In industries where tools must endure extreme impact, high loads, and rapid mechanical stress, not every steel can rise to the challenge. That’s where S7 tool steel comes into play — a material known for its exceptional combination of strength, shock resistance, and thermal stability. As both a workhorse and a specialist, it’s widely used in punches, dies, jackhammer bits, and other high-impact tools. Today, we’ll take a closer look at S7 tool steel, from its chemical makeup to its mechanical properties, heat treatment process, and how it compares with 4140 alloy steel.
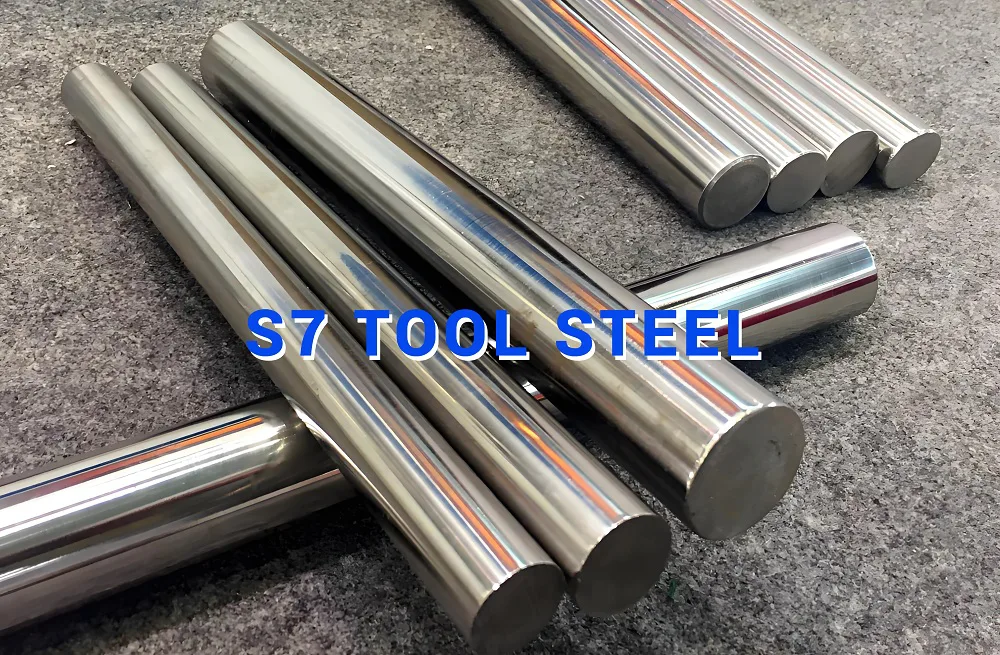
1. What is S7 Tool Steel?
S7 tool steel is a high-performance, air-hardening alloy steel used primarily for tools requiring high impact resistance and toughness. Unlike traditional water or oil-hardening steels, S7 hardens in still air, minimizing distortion and reducing the risk of cracking during heat treatment.
Its balanced profile of durability, dimensional stability, and workability has made it a preferred choice in both hot and cold working environments. In short, S7 is engineered to endure – making it one of the most reliable materials for industrial tooling.
2. S7 Steel Chemical Composition
The chemical composition of S7 tool steel is carefully formulated to deliver a blend of strength, hardness, and impact resistance:
Element | Content (%) | Contribution |
---|---|---|
Carbon (C) | 0.45–0.55 | Strength and hardenability |
Chromium (Cr) | 3.00–3.50 | Toughness, wear resistance, oxidation control |
Molybdenum (Mo) | 1.30–1.80 | High-temperature strength and toughness |
Vanadium (V) | ≤0.35 | Grain refinement and wear resistance |
Silicon (Si) | 0.20–1.00 | Toughness and oxidation resistance |
Manganese (Mn) | 0.20–0.90 | Hardenability and structural strength |
Phosphorus (P) | ≤0.030 | Impurity control |
Sulfur (S) | ≤0.030 | Improves machinability in small amounts |
3. S7 Tool Steel Properties
S7 tool steel offers a unique combination of mechanical and thermal properties that make it suitable for demanding environments. Let’s break down its capabilities in detail:
Mechanical Properties
Property | Typical Value |
---|---|
Tensile Strength | ~220 ksi (1517 MPa) |
Yield Strength | ~190 ksi (1310 MPa) |
Modulus of Elasticity | ~207 GPa |
Elongation at Break | ~10–15% |
Density | 7.76 g/cm³ (0.280 lb/in³) |
Impact Toughness | Extremely High |
Fatigue Resistance | Excellent |
Softening Resistance | Maintains hardness at elevated temps |
Dimensional Stability | High during heat treatment |
Hardness
One of the standout features of S7 is its ability to combine hardness with impact resistance. It can be heat treated to high hardness levels while still absorbing shock.
