Clear anodized aluminum is a versatile and durable material that has gained popularity across various industries due to its unique properties. This metal undergoes an electrochemical process to form a transparent oxide layer on its surface, enhancing its natural characteristics. This process not only boosts aluminum’s corrosion and wear resistance but also preserves its sleek, metallic appearance. From architecture to consumer electronics, clear anodized aluminum is valued for both its functional and aesthetic benefits. With this aluminum guide, we’ll talk about the clear anodizing finish, its advantages and disadvantages, and its wide-ranging applications. We’ll also compare it with other finishes like satin anodized and mill finish aluminum to provide a comprehensive understanding of its uses and benefits.
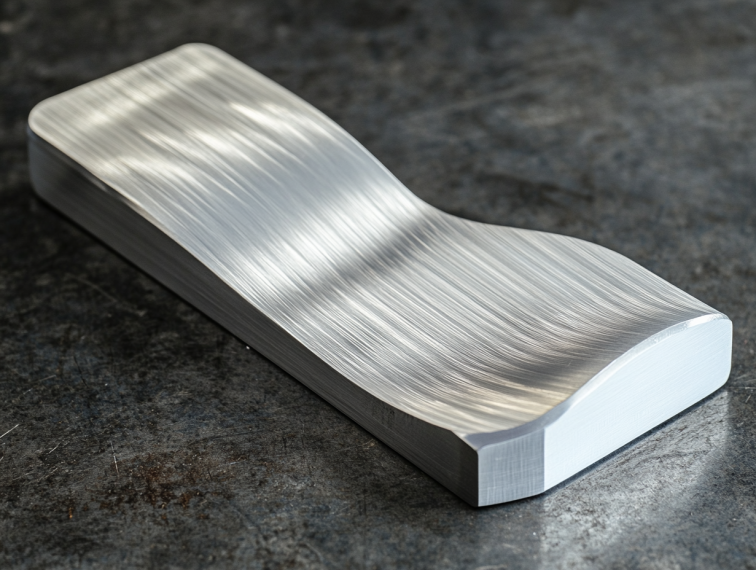
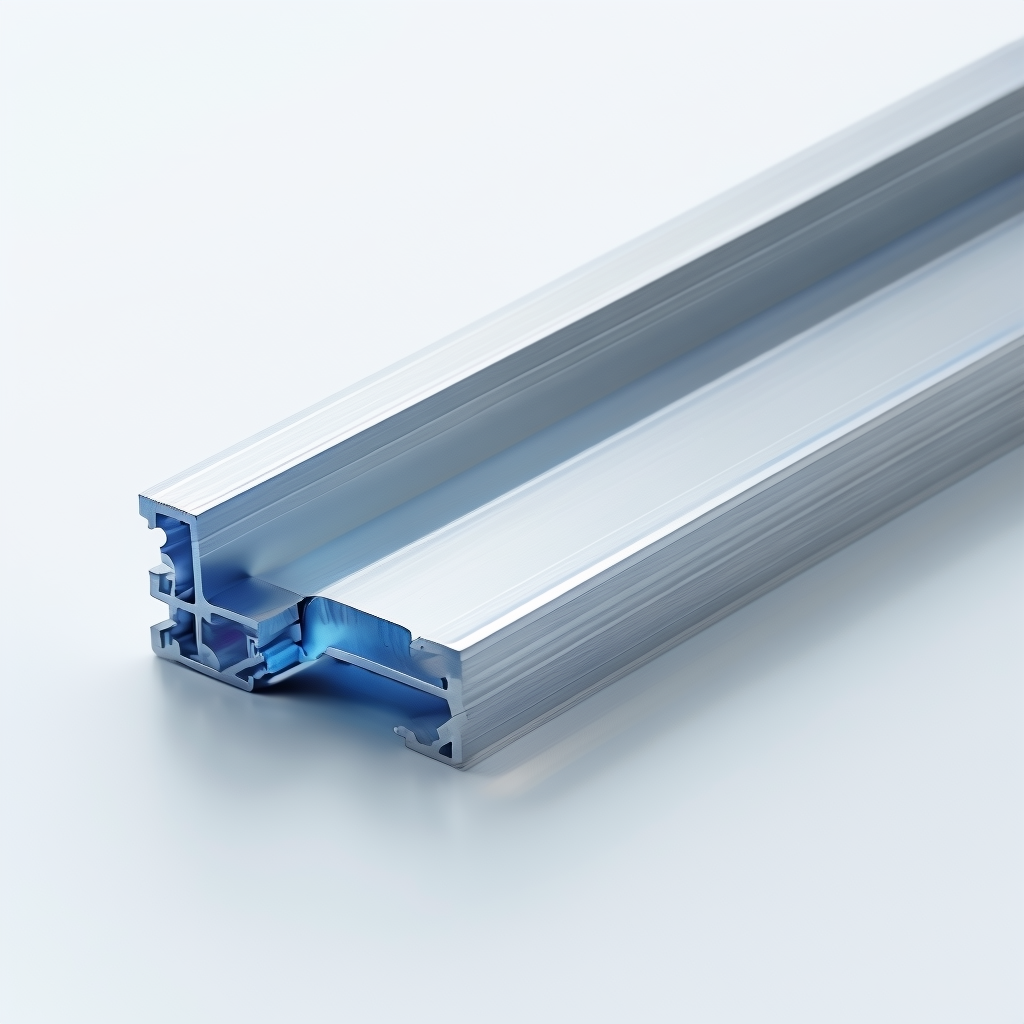
What is Clear Anodized Aluminum?
