The filling capacity is an important consideration in die casting, which influences the casting quality and efficiency. So follow us to learn about the factors affecting the filling capacity so as to improve it.
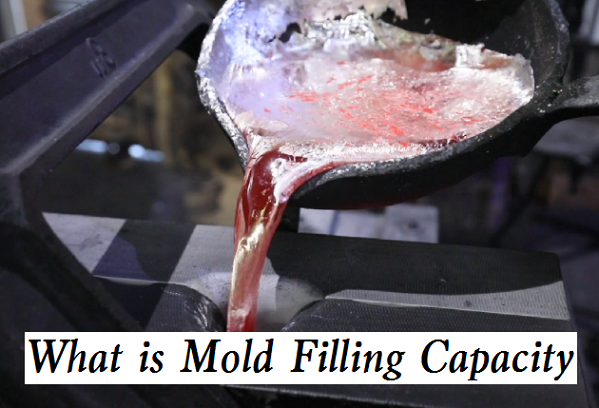
What is Mold Filling Capacity?
Mold filling capacity refers to the ability to fill the mold cavity with a liquid metal to obtain thin and complex castings with accurate size, clear contour, and complete shape. During alloy pouring, it is necessary to have a good filling ability.
What Factors Affect the Filling Capacity in Casting?
The factors that affect the filling capacity of liquid metal are mainly the fluidity of liquid metal itself, as well as the casting property, pouring conditions, casting structure, and other factors.
1. Metal fluidity
Only when the liquid metal completely fills the cavity can a good casting be obtained. The filling ability of the liquid metal is called fluidity. The fluidity of liquid metal is one of the most important casting properties of metal. The fluidity is checked and measured by pouring the fluidity sample. The most widely used flowability sample in production and scientific experiments is the spiral sample. The internal factor affecting metal fluidity is mainly the chemical composition of the alloy, and there is a certain regularity between the fluidity and composition of the alloy. Compared with cast iron, the fluidity of cast steel differs greatly due to different chemical compositions, and the fluidity of cast steel is much worse than that of cast iron. As for the cast steel itself, the fluidity is different due to different chemical compositions. For example, the melting point of ordinary carbon cast steel is higher than that of high carbon steel. At the same pouring temperature, the fluidity of low-carbon cast steel is not as good as that of high-carbon cast steel. If the steel contains alloy elements that are easy to oxidize (such as high chromium alloy steel) and oxidize into insoluble oxide inclusions at high temperatures, the fluidity of the molten steel is even worse., In a word, any factor that can increase the friction resistance between the molten metal and the mold or cause the metal temperature to drop will reduce the fluidity of the molten metal. The influence of liquid metal fluidity on casting quality is shown in the following aspects:
1) When the fluidity is good, the gas and non-metallic inclusions can be removed before pouring, or they can emerge during pouring and solidification, so as to improve the internal quality of the casting.
2) Good fluidity is the key to producing thin-walled parts. It is easy to obtain castings with accurate dimensions and clear outlines with good fluidity.
3) Good fluidity can make the casting get the liquid metal supplement in time during solidification to prevent shrinkage cavity and porosity defects.
4) Good fluidity can make the hot cracks caused by a blockage at the end of solidification easy to be bridged by liquid metal. Poor flowability can cause casting defects such as insufficient pouring and cold shut.
2. Mold properties
The properties of the mold mainly refer to the mold material, mold temperature, and the gas in the mold have an important influence on the mold filling ability. It is shown in the following aspects:
1) The mold material has good thermal conductivity (such as metal mold casting). After the metal is poured, the heat dissipation is fast, and the heat preservation time is short. The fluidity will drop sharply, and the mold filling ability will decline accordingly; On the contrary, if the casting mold has poor heat generation (such as sand casting), the fluidity will be good, making the mold filling ability high.
2) Mold temperature. Preheating the mold can reduce the temperature difference between the molten metal and the mold, slow down the cooling rate of the molten metal and prolong the liquid time, thus improving the mold-filling ability.
3) Gas in the mold. The casting material has large gas generation and low permeability. When pouring, a large amount of gas is generated in the mold cavity, which will hinder the forward flow of liquid metal if it is not eliminated in time, and even the liquid metal can not be poured in, or there is a somersault phenomenon in the pouring cup and top riser, which may even splash out and hurt people.
3. Pouring conditions
1) The higher the pouring temperature, the better the filling ability. Within the allowable pouring temperature range of castings, the filling capacity increases with the increase in pouring temperature.
2) The greater the pressure on the liquid metal in the flow direction, the better the filling capacity.
3) The more complex the gating system structure, the greater the flow resistance, and the lower the filling capacity under the same static head.
4. Casting structure
The factors to measure the structural characteristics of castings are the modulus and complexity of castings, which determine the structural characteristics of the mold cavity.
1) Modulus. When the casting volume and pouring conditions are the same, the casting with a large modulus has a relatively small contact surface area with the mold, and the heat loss is relatively slow, so the mold filling capacity is higher. The thinner the wall of the casting and the smaller the modulus, the less easy it is to be filled. Therefore, the right pouring position should be selected for thin-walled parts.
2) The complexity of the casting. The more complex the casting, the more complex the mold cavity structure, the more bends, the greater the flow resistance, and the difficulty in filling the mold.