Grey cast iron is one of the most used materials for casting and machining. The versatility of gray cast iron makes it suitable for a wide range of uses in various industries! Why is it so good? Let’s take a detailed understanding of grey iron by breaking down its chemical composition (microstructure), physical & mechanical properties, characteristics, application, casting process, and the differences between grey iron and ductile iron!
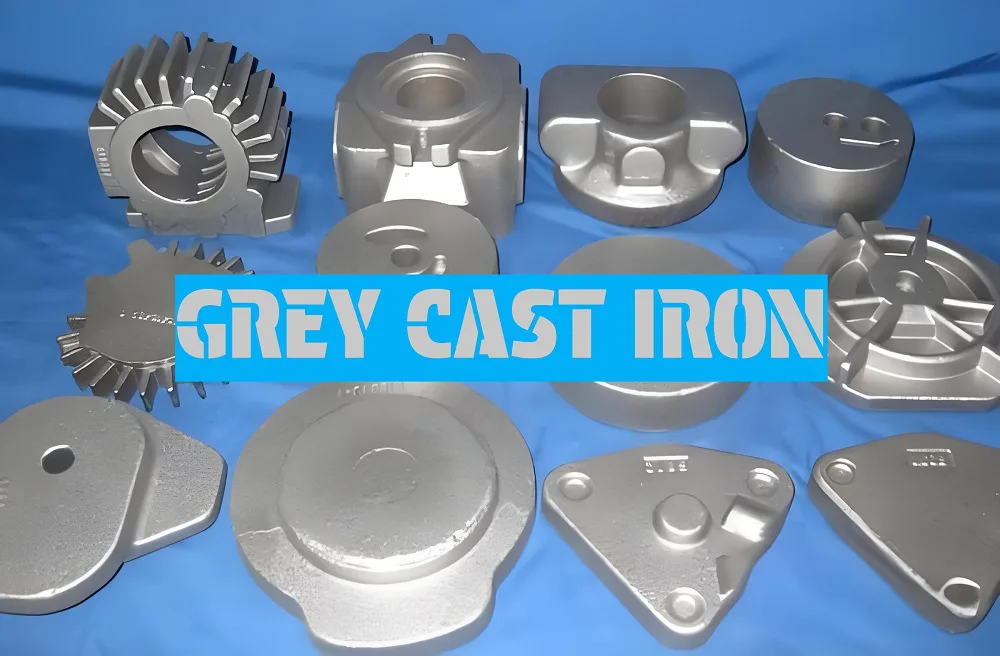
What is Grey Iron?
Grey iron is a type of cast iron, so also known as Grey Cast Iron that contains flake-like graphite, and its name varies depending on the base structure. The name “gray” comes from the fact that the fracture surface is gray, or mouse-colored. Cast iron is an iron-carbon alloy with a high carbon content, and by definition contains 2.06 to 6.67% carbon. Gray cast iron is a material classified as ordinary cast iron among cast iron products.
Grey cast iron is abbreviated as FC, which is the abbreviation of iron (Fe) and casting, and a three-digit number indicating the tensile strength is written after FC. For example, FC150 means that the tensile strength of this gray cast iron is at least 150. It is called “flake graphite cast iron” because the graphite resembles a collection of petals. When gray cast iron and white cast iron are mixed and the fracture surface appears as black and white spots, it is sometimes called “mottled cast iron.
Grey Cast Iron Composition (Microstructure)
The main components of gray cast iron are iron (Fe) and carbon (C), but it also contains silicon (Si), manganese (Mn), phosphorus (P), and sulfur (S). Below is main chermical compostion:
- Iron (Fe): 80%+ (The main component of gray iron, providing the matrix structure of the material)
- Carbon (C): 2.5 % ~ 4.0% (The carbon content significantly affects the performance of grey iron, Carbon exists in the form of graphite, influencing the material’s strength and hardness)
- Silicon (Si): 1.0% ~ 3.0 % (Improves castability and heat resistance)
- Manganese (Mn): 0.25% ~ 1.0% (Enhances strength and wear resistance)
- Phosphorus (P): 0.05% ~ 0.5% (Improves fluidity and machinability)
- Sulfur (S): 0.02% ~ 0.2% (Decreases fluidity and strength, increases brittleness)
Grey Cast Iron Properties
As the carbon content increases, the hardness also increases; thus, the properties change depending on which components are more prevalent. The basic properties of gray cast iron are as follows:
Grey Iron Mechanical Properties:
- Tensile Strength σb (MPa): 100 ~ 250 MPa (If treated with inoculation, the tensile strength can reach 250 ~ 400 MPa)
- Yield Strength σs (MPa): 150 ~ 300 MPa
- Conditional Yield Strength σ0.2 (MPa): 100 ~ 250 MPa
- Elongation δ (%): 0.3 ~ 0.8%
- Impact Toughness αkv (J/cm²): 2 ~ 5 J/cm²
- Creep Rate VG (%): 0.1 ~ 0.5%
- Deflection f (mm): 1 ~ 3 mm
- Brinell Hardness (HBS100/3000): 170 ~ 300 HB
Grey Iron Physical Properties:
- Young’s Modulus: 130 GPa
- Density: 7300 kg/m³
- Poisson’s Ratio: 0.25
Grey Cast Iron Processing Methods
Gray cast iron is a material that is widely used as a machine part and structural material because of its excellent workability. We process it in various ways even for the production of test pieces, which is often requested at Disecasting-Mould.Com.