Clear anodized aluminum is aluminum that has undergone an anodizing process, creating a transparent, oxide layer on its surface. This oxide coating enhances the metal’s corrosion resistance, wear resistance, and surface hardness, making it ideal for long-term applications in harsh environments.
General Specifications
- Material:
- Base material: Aluminum alloys, such as:
- 5000 Series (e.g., 5052): High strength and corrosion resistance.
- 6000 Series (e.g., 6061, 6063): Good strength and machinability.
- Base material: Aluminum alloys, such as:
- Anodized Layer Thickness:
- Typical thickness: 5 to 25 microns (0.005–0.025 mm).
- Thickness depends on the application:
- 5–10 microns: Indoor use or decorative purposes.
- 15–25 microns: Outdoor use or in corrosive environments.
- Surface Appearance:
- Clear, transparent finish that retains the natural metallic look of aluminum.
- Can be matte or shiny, depending on pre-treatment (e.g., etching or polishing).
- Standard Compliance:
- Meets various anodizing standards, including:
- MIL-A-8625F: U.S. military specification for anodized aluminum.
- ISO 7599: International standard for anodizing aluminum.
- AA-M12C22A31: Aluminum Association designation for clear anodizing.
- Meets various anodizing standards, including:
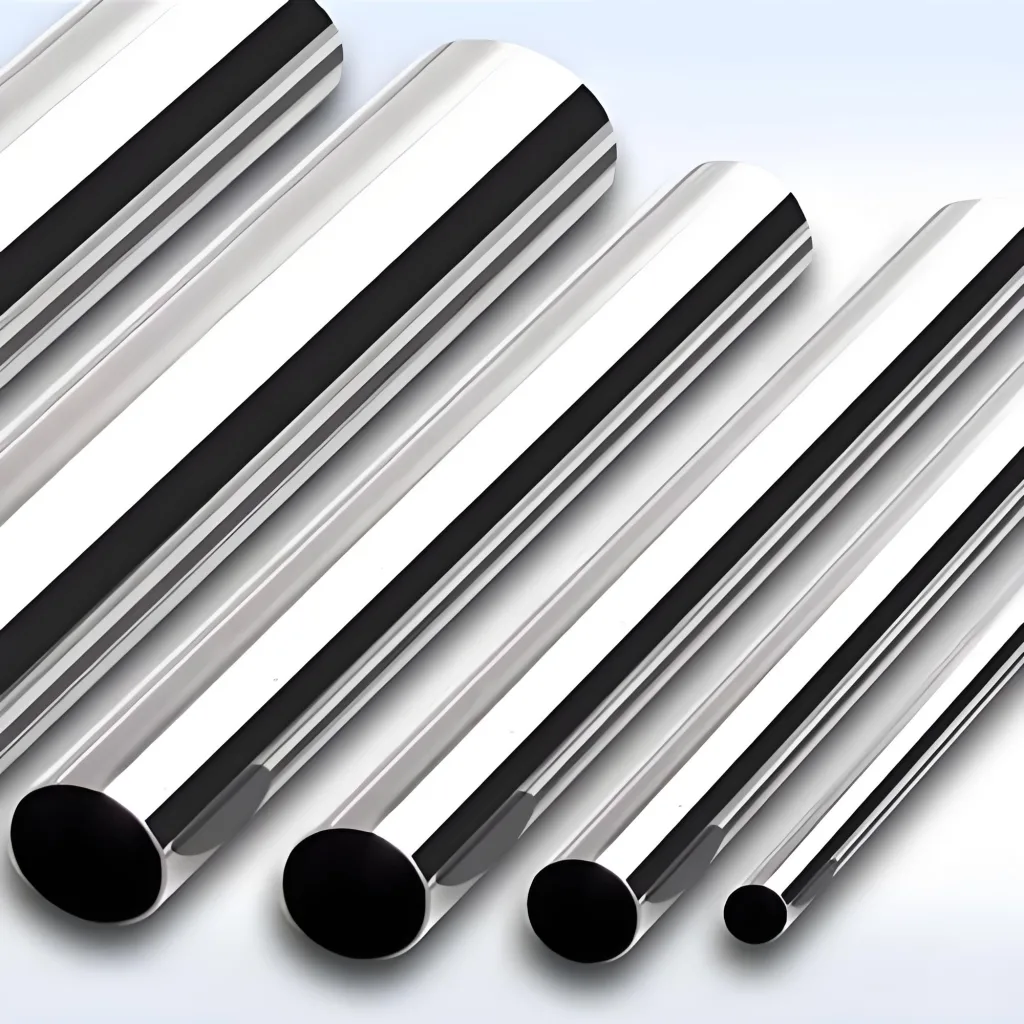
What is Clear Anodizing Finish?
