H65 brass is a versatile and widely used alloy that has become an essential material in various industries. Known for its excellent mechanical properties, corrosion resistance, and adaptability to different environments, H65 brass is particularly valued in applications ranging from decorative items to industrial components. This article provides an in-depth overview of H65 brass, its composition, equivalent standards, applications, and performance in various environments. Additionally, a comparison with H62 brass highlights the unique advantages of H65 for specific use cases.
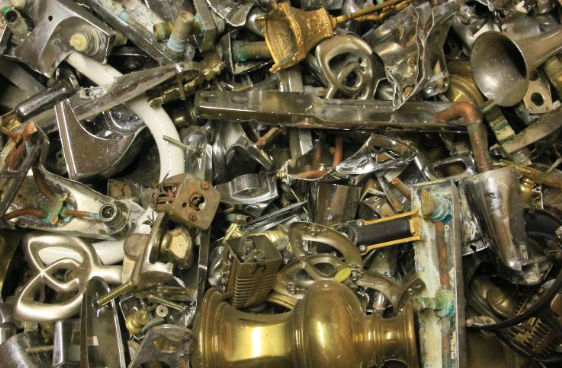
H65 Brass Chemical Composition
H65 brass is a common brass alloy composed primarily of copper and zinc. The typical chemical composition includes 64-66% copper and 33-35% zinc. This combination results in a balanced alloy with moderate strength and hardness, making it suitable for most mechanical applications. The tensile strength typically ranges from 350-450 MPa, and its hardness falls within the HB 80-100 range.
H65 Brass Equivalents
The international equivalents for H65 brass are as follows:
CDA (Copper Development Association): CDA270
UNS (Unified Numbering System): C27000
DIN (Deutsches Institut für Normung): CuZn36 (2.0335)
JIS (Japanese Industrial Standards): CuZn35
GB (Chinese Standard): H65
BS (British Standard): CZ107
These equivalents highlight the global recognition of H65 brass and its widespread use across industries.
Applications of H65 Brass
H65 brass finds application in a wide range of industries due to its favorable properties:
-Liquid Filtration and Particle Separation: Commonly used in screens and strainers.
-Aerospace and Architectural Components: Ideal for lightweight and corrosion-resistant parts.
-Decorative Items: Suitable for aesthetic designs due to its golden appearance.
-Marine Settings and Plumbing: Used in valves, pumps, and fixtures.
-Oil Strainers and Power Plants: Essential in filtering systems.
Corrosion Resistance of H65 Brass in Different Environments
1. Atmospheric Environment
Corrosion Resistance: H65 brass exhibits excellent corrosion resistance in dry atmospheric conditions. The alloy forms a dense oxide layer that prevents further corrosion.
Applications: Suitable for parts exposed to general atmospheric conditions, such as decorative fittings, lamps, and furniture components.
2. Freshwater Environment
Corrosion Resistance: Good resistance to freshwater environments, with the high copper content offering protection. However, localized corrosion can occur under certain conditions.
Applications: Used in pipes, valves, and pumps in freshwater systems, though regular maintenance is recommended.
3. Seawater Environment
Corrosion Resistance: Poor resistance due to the presence of chloride ions, which accelerate zinc corrosion and can cause stress corrosion cracking.
Applications: Not recommended for direct seawater exposure unless additional protective measures, such as coatings, are applied.
4. Chemical Media Environment
Corrosion Resistance: Performs well in weak acids, weak bases, and neutral solutions but corrodes rapidly in strong acids, strong bases, or certain organic solvents.
Applications: Suitable for parts in contact with mild chemicals but should be avoided in harsh chemical environments.
5.Soil Environment
Corrosion Resistance: Performance varies with soil chemistry. It resists corrosion well in neutral or mildly acidic soils but deteriorates in strongly acidic or alkaline soils.
Applications: Used in underground pipelines and structures with appropriate protective measures.
6. Indoor Environment
Corrosion Resistance: Excellent corrosion resistance due to stable indoor conditions with low humidity and fewer reactive chemicals.
Applications: Ideal for indoor decorative items, electronic components, and precision instruments.
Mechanical Properties and Processing Performance of H65 Brass
7. Hardness and Workability
Machining: The moderate hardness of H65 brass ensures excellent machinability, reducing tool wear and allowing efficient turning, milling, and drilling.
Forming: H65 brass is suitable for various forming processes, including extrusion, stretching, and forging, thanks to its good plasticity and toughness.
8. Wear Resistance and Fatigue Resistance
Wear Resistance: H65 brass offers moderate wear resistance, making it ideal for medium-load applications such as gears and bearings.
Fatigue Resistance: The alloy’s combination of toughness and hardness ensures good performance under repeated stress, making it suitable for springs, bushings, and other dynamic parts.
H62 vs H65 Brass, Which is Better?
H62 and H65 brass differ in their copper content and mechanical properties. H62 brass, with slightly lower copper content, is versatile and widely used in plumbing, electrical components, and hardware. In contrast, H65 brass boasts higher tensile strength, better corrosion resistance, and superior machinability, making it ideal for decorative items, musical instruments, and radiator cores. Your choice should depend on specific project requirements like strength, corrosion resistance, or aesthetic needs.
Property | H62 Brass | H65 Brass |
Copper Content (%) | 60.5-63.5 | 63-65 |
Zinc Content (%) | 36.5-39.5 | 35-37 |
Tensile Strength (MPa) | ≥295 | ≥315 |
Yield Strength (MPa) | ≥105 | ≥110 |
Elongation (%) | ≥25 | ≥30 |
Hardness (HB) | 80-100 | 90-110 |
Corrosion Resistance | Good | Excellent |
Machinability | Moderate | Good |
Applications | Plumbing, electrical components, hardware | Decorative items, musical instruments, radiator cores |