADC3 Aluminum Alloy?
ADC3 is an aluminum alloy developed for die casting, primarily based on the aluminum-silicon-magnesium (Al-Si-Mg) system. Its main components are silicon (Si) and magnesium (Mg), which provide the alloy with excellent strength, corrosion resistance, and impact resistance. However, ADC3 is somewhat limited in castability compared to other aluminum alloys like ADC12 but excels in machinability and wear resistance.
Common Aluminum Alloys for Die Casting
Alloy System | Features | Main Alloys |
---|---|---|
Al-Si Series | Good castability | ADC1, ADC7 |
Al-Mg Series | Excellent corrosion resistance | ADC5, ADC6 |
Al-Si-Cu Series | High castability and strength | ADC10, ADC12 |
ADC3 is frequently used in the manufacturing of automotive, motorcycle, and bicycle parts, as well as outboard motor components due to its ability to withstand high temperatures, pressure, and mechanical stresses.
2. ADC3 Aluminum Chemical Composition
The composition of ADC3 is as follows:
- Copper (Cu): 0.6 – 1.0%
- Silicon (Si): 9.0 – 11.0%
- Magnesium (Mg): 0.3%
- Zinc (Zn): ≤ 0.5%
- Iron (Fe): ≤ 0.9%
- Manganese (Mn): ≤ 0.5%
- Chromium (Cr): ≤ 0.1%
- Nickel (Ni): ≤ 0.5%
- Tin (Sn): ≤ 0.1%
- Lead (Pb): ≤ 0.1%
- Titanium (Ti): ≤ 0.15%
- Aluminum (Al): Balance
ADC3 contains significant amounts of silicon and magnesium, with small amounts of copper, zinc, and iron to enhance its strength and machinability.
ADC Aluminum Alloy Chemical Composition Comparison
Here we list the following table to show the Chemical Composition of Aluminum Alloys for Die Casting (ADC1, ADC3, ADC5, ADC6, ADC10, ADC12, ADC14), to help you better understand their differences:

3. ADC3 Material Properties
ADC3 offers a strong balance of mechanical properties, making it suitable for a wide range of uses.
3.1. ADC3 Mechanical Properties
The mechanical properties of ADC3 are as follows:
- Young’s Modulus (Elastic Modulus): 71.0 GPa
- Tensile Strength: 320 MPa
- Yield Strength (0.2% Deformation): 170 MPa
- Elongation (50mm Test): 3.5%
- Impact Strength: 144 kJ/m²
- Shear Strength: 180 MPa
- Fatigue Strength: 120 MPa
- Hardness (HRB): 39 HRB
These properties confirm that ADC3 has excellent tensile and impact strength, making it suitable for demanding structural applications.
ADC3 Density
ADC3’s density is about 2.63 g/cm³, which is typical for aluminum alloys and contributes to its lightweight nature, making it ideal for automotive and aerospace applications where weight reduction is important.
3.2. ADC3 Physical Properties
ADC3 exhibits the following physical and thermal properties:
- Specific Heat Capacity: 963 J/(kg·K)
- Thermal Conductivity: 113 W/(m·K)
- Electrical Conductivity (Copper Base): 29% IACS
- Coefficient of Thermal Expansion (293K to 473K): 22 × 10⁻⁶/K
- Solidification Temperature: 596°C – 557°C
These properties indicate that ADC3 provides moderate thermal conductivity and a relatively high coefficient of thermal expansion, which is typical for aluminum alloys.
ADC3 Thermal Conductivity
ADC3 has a thermal conductivity of 113 W/(m·K), which is slightly lower than some other aluminum alloys. This makes it suitable for applications that require moderate heat dissipation, such as housings and enclosures.