Clear anodizing is a process using electrochemical reactions to treat the surface of metals (mainly aluminum and its alloys) to form a colorless, transparent oxide film. This enhances the material’s appearance and improves its corrosion resistance and other properties.
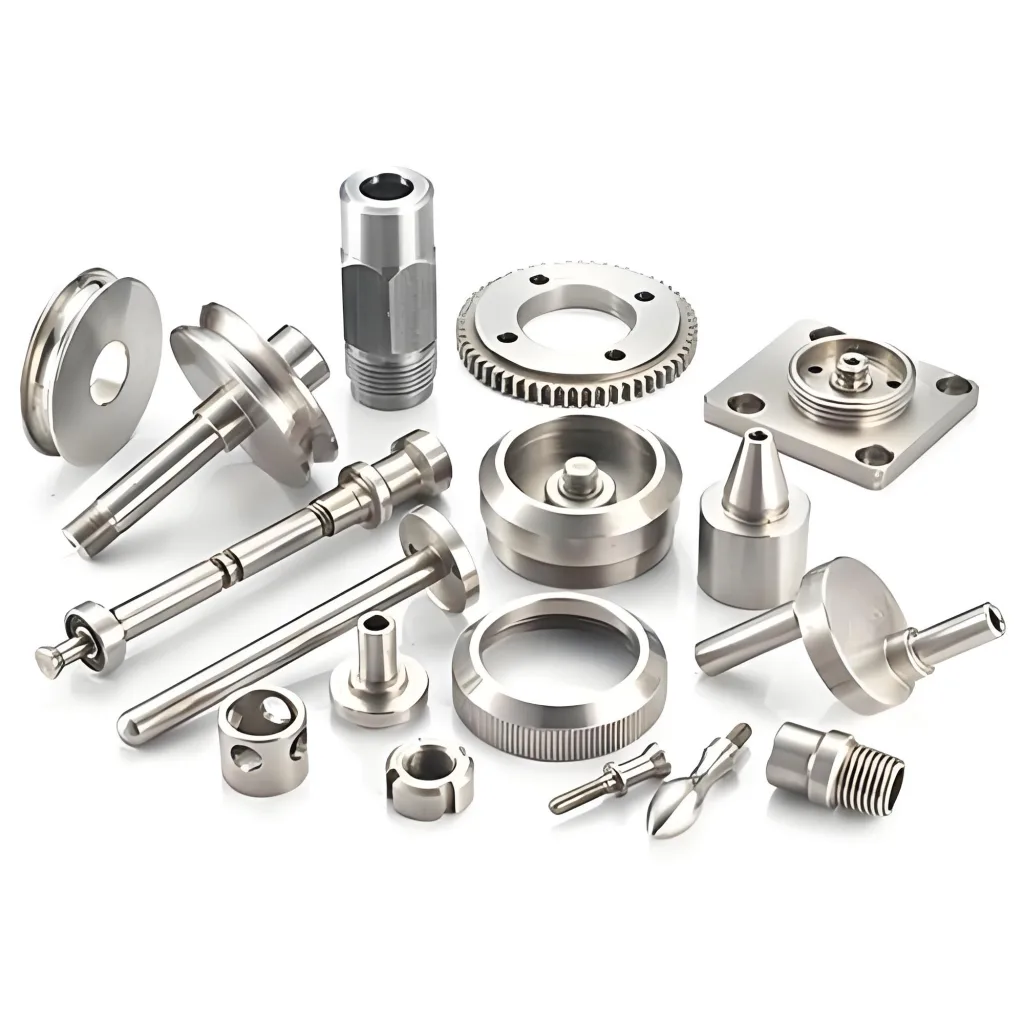
Clear Anodizing Aluminum Color
What color is clear anodized? Clear anodized aluminum typically has a silver or natural metallic appearance. The anodizing process enhances the metal’s natural characteristics, resulting in a smooth, matte finish. It doesn’t add any color, so it maintains the base metal’s look.
