A356.2 aluminum alloy is a specialized casting material widely recognized for its excellent casting properties and diverse applications, particularly in the automotive industry. This alloy is highly valued for its light weight, good corrosion resistance, and ease of welding, making it a popular choice for manufacturing high-performance, durable components. In this aluminum A356.2 guide, we’ll explain the advantages, uses, components and the differences between A356.2 and A356.1.
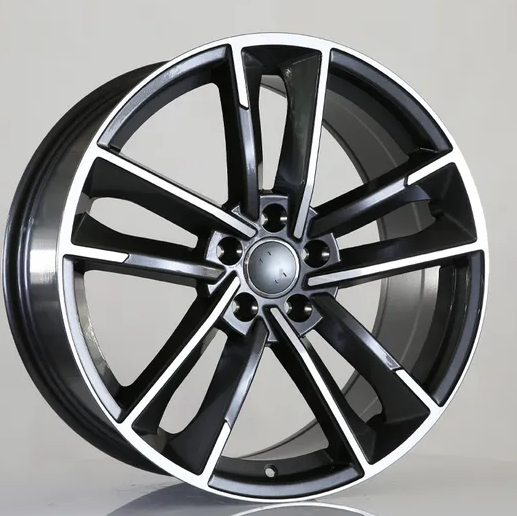
Characteristics of A356.2 Aluminum Alloy
A356.2 aluminum alloy offers several beneficial properties that enhance its versatility in casting applications:
- Good Fluidity and Low Shrinkage: A356.2 alloy has excellent fluidity, allowing it to fill complex molds with minimal shrinkage. This makes it ideal for producing intricate components with precise dimensions.
- High Air Tightness and Low Porosity: Components cast from A356.2 show excellent air tightness and a compact fracture surface, free from impurities and non-metallic inclusions, making it reliable for applications that require structural integrity.
- Corrosion Resistance and Lightweight: A356.2 has a relatively low density, making it suitable for lightweight applications. Its inherent corrosion resistance contributes to long-term durability, even in demanding environments.
- Strong and Adaptable: This alloy maintains strength without significant reduction as the wall thickness of the cast part increases. Moreover, it can be heat-treated to further enhance its mechanical properties, making it a flexible choice for different applications.
Applications of Aluminum A356.2
The primary use of A356.2 is in the production of lightweight yet strong components for various automotive and transportation applications. It is especially suited for:
- Automobile and Motorcycle Wheels: A356.2 is commonly used to produce wheels for cars, motorcycles, and other vehicles. Its lightweight and high-strength characteristics make it ideal for enhancing fuel efficiency while maintaining structural safety.
- Structural Components: Beyond wheels, A356.2 is used in other automotive parts and structural components where high durability and resistance to corrosion are required.
Chemical Composition of A356.2 Aluminum
The chemical composition of A356.2 alloy is in accordance with ASTM standards, as outlined below:
- Silicon (Si): 6.5 – 7.5%
- Magnesium (Mg): 0.30 – 0.45%
- Titanium (Ti): ≤ 0.2%
- Iron (Fe): ≤ 0.12%
- Manganese (Mn): ≤ 0.05%
- Copper (Cu): ≤ 0.1%
- Zinc (Zn): ≤ 0.05%
- Aluminum (Al): Balance
The silicon and magnesium content contribute to the alloy’s strength, castability, and fluidity, while maintaining a balance between ductility and toughness. The remaining elements, like titanium, iron, and manganese, are kept at low levels to minimize impurities and maintain the alloy’s overall quality and performance.
A356.2 VS A356.1 Aluminum Alloy, Which Is Better
The primary differences between A356.2 and A356.1 aluminum alloys lie in their mechanical properties, treatment requirements, and specific applications. Both alloys belong to the A356 series, which is known for its excellent castability, corrosion resistance, and strength-to-weight ratio. However, subtle distinctions in their properties and treatments make them suited to different needs.
1. Mechanical Properties and Performance
A356.2 is generally preferred over A356.1 for applications requiring enhanced mechanical strength and ductility. This difference is largely due to the additional heat treatment that A356.2 undergoes, typically in the form of a T6 temper, which increases its tensile strength and elongation capacity. As a result, A356.2 is more resistant to stress and strain, making it suitable for critical structural components like wheels and automotive parts that must endure high loads and impacts. In contrast, A356.1 is typically left in its “as-cast” condition, meaning it does not receive additional heat treatment after casting. While this makes it more affordable and efficient for certain applications, it generally has lower tensile strength and ductility compared to A356.2.
2. Heat Treatment and Aging
A key difference between A356.2 and A356.1 lies in their heat treatment process. A356.2 undergoes a T6 heat treatment, which involves solution treatment, quenching, and artificial aging. This process enhances the alloy’s yield strength and hardness, making it suitable for parts that require higher mechanical performance. In contrast, A356.1 is left in the as-cast condition, or F-temper, without undergoing additional heat treatment. This absence of treatment can be beneficial for components that do not require high strength but do need good castability and corrosion resistance.
3. Applications and Use Cases
Due to its enhanced strength and durability, A356.2 is widely used in the automotive and aerospace industries for parts that require reliability under stress, such as wheels, suspension components, and engine parts. The increased performance of A356.2 makes it ideal for applications where safety and load-bearing are essential. A356.1, on the other hand, is used in non-critical applications where cost efficiency and ease of manufacturing are prioritized over extreme mechanical strength. Examples include various non-load-bearing cast components, fittings, or parts where high ductility and machinability are not as critical.
4. Cost and Efficiency
A356.1, being left in its as-cast condition, can be more cost-effective and quicker to produce, as it bypasses the additional heat treatment steps that A356.2 requires. This makes A356.1 advantageous for applications that require high volumes at a lower cost, especially in parts that do not need the enhanced properties provided by T6 treatment. A356.2, while slightly more expensive due to the additional treatment, justifies the cost in applications demanding superior strength, making it more cost-effective over the lifespan of high-performance parts.