Here, we will explain the characteristics of casting, milling, lathe machining, polishing, and electric discharge machining, which are the typical methods used for cutting and processing test pieces of gray cast iron.
- Casting: Easy to cast machine tool beds and tables, engine blocks, machine bases, pipes, gear housings, brake components, and cookware.
- Milling: Can process complex shapes such as flat surfaces, curved surfaces, and grooves.
- Lathe machining: Suitable for machining cylindrical and conical shapes.
- Electric discharge machining: Can process hard materials (difficult-to-cut materials) and complex shapes.
- Polishing: Improves flat surface smoothness. Dimensional control is possible in microns.
We can process grey cast iron using some of its processing machines (cutting machines, general-purpose machines, machining centers, NC lathes, surface grinders, and electric discharge machines) according to the request. Regarding the production of parts and jigs, consultation is required depending on the size and quantity.
Grey Iron Casting Process
Although grey iron has good mechanical properties and can be used in a variety of processing methods, its most commonly used processing method is casting. Its casting process mainly includes mold making, raw material preparation, smelting, pouring, cooling, demoulding, cleaning and heat treatment:
- First of all, mold making is the first step in the casting process, and its main purpose is to ensure the accuracy and surface quality of gray cast iron castings. The mold is usually made of materials such as gypsum, sand, graphite, etc., depending on the shape and size of the casting.
- Secondly, raw material preparation refers to the mixing of molten iron, pig iron, scrap steel and other additives in a certain proportion to make the raw materials of gray cast iron. This process is very important and determines the chemical composition and mechanical properties of the final casting.
- Then, smelting is the process of melting the raw materials at high temperature, usually in an electric arc furnace or furnace. During smelting, the temperature and melting time should be controlled to fully melt the raw materials and ensure the quality of the casting.
- Next, pouring is the process of pouring molten iron into the mold. During this process, care should be taken to avoid the generation of bubbles and inclusions to ensure the compactness and surface quality of the casting.
- Then, cooling and demolding are indispensable links in the casting process. A series of physical and chemical changes will occur in the casting during the cooling process, so the cooling rate should be controlled to avoid cracks and defects. When demolding, care should be taken to avoid damage to the surface of the casting.
- Finally, cleaning and heat treatment are the last two links in the casting process. Cleaning is to remove the oxide scale and residue on the surface of the casting to facilitate heat treatment. Heat treatment is the process of heating, heat preservation and cooling the gray cast iron casting to improve the mechanical properties and wear resistance of the casting.
Grey Cast Iron Applications
Grey cast iron has low friction due to the flake graphite acting as a lubricant, giving it excellent wear resistance. This makes it suitable for parts that experience significant wear, such as machine components and tools. Additionally, the flake graphite facilitates the escape of cutting tool edges and easily breaks up chips, making it a good material for machining. Compared to steel, it is easier to machine, allowing for the production of complex-shaped components.
However, some machining contractors may refuse to process grey cast iron. This is because the graphite contained in it can accumulate inside machine tools, adversely affecting their operation and machining accuracy. It is advisable to confirm in advance whether they can handle your request.
Given its excellent wear resistance and machinability, gray cast iron is used in the following applications:
- Machine Parts: Cylinder blocks, crankshafts, bearings, gears, camshafts, etc.
- Tools: Cutting tools, grinding tools, molds, etc.
- Household Items: Frying pans, pots, etc.
