Inconel is a nickel-chromium-based superalloy that is highly resistant to corrosion and heat. In this article, we will explore what Inconel is, its various types and specifications, common applications, advantages over other materials, and interesting facts about Inconel.
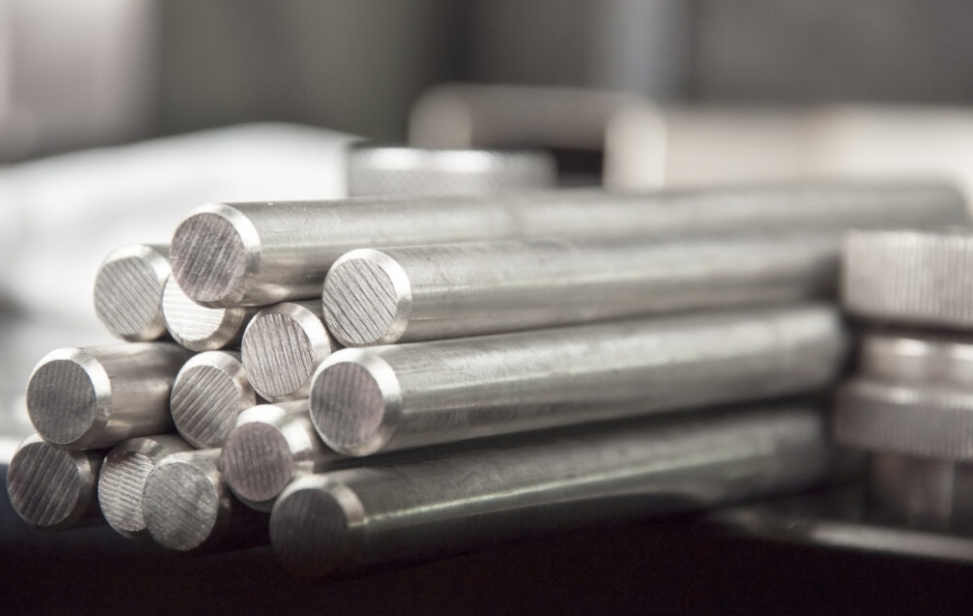
What is Inconel
Inconel is a registered trademark of Special Metals Corporation for a series of nickel and nickel-iron-based corrosion-resistant superalloys. The name “Inconel” comes from “INCo nickel”, referring to its chief components of nickel and chromium and the company INCO which developed the alloy system in the 1940s.
Inconel alloys contain a minimum of 50% nickel along with chromium for oxidation and corrosion resistance. They can withstand high temperatures of up to 2000° F (1100° C) without protection by oxidation. Thanks to their high nickel content, Inconels possess excellent strength and resistance against corrosion from saltwater, acids, alkalis, and chlorine at high temperatures.
Types and Specifications of Inconel
There are many types and grades of Inconel alloys tailored for specific temperature ranges and corrosive environments:
- 1. Inconel 600: Developed in 1946, Inconel 600 contains 72% nickel, 15.5% chromium, and various other elements. It has good corrosion resistance up to 1600°F (870°C).
- 2. Inconel 625: Introduced in 1960, this versatile alloy contains 62% nickel, 21.5% chromium, 9% molybdenum, and other elements. It can operate continuously at temperatures up to 2000°F (1095°C).
- 3. Inconel 686: Developed for use up to 1400°F (760°C), it contains 59% nickel, 16% chromium, 9% molybdenum, and other elements.
- 4. Inconel 718: Containing 52-55% nickel, 18-20% chromium, 18.5-21% iron, and niobium, this alloy has strength up to 1800°F (980°C).
- 5. Inconel X-750: Used for gas turbine applications up to 1300°F (704°C), it contains 56-81% nickel, 17-22% chromium, and 8-10% cobalt.
- 6. Inconel 939: Used as diffusion barriers for solid oxide fuel cells, it contains 57% nickel and 20% chromium. Operating temperatures can reach 1400°C.
Common Uses and Applications of Inconel
Thanks to their exceptional corrosion resistance, strength, and ability to operate continuously at high temperatures, Inconels see widespread use in industries.
- -Aerospace: Turbine engines, combustion chambers, and exhaust nozzles experience extreme heat and corrosion. Inconel alloys are ideal here.
- -Chemical Processing: Reactors, pipes, and valves in refineries handling hydrochloric acid, seawater, and other chemicals.
- -Oil & Gas: Downhole tools, subsea pipelines transporting crude at high pressures and saline conditions.
- -Power Generation: Boilers, heat exchangers, steam turbines subjected to high heat and pressures.
- -Industrial Gas: Reactors, furnace components manufacturing ammonia, and ethylene using corrosive feedstocks.
- -Automotive: Exhaust manifolds and turbocharger housings must withstand heat from burned gases.
- -Medical: Surgical/dental instruments, prosthetics requiring corrosion resistance and biocompatibility.