Clear Anodized Aluminum Process
The detailed steps and technical requirements of the clear anodized aluminum process are as follows:
- Cleaning: To remove oil, dust, and the natural oxide layer from the surface of aluminum alloys, parts are soaked in a degreaser (such as R105) followed by rinsing with clean water.
- Alkali Etching: For further removal of surface impurities and complete elimination of the natural oxide layer, aluminum materials are placed in a sodium hydroxide solution for an etching reaction at controlled temperatures of 70-90°C.
- Chemical Polishing: To remove contaminants and the natural oxide layer, and to improve surface smoothness, a chemical polishing solution is used.
- Activation: To provide a uniform conductive base for subsequent anodizing, a specific electrolyte is used for activation.
- Anodizing: In the electrolytic solution, aluminum serves as the anode, and upon electrification, an oxide layer (Al2O3 layer) is formed on the aluminum surface. Sulfuric acid is used as the electrolyte, with a current density of 2-4.5 A/dm², a voltage range of 23-100 V, and temperature controlled at 2°C or higher, with treatment times typically over 60 minutes. Specific parameters include a use temperature of ±25°C, free sulfuric acid concentration of 150-210g/L, and treatment time of 3-15 minutes.
- Rinsing and Neutralization: To remove residual acidic substances and prevent interference with subsequent dyeing processes, rinse multiple times with clean water to ensure no sulfuric acid residue remains.
- Coloring: Place the anodized aluminum parts in a dye solution, allowing the dye to be adsorbed into the pores of the oxide film. Dyeing must be completed within 24 hours.
- Sealing: Place the anodized or colored aluminum panels in a sealing solution to close the micropores, enhancing corrosion resistance and sealing performance. Cold wind or moderate temperature sealing processes are used.
- Drying: After rinsing clean with water, air-dry or hang to dry.
Clear Anodized Aluminum Advantages and Disadvantages
Here are the advantages and disadvantages of clear anodized aluminum:
✅ Key Advantages
- ✔Improved Corrosion Resistance: The dense oxide layer formed on the surface of anodized aluminum isolates air and moisture, significantly enhancing the aluminum’s corrosion resistance.
- ✔High Hardness: The surface of anodized aluminum forms a protective layer harder than the substrate itself, enhancing material wear resistance and mechanical strength.
- ✔Aesthetic Appeal: Clear anodized aluminum retains the natural soft metallic texture of aluminum and can achieve a variety of colors through dyeing, making it visually more appealing.
- ✔Good Processability: Clear anodized aluminum is easy to process, can be easily bent into shape, and is suitable for various complex-shaped applications.
- ✔Weather Resistance: Does not change color, corrode, oxidize, or rust over long-term use, demonstrating excellent weather resistance.
- ✔Environmentally Friendly: Compared to other surface treatment methods, the anodizing process has less environmental impact, making it a more environmentally friendly choice.
❌ Potential Disadvantages
- ✖Limited Color Choices: Although clear anodized aluminum can achieve various colors through dyeing, its color choices are relatively limited and cannot be freely chosen.
- ✖Brittleness: Although the surface of anodized aluminum has high hardness, it is relatively brittle and prone to cracks or damage under external forces.
- ✖Higher Cost: Compared to other surface treatment methods, the production cost of anodized aluminum is relatively high, especially during large-scale production.
Clear Anodized Aluminum Applications
Clear anodized aluminum is widely valued for its aesthetic appeal and protective qualities, making it a popular choice across various industries. Here’s how clear anodized aluminum is applied across different fields:
- 🏢Architectural and Construction
Exterior Panels & Facades – Weather-resistant, durable, and stylish. Windows & Door Frames – Protects against corrosion and enhances appearance. Roofing & Structural Components – Ensures longevity and strength.
- 🚗Automotive Industry
Decorative Trim and Functional Components: Used in both interior and exterior parts of vehicles for its resistance to wear and its aesthetic quality.
Engine Components: Its heat-resistance qualities make it suitable for various engine parts.