Grey Cast Iron Grades & Types
Grey cast iron grades are typically classified based on their mechanical properties and the strength of the iron. Here’s a detailed look at the grades and types of grey cast iron worldwide:
Certainly! Adding the China National Standards (GB) for grey cast iron to the table will provide a more comprehensive overview, especially for users dealing with international specifications. Here’s the updated table including the GB grades:
Standard | Grade | Minimum Tensile Strength | Application Examples |
ASTM A48 Defines unalloyed grey cast iron grades based on minimum tensile strength for general applications in the U.S. | Class 20 | 20 ksi | Gear boxes, engine blocks, machine bases |
Class 25 | 25 ksi | Counter weights, pump housings | |
Class 30 | 30 ksi | Valve bodies, pistons, bearing caps | |
Class 35 | 35 ksi | High-strength applications, heavy-duty gears | |
EN 1561 European standard specifying properties of unalloyed grey cast iron, focusing on hardness and wear resistance. | EN-GJL-150 | 150 MPa | General engineering, housing frames |
EN-GJL-200 | 200 MPa | Engine blocks, manifolds | |
EN-GJL-250 | 250 MPa | Heavy-duty gears, flywheels | |
EN-GJL-300 | 300 MPa | Press frames, stressed engine parts | |
EN-GJL-350 | 350 MPa | Highly stressed components in machinery | |
ISO 185 International standard that categorizes grey cast iron based on tensile strength for global applications. | ISO 185/150 | 150 MPa | Frames, housings, medium-strength applications |
ISO 185/200 | 200 MPa | Construction equipment, road machinery | |
ISO 185/250 | 250 MPa | Industrial machines, high-strength parts | |
ISO 185/300 | 300 MPa | Stressed parts in machinery and engines | |
JIS G5501 Japanese standard for grey cast iron, defining grades similar to ASTM and ISO for use primarily in Asia. | FC150 | 150 MPa | Pipes, machine parts, general castings |
FC200 | 200 MPa | Motor blocks, pumps, general machinery | |
FC250 | 250 MPa | Heavy-duty gears, machine tool parts | |
FC300 | 300 MPa | Heavy machinery, press frames | |
FC350 | 350 MPa | Highly stressed components, heavy-load gears | |
SAE J431 Specifies grey cast iron grades used in the automotive industry, particularly for components like brake drums and engine blocks. | G1800 | 18 ksi | Suitable for products requiring low strength |
G2500 | 25 ksi | Brake drums, rotors, other automotive parts | |
G3000 | 30 ksi | Automotive engine blocks, cylinder heads | |
G3500 | 35 ksi | Higher strength automotive components | |
G4000 | 40 ksi | Applications requiring higher wear resistance | |
GB/T 9439 Chinese standard for grey cast iron, setting technical requirements for castings in engineering and automotive industries in China. | HT150 | 150 MPa | General engineering, light castings |
HT200 | 200 MPa | Machine bases, frames, boxes, heavier castings | |
HT250 | 250 MPa | Gears, cylinder blocks, heavy-duty machinery | |
HT300 | 300 MPa | Heavy machinery, rollers, press frames | |
HT350 | 350 MPa | Heavy-duty gears, high-stress components |
Grey Iron vs Ductile Iron: What are the Differences?
Alongside with Grey Iron, Ductile Iron is another most commonly used casting materials. Though they share some basic characteristics as they both belong to the iron casting family, their properties and applications differ significantly due to their distinct microstructures.
First of all, let take a overview of the table comparing the properties of gray cast iron and ductile cast iron:
Property | Grey Iron | Ductile Iron |
Graphite Shape | Flaky | Spherical |
Tensile Strength | Low | High |
Compressive Strength | High | High |
Ductility | Low | High |
Wear Resistance | High | Very High |
Machinability | Very High | High |
Vibration Damping | Very High | High |
Cost | Low | Moderately High |
Main Uses | Engine blocks, manhole covers, cutting tools | Water pipes, vehicle parts, frying pans, railway wheels |
Differences Between Grey Iron and Ductile Iron
Let’s explain the differences between them in more detail to help you figure out which one is better:
Graphite Shape
Grey Iron: Contains graphite in flake form. This flake-like structure contributes to the grey color seen on the fracture surfaces, hence the name “grey iron.”
Ductile Iron: Contains graphite in spherical form. The spherical shapes of graphite within the metal provide enhanced ductility and toughness, which improves the overall strength and impact resistance of the iron.
Mechanical Properties
Tensile Strength:
Grey Iron: Lower tensile strength due to the stress concentration effects of the flake graphite.
Ductile Iron: Higher tensile strength and better elongation properties, making it more suitable for dynamic and high-stress applications.
Compression Strength:
Both grey and ductile iron have high compression strength, but ductile iron’s additional ductility makes it more versatile under load.
Ductility
Grey Iron: Generally, has lower ductility compared to ductile iron, making it more brittle and susceptible to cracking under shock or impact.
Ductile Iron: Exhibits higher ductility, which allows it to withstand greater deformation before failing, making it ideal for applications requiring a higher resistance to impact.
Wear Resistance
Grey Iron: Offers good wear resistance, which makes it suitable for applications like engine blocks and machinery where durability is important.
Ductile Iron: Exhibits even higher wear resistance due to its tough structure, suitable for heavily stressed components like automotive drivetrain parts.
Machinability
Grey Iron: Excellent machinability due to the presence of graphite flakes which act as a lubricant during the cutting process.
Ductile Iron: Also machinable, but to a slightly lesser extent compared to grey iron due to its tougher nature.
Vibration Dampening
Grey Iron: Superior vibration dampening capabilities due to the graphite flake structure, making it a preferred material for bases of heavy machinery and engine blocks.
Ductile Iron: Also good at dampening vibrations but slightly less effective compared to grey iron.
Cost
Grey Iron: Typically less expensive to produce than ductile iron, mainly due to simpler processing requirements.
Ductile Iron: Generally costs more due to additional processing to achieve the spherical graphite shapes, but the cost is offset by the material’s superior properties.
Common Applications
Grey Iron: Widely used in applications such as engine blocks, manhole covers, and machinery bases where strength is required but where the material will not be subjected to bending or torsional stresses.
Ductile Iron: Used in applications that require additional toughness and strength, such as water pipes, automotive components, and gears.