FAQ
1. How Is Machining With Inconel?
Machining Inconel, a family of nickel-chromium-based superalloys, is notoriously challenging due to the material’s unique properties. Inconel alloys are designed for high temperature and corrosive environments, which also make them difficult to cut and shape using traditional CNC machining processes. There are some tips for Machining.
- -Use Hard Cutting Tools: Tools made of materials such as carbide, ceramic, or cubic boron nitride (CBN) are more effective at machining Inconel due to their hardness and heat resistance.
- -Low Cutting Speeds: Operating at lower cutting speeds can help manage the heat and reduce work hardening.
- -High Feed Rates: A higher feed rate can help to cut beneath the work-hardened layer more effectively.
- -Adequate Cooling: Generous and consistent coolant flow is essential to dissipate heat and extend tool life.
- -Rigid Setup: Ensure that the workpiece and tool are rigidly mounted to reduce vibration and chatter, which can exacerbate tool wear.
- -Opt for Sharp Tools: Using tools with sharp edges helps to reduce cutting forces and heat generation.
- -Use Climb Milling: Climb milling can help in reducing work hardening by ensuring that the cutting happens under the material’s surface.
- -Regular Tool Changes: Be prepared for more frequent tool changes to maintain surface finish and dimensional accuracy.
2. How Are Welding Jobs with Inconel?
Welding Inconel alloys can be as challenging as machining them, due to their robust properties that are essential for their applications in extreme environments. There are some tips for Welding.
- -Appropriate Filler Metals: Use filler materials that are specifically designed for Inconel or that match the base material to minimize the risk of cracking and other weld defects.
- -Preheating and Interpass Temperatures: Managing to preheat and interpass temperatures can reduce stresses that contribute to cracking.
- -Control Heat Input: Use welding processes that allow for control over heat input to mitigate the risks of distortion and cracking. Pulse arc welding can be beneficial for this reason.
- -Cleanliness: Ensure the welding area is free of contaminants. Use a dedicated stainless steel brush for cleaning and avoid cross-contamination with other metals.
- -Post-Weld Heat Treatment (PWHT): Depending on the specific Inconel alloy and the service conditions of the part, post-weld heat treatment may be required to relieve residual stresses and restore corrosion resistance.
- -Tungsten Inert Gas (TIG) Welding: TIG welding is commonly used for Inconel because it offers good control over the weld pool and heat input, which is beneficial for managing the challenges of welding Inconel.
- -Inert Gas Shielding: Use high-purity argon or a mixture of argon and helium as a shielding gas to protect the weld pool from atmospheric contamination.
- -Welding Technique: Employ a stringer bead technique rather than a weaving motion to reduce heat input and minimize the HAZ.
3. How Much Does an Inconel Cost?
The cost of Inconel can vary depending on the specific grade, form (pipe, tube, fittings, etc.), and market conditions.
Price of Inconel Pipe:
- – Inconel 600 Seamless Pipe: $44,000 – USD 45,500 / Ton
- – Inconel 625 Seamless Pipe: $45,000 – USD 46,500 / Ton
- – Inconel 800 Seamless Pipe: $23,500 – USD 25,000 / Ton
- – Inconel 825 Seamless Pipe: $25,000 – USD 26,500 / Ton
Price of Inconel Tube:
- – Inconel 600 Seamless Tube: $45,000 – USD 46,500 / Ton
- – Inconel 625 Seamless Tube: $46,000 – USD 47,500 / Ton
- – Inconel 800 Seamless Tube: $24,500 – USD 26,000 / Ton
- – Inconel 825 Seamless Tube: $26,000 – USD 27,500 / Ton
Price of Inconel Fittings:
- – Inconel Pipe Fittings (Weldolet, Tee, Reducer): $1 – USD 100 / Piece (FOB Price)
4. How Hard is the Inconel?
The hardness values for Inconel alloys can vary depending on the specific alloy and the treatments it has undergone. The ranges you’ve provided are representative of general conditions of Inconel alloys, but actual hardness values can differ based on the exact composition and processing history of the material.
- -Cold-Rolled Inconel: This refers to Inconel that has been strengthened through cold working. Cold rolling is a process where the metal is worked below its recrystallization temperature, which increases its strength through dislocation mechanisms. The Brinell hardness range you’ve stated, 175–240, is indicative of a significant increase in strength due to work hardening.
- -Annealed Inconel: Annealing is a heat treatment that softens the metal, which in the case of Inconel, is typically done to improve ductility and reduce internal stresses. The process involves heating the material to a certain temperature and then allowing it to cool slowly. The specified Brinell hardness range of 145–220 reflects a softer and more ductile material compared to the cold-rolled condition.
- -Solutionized Inconel: Also known as solution annealing or solution treatment, this process involves heating the alloy to a high temperature to dissolve certain phases and then rapidly cooling it to retain a homogeneous structure. The hardness reduces as you indicated to 116–194 Brinell, making the alloy softer than the annealed state, which can be beneficial for further processing or forming operations.