ADC Aluminum Alloy Material Properties Comparison
Here we list the following table to show the Mechanical Properties of Aluminum Alloys for Die Casting (ADC1, ADC3, ADC5, ADC6, ADC10, ADC12, ADC14), to help you better understand their differences:
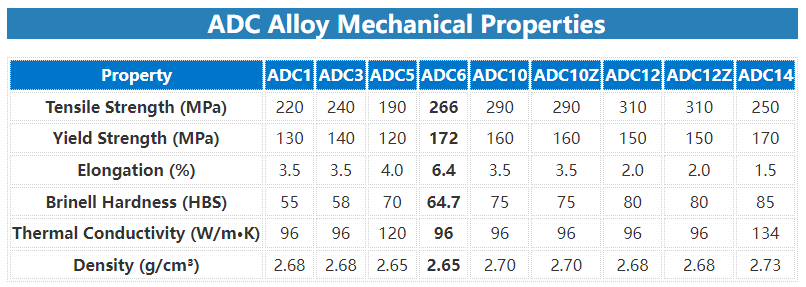
4. ADC3 Aluminum Equivalent Material
When looking for equivalent materials across different standards, a few notable substitutes for ADC3 include:
- A360.0 (USA, ASTM): This alloy offers high corrosion resistance and good casting characteristics, making it a common alternative to ADC3.
- EN AC-46000 (Europe, EN): Similar in composition and mechanical properties to ADC3, particularly in its silicon and copper content.
- AA 360 (USA, SAE): Classified under a different standard, this alloy is similar to A360.0 in its pressure tightness and die casting characteristics.
5. ADC3 Material Applications (Uses)
ADC3 is widely used in applications where high impact resistance, corrosion resistance, and strength are required. Typical uses include:
- Automotive Parts: Wheel caps, engine mount brackets.
- Motorcycle Parts: Crankcases, brackets, mufflers, and frames.
- Bicycle Parts: Wheels and frames.
- Outboard Motors: Propellers and casings.
Additionally, ADC3 is used in components like jet pump undercovers for jet skis and bodies for surveying equipment due to its strength, pressure resistance, and durability at high temperatures.
6. ADC3 vs ADC12 Aluminum, What is the Difference & Which is Better?
ADC3 and ADC12 aluminum alloys, both are commonly used in Japanese die-casting applications (under the JIS standard), the differences primarily lie in their chemical composition, mechanical properties, casting properties, and intended applications. Here’s a detailed breakdown:
6.1. Chemical Composition
Both ADC3 and ADC12 are aluminum-silicon-copper (Al-Si-Cu) based alloys, but their exact compositions differ, which leads to variations in their properties.
Element | ADC3 (%) | ADC12 (%) |
---|---|---|
Aluminum (Al) | Balance | Balance |
Silicon (Si) | 6.5 – 9.5 | 9.6 – 12.0 |
Copper (Cu) | 2.0 – 4.0 | 1.5 – 3.5 |
Magnesium (Mg) | ≤ 0.3 | ≤ 0.3 |
Iron (Fe) | ≤ 1.2 | ≤ 1.3 |
Zinc (Zn) | ≤ 1.0 | ≤ 1.0 |
Manganese (Mn) | ≤ 0.5 | ≤ 0.5 |
Nickel (Ni) | ≤ 0.5 | ≤ 0.5 |
Others | (Other elements ≤ small amounts) | (Other elements ≤ small amounts) |
Silicon (Si) content is higher in ADC12 (up to 12%) compared to ADC3 (up to 9.5%). Higher silicon content improves fluidity in casting and enhances wear resistance.
Copper (Cu) content is generally higher in ADC3 (up to 4%) compared to ADC12 (up to 3.5%). Increased copper improves strength and hardness but can reduce corrosion resistance.
6.2. Mechanical Properties
The differences in chemical composition lead to variations in mechanical properties.
Property | ADC3 | ADC12 |
---|---|---|
Tensile Strength (MPa) | ~220 | ~280 |
Yield Strength (MPa) | ~110 | ~160 |
Elongation (%) | ~4 – 7 | ~1 – 3 |
Hardness (HB) | ~70 – 80 | ~90 – 100 |
Density (g/cm³) | ~2.73 | ~2.74 |
- Tensile Strength and Yield Strength: ADC12 generally has higher tensile and yield strength compared to ADC3, making it more suitable for applications requiring higher load-bearing capacity.
