What is Die Casting Machine - Types of Die Casting Machine | Diecasting-mould
Die casting is a process employing the pressure to inject molten metal into a mold or die, then to obtain the casting products that have exact shapes or geometries as the internal shape of the mould. In this article, we’ll talk about the equipment for this process, what is die casting machine and common types of die casting machines, as well as their mechanism and selection.
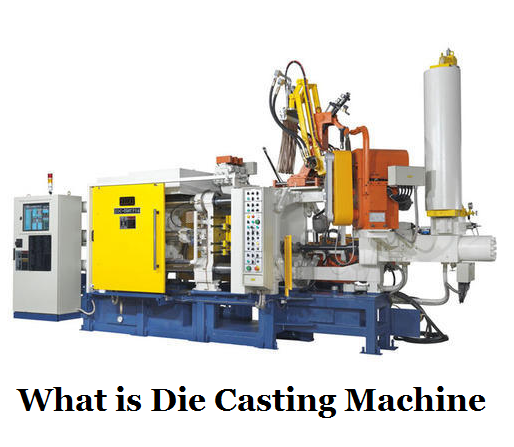
What is Die Casting Machine?
Die casting machine is used for the metal casting process, through which the molten metal is injected into the mold cavity, the shape of the die casting parts will be formed when the metal is cool and solidified, this is a manufacturing method to get metal castings like aluminum or zinc die castings.
How Does a Die Cast Machine Work?
A die cast machine works by injecting molten metal, such as aluminum, zinc, or magnesium, into a precisely machined steel mold (called a die) under high pressure to form complex and accurate parts. The process begins with clamping the die halves together, then a furnace or shot sleeve feeds molten metal into the injection chamber. A plunger or piston forces the metal into the die cavity at pressures ranging from hundreds to thousands of psi, ensuring it fills even fine details. Once the metal solidifies within seconds, the die opens, ejector pins push the casting out, and the cycle repeats rapidly, making die casting ideal for high-volume, dimensionally consistent production.
Die Cast Machine Properties
Here are the key properties of a die casting machine, which determine its performance, efficiency, and suitability for specific applications:
1. Clamping Force
Definition: The force used to keep the mold closed during injection.
Importance: Prevents mold separation under high injection pressure.
Range: Typically 20 to 5000 tons depending on machine size.
2. Injection Pressure & Speed
Injection Pressure: The hydraulic force applied to inject molten metal into the mold cavity (up to 1500 bar or more in high-pressure die casting).
Injection Speed: Determines how quickly metal fills the mold; critical for thin-walled parts.
3. Shot Capacity
Definition: Maximum amount of molten metal the machine can inject in a single shot.
Units: Measured in kg or cm³.
Impact: Must match part size and mold design requirements.
4. Die Locking Mechanism
Types: Toggle-type or direct hydraulic.
Significance: Impacts cycle time, machine durability, and energy efficiency.
5. Automation Compatibility
Many modern machines include automatic ladling, spraying, and part extraction systems to improve productivity and consistency.
6. Cycle Time
Definition: Time taken for one full operation (clamping, injection, solidification, and ejection).
Impact: Shorter cycle time increases production efficiency.
7. Accuracy & Repeatability
Importance: Ensures consistent part dimensions, critical for precision industries like automotive and electronics.
Factors: Machine rigidity, injection control, and temperature stability.
8. Energy Consumption
Hydraulic vs. Servo-Hydraulic: Servo-driven machines are more energy-efficient.
Relevance: Affects operating costs and environmental impact.
9. Durability & Maintenance
Material Quality: Machine frames and platens must withstand repeated high-pressure cycles.
Ease of Maintenance: Access to components for quick repairs reduces downtime.
10. Safety & Control Systems
Modern machines feature PLC controls, touchscreens, sensors, and real-time monitoring for safe and optimized operation.