- 📱Consumer Electronics
Enclosures for Devices: Popular in laptops, tablets, and other portable electronics for its sleek finish and robust nature.
Audio Equipment: Utilized in casings for speakers and other audio devices to provide a durable, yet attractive exterior.
- 🍳Kitchenware and Appliances
Cookware: Clear anodized aluminum is used in pots, pans, and utensils as it is non-toxic and heat resistant.
Appliance Components: Provides a scratch-resistant surface that is easy to clean and maintain.
- ✈Aerospace
Interior Cabin Components: Used for parts within the cabin for its lightweight nature and corrosion resistance.
Exterior Panels: Ensures durability and resistance to harsh atmospheric conditions.
- 🏋️♂️Sporting Goods
Outdoor Equipment: Ideal for camping gear and bicycle components due to its lightweight and durable properties.
Golf Clubs and Baseball Bats: Enhances the wear resistance and appearance of sports equipment.
- 🔭Optical Equipment
Telescopes and Camera Housings: Used to protect against environmental exposure and mechanical wear while ensuring lightweight properties.
Clear anodized aluminum is also favored for its environmental benefits, as the anodizing process is relatively eco-friendly and the materials are recyclable. This makes it an excellent choice for applications requiring long-lasting, aesthetically pleasing, and environmentally responsible materials.
Satin Anodized vs Clear Anodized, What is the Difference?
Both satin anodized and clear anodized finishes are used to protect and enhance aluminum surfaces, but they have different appearances and applications:
Satin Anodized
- Appearance: Has a matte finish with a subtle sheen.
- Texture: Smooth but not shiny, reducing glare.
- Applications: Used in architectural projects and consumer products where a less reflective surface is desired.
- Advantages: Hides fingerprints and minor scratches well.
Clear Anodized
- Appearance: Transparent finish that maintains the natural look of aluminum.
- Texture: Glossy and smooth, showing the metal’s original luster.
- Applications: Common in architectural components and electronics that require a clean, metallic appearance.
- Advantages: Provides a durable, corrosion-resistant layer without altering the metal’s appearance significantly.
Mill Finish Aluminum vs Clear Anodized: What is the Difference?
Mill finish aluminum is another popular finish used for aluminum products, refers to the finish of aluminum directly after it has been extruded or rolled without any further treatment. The main differences between mill finish aluminum and clear anodized aluminum are:
- Surface finish – Mill finish aluminum has a dull, matte finish from the manufacturing process. Clear anodized aluminum has a smoother, more uniform surface finish.
- Corrosion resistance – Clear anodized aluminum has greater corrosion resistance than mill finish aluminum due to the anodizing process. Anodizing creates a protective oxide layer on the surface.
- Hardness – Clear anodized aluminum is slightly harder than mill finish aluminum due to the anodized layer.
- Appearance – Mill finish aluminum has a gray, metallic color. Clear anodized aluminum has a more uniform, shiny appearance while still showing the natural aluminum color.
- Cost – Clear anodized aluminum is more expensive than mill finish aluminum due to the extra processing steps required.
- Uses – Mill finish aluminum is often used in industrial/structural applications where appearance is not critical. Clear anodized aluminum has more applications where aesthetics and corrosion resistance are important such as architecture, consumer products, etc.
Clear Anodized vs. Satin Anodized vs. Mill Finish Aluminum
Feature | Clear Anodized Aluminum | Satin Anodized Aluminum | Mill Finish Aluminum |
---|---|---|---|
Appearance | Transparent, metallic | Matte, subtle sheen | Dull, unfinished |
Texture | Glossy or matte | Smooth, low reflection | Rough, unpolished |
Durability | High corrosion resistance | Hides minor scratches | Low corrosion resistance |
Applications | Architectural, electronics | Consumer products, architecture | Industrial, structural |
Cost | Higher | Medium | Lower |
Which One to Choose?
- Clear Anodized: Best for modern, high-end applications requiring durability and aesthetics.
- Satin Anodized: Ideal for low-gloss, fingerprint-resistant finishes.
- Mill Finish: Suitable for industrial applications where appearance is not a priority.
Why Choose Clear Anodized Aluminum?
Clear anodized aluminum is an exceptional choice for industries requiring durable, attractive, and corrosion-resistant materials. Whether for architecture, automotive, aerospace, or consumer electronics, it provides long-lasting performance and modern aesthetics.
Looking for custom clear anodized aluminum parts? Contact Junying Metal Manufacturing Co., Limited, a leading provider of die-casting, CNC machining, and surface finishing services.