- Elongation: ADC3 has better elongation (up to ~7%) than ADC12, making it more ductile and less brittle.
- Hardness: ADC12 is harder than ADC3, which makes it more wear-resistant but also more prone to cracking under stress.
6.3. Casting Properties
- ADC3: Due to its lower silicon content, ADC3 has slightly lower fluidity compared to ADC12, which can make it more challenging to cast complex shapes. However, it has better machinability and can achieve better surface finishes in post-casting processes.
- ADC12: Higher silicon content improves castability (fluidity), making it easier to fill intricate molds with thinner sections. This makes ADC12 more suitable for high-pressure die-casting and for manufacturing parts with complex geometries.
6.4. Corrosion Resistance
- ADC3: With higher copper content, ADC3 is slightly more prone to corrosion than ADC12, especially in environments with moisture or corrosive chemicals.
- ADC12: Due to its lower copper content, ADC12 generally has better corrosion resistance, making it suitable for applications exposed to moisture or chemicals.
6.5. Application Areas
- ADC3: Primarily used in applications where ductility, machinability, and surface finish are important. It’s often used for automotive parts (such as cylinder heads and pistons), electrical components, and machined components where post-casting machining is necessary.
- ADC12: More commonly used in automotive, electronic, and appliance housings due to its excellent castability and higher strength. It is ideal for complex and thin-walled parts, such as engine brackets, transmission cases, and large structural components.
6.6. Price and Availability
- ADC12 is often more readily available and widely used in mass-production die-casting processes due to its better castability and strength. It is generally more cost-effective for large-scale production.
- ADC3 may be slightly more expensive due to its specialized properties and lower production volume compared to ADC12.
ADC3 vs ADC12, Which is Better?
Based on the above comparison, we sort out the following chart to show which of these two ADC materials is better in different aspects, and you should take a look before choosing:
Factor | ADC3 | ADC12 |
---|---|---|
Tensile Strength | Lower (~220 MPa) | Higher (~280 MPa) |
Ductility (Elongation) | Higher (up to ~7%) | Lower (1 – 3%) |
Hardness | Lower (~70 – 80 HB) | Higher (~90 – 100 HB) |
Castability | Good, but lower fluidity | Excellent fluidity for thin/complex parts |
Machinability | Better, easier to machine | Harder to machine, more brittle |
Corrosion Resistance | Slightly lower (due to Cu) | Better (lower Cu content) |
Cost and Availability | Less common, possibly more expensive | Widely used, cost-effective in large volumes |
Typical Applications | Machined parts, automotive, electrical | Automotive, electronics, complex castings |
The choice between ADC3 and ADC12 depends largely on the specific requirements of your part and the operating conditions it will face:
- Choose ADC12 if:
- You need higher strength and wear resistance.
- Your part has a complex geometry or thin-walled sections, where castability is critical.
- Corrosion resistance is important.
- You are working on a large-scale production where cost and availability are key factors.
- Choose ADC3 if:
- You need better ductility and machinability for post-casting processes.
- The part requires some flexibility or impact resistance.
- The design is simpler and doesn’t require the extreme castability of ADC12.
- Surface finish and machinability after casting are priorities.
For ADC3 Die Casting, Leave It To DieCasting-Mould.Com!
We introduced the features of ADC3 aluminum die casting in this article. For high-quality die casting services involving ADC3 or other aluminum alloys, consider working with an experienced die casting provider who can help you choose the best material for your project.
Based on our track record of delivering aluminum die casting products to domestic and overseas auto parts, agricultural and forestry equipment parts, and housing equipment manufacturers, we offer a variety of proposals, including optimal material selection and conversion of construction methods to die casting. We accept die casting of ADC3, which has inferior castability but excellent impact value, strength, and corrosion resistance. We can also handle zinc and magnesium die casting in addition to aluminum.
Our Features:
- Improvement of internal quality and reduction of defect rate by using extrusion pin/gas vent pin.
- Die casting of high-performance aluminum alloys.
- Alloy development support for various development products.
If you have any problems with die casting, please feel free to contact us. Thank you for reading to the end!