Diecast Machine Applications
Die casting machines are used to produce high-precision, complex metal parts at high volumes. Their applications span multiple industries due to their ability to produce parts with excellent dimensional accuracy, smooth surface finish, and repeatability. Key applications include:
1. Automotive Industry
2. Electronics & Electrical Industry
3. Aerospace & Aviation
4. Industrial & Machinery
5. Consumer Products
6. Renewable Energy
Types of Die Casting Machine
Die casting machines can be divided into different categories according to different classification methods, such as application and size. Generally, die casting machines can be classified into two types: hot chamber and cold chamber.
Hot Chamber Die Casting Machine
Hot chamber machines have a pressure chamber connected to the mold cavity, the molten metal can flow to the pressurized compartment continuously. When the chamber’s cylinder reverts to an unpressurized position, molten metal is fed into the casting die. The crucible for melting metal is attached to the machine, and the piston mechanism for hydraulic injection of metal into the mold is installed in the crucible. Some hot chamber die casting machines use compressed air to directly press metal into the mold, the piston mechanism is not needed. The injection mechanism is submerged in the molten metal, so it’s necessary to avoid chemical attack or erode to the submerged injection system. Hot chamber die casting machine is mainly used for casting zinc, tin and other alloys with a low melting point.
Advantages of hot chamber die casting machine
– High productivity
– Improved surface finish
– Capable of production of intricate castings
– Close dimensional tolerance
– Suitable for making zinc die casting parts
Cold Chamber Die Casting Machine
In a cold chamber machine, molten metal from a separate holding furnace is ladled into the cold chamber sleeve after the mold is closed. Then the metal is forced into the die, open the mold after solidification, the casting part will be injected. The metal is melted outside the machine, and then is added into the compression chamber. According to the moving direction of the compression piston, it can be divided into vertical cold chamber die casting machine and horizontal cold chamber die casting machine. The molten metal is taken out from the furnace of the vertical cold chamber die casting machine and poured into the compression chamber. The metal is injected into the mold by the compression piston, and the surplus metal is pushed out by another piston. Horizontal cold chamber die casting machine is working in the same method as vertical die casting machine, but the movement direction of piston is horizontal. Most modern die casting machines are horizontal. Cold chamber die casting machine can die-casting metal with high melting point, such as copper alloy.
Advantages of cold chamber die casting machine
– Reduced chance of corrosion
– Suitable for casting aluminum, copper and their alloys
– Can be used for manufacturing large parts
Which type of die casting machine you should choose? You can select the machine based on what metals you want to use. For example, if you are going to obtain zinc, tin, and lead castings, you should choose a hot chamber die casting machine, because it’s easy to suffer from corrosion and more suitable for alloys with low melting temperature and proper fluidity. In addition, the high temperature used in casting aluminum and copper alloys will shorten the life of hot chamber machines. On the contrary, cold chamber casting machines are more suited to casting high melting-point metals like aluminum or alloys with a high aluminum content.
Die Cast Machine Price
Price Ranges for Die Casting Machines
Hot Chamber Die Casting (new or used):
Smaller machines (~10 tons): around US $30,000
Larger units (up to 1,200 tons): over US $1,000,000
Aluminum Cold Chamber Die Casting Machines (used):
Around 100 tons: starting from US $80,000.
Very large models (up to 4,500 tons): can reach US $3,000,000 or more
New Entry-Level Units (e.g., from manufacturers in China):
30-ton high-pressure die casting machine: about US $26,900–29,600
Mid-range to larger setups:
60-ton hot chamber: US $26,900–36,000
200-ton hot chamber: US $52,500–70,200
220-ton cold chamber: US $49,980
700-ton cold chamber: US $126,560–156,000
Online Market & Auctions (e.g., MachineTools listings):
Used machines like a 399-ton Buhler H-400 SC: about £11,179 GBP (~US $14,000).
A 630-ton Buhler H-630 B: around £18,632 GBP (~US $23,000).
Higher-tonnage units cost more—for example, Toshiba DC650J-MS (601 tons) is listed at around.