- S7 Tool Steel Hardness Before Heat Treatment (Annealed): ~20–24 HRC
- S7 Tool Steel Hardness After Quenching and Tempering: Up to 60–61 HRC
- S7 Tool Steel Hardness Tempering Range: Hardness between 45–57 HRC, depending on temperature
S7 Tool Steel Rockwell Hardness Tempering Chart
Tempering Temperature (°F) | Hardness (HRC) |
---|---|
400 | 60 |
600 | 58 |
800 | 54 |
1000 | 50 |
1150 | 45 |
Machinability
S7 tool steel is moderately machinable, especially in its annealed state. Its machinability rating is approximately 65%, compared to W1 tool steel at 100%.
- Best machined before heat treatment
- Use carbide tools for machining hardened S7
- Requires slower speeds and rigid setups for best results
Heat Treatment Process
Proper heat treatment is essential for achieving the desired mechanical performance of S7. It responds well to air hardening, which reduces distortion compared to oil-quenched steels.
Stage | Conditions | Goal |
---|---|---|
Annealing | Heat to 815–845°C (1500–1550°F), hold, then slow-furnace cool to 538°C (1000°F) | Soften the steel for machining. |
Hardening | Preheat to 650–705°C (1200–1300°F), austenitize at 925–955°C (1700–1750°F), air or oil quench | Full hardness of 60–61 HRC |
Tempering | Reheat to 205–620°C (400–1150°F), hold based on section size and desired hardness | Tempering temperature determines final hardness and toughness.Double tempering is often recommended to relieve residual stress. |
Cutting Speeds & Feeds (Annealed Condition)
To maintain tool life and ensure surface finish, machining parameters must be carefully selected:
Operation | Speed (SFM) | Feed Rate |
---|---|---|
Turning (HSS) | 60–80 | 0.010–0.015 IPR |
Turning (Carbide) | 150–250 | 0.015–0.025 IPR |
Drilling (HSS) | 20–35 | 0.004–0.008 IPR |
Milling (HSS) | 60–90 | 0.003–0.006 per tooth |
Milling (Carbide) | 200+ | 0.005–0.010 per tooth |
Thermal & Physical Properties
Property | Value |
---|---|
Thermal Expansion (20–200°C) | 12.6 μm/m·K |
Thermal Expansion (20–425°C) | 13.3 μm/m·K |
Thermal Expansion (20–500°C) | 13.7 μm/m·K |
Specific Heat Capacity | ~0.46 J/g·K |
Electrical Resistivity | ~0.75 µΩ·m |
4. S7 Tool Steel Equivalent Grades
S7 has international equivalents that share similar properties and applications:
Standard | Equivalent |
---|---|
AISI / SAE | S7 |
UNS | T41907 |
DIN | 1.2355 |
Werkstoff Nr. | X45NiCrMo4 |
JIS | SKS93 |
Chinese Equivalent | 5Cr3Mn1SiMo1V |
5. S7 Tool Steel Applications
With its excellent combination of impact strength, wear resistance, and heat stability, S7 is used in a wide variety of tools and mechanical components, including:
- Punches and Dies for stamping and forming
- Chisels and Shear Blades exposed to shock
- Jackhammer Bits and Air Hammer Tools
- Plastic Mold Inserts
- Hot Forging Dies and Cutting Tools
- Rivet Setters, Screwdrivers, and Stamps
Because it resists both deformation and cracking, S7 remains a trusted material for heavy-duty and precision tooling across many sectors.
6. S7 Tool Steel vs 4140 Steel, What are the Differences?
When selecting a steel for industrial tools or mechanical components, both S7 tool steel and 4140 alloy steel are commonly considered due to their strength and versatility. However, these two materials are designed for very different purposes. Understanding how they compare helps ensure the right material is used for the job.
Differences in Chemical Composition
Element | S7 Tool Steel | 4140 Steel |
---|---|---|
Carbon (C) | 0.45-0.55% | 0.38-0.43% |
Chromium (Cr) | 3.00-3.50% | 0.80-1.10% |
Molybdenum (Mo) | 1.40-1.80% | 0.15-0.25% |
Vanadium (V) | 0.20-0.30% | Negligible or < 0.03% |
Silicon (Si) | 0.20-1.00% | 0.15-0.35% |
Manganese (Mn) | 0.20-1.00% | 0.75-1.00% |
4140 Steel has lower alloy content, making it more economical but less specialized in properties like impact resistance.
Differences in Mechanical Properties
Property | S7 Tool Steel | 4140 Steel |
---|---|---|
Tensile Strength | 200,000 psi (approx.) | 95,000–180,000 psi (depending on heat treatment) |
Hardness (HRC) | Up to 54-60 HRC after treatment | Up to 28-32 HRC (can reach ~55 HRC with heat treatment) |
Toughness | Extremely high | Moderate |
Wear Resistance | Moderate | Moderate to good |
Machinability | Decent (annealed state) | Better machinability compared to S7 |
4140 Steel has good machinability and versatility, often used in structural and mechanical components.
Differences in Key Characteristics
Feature | S7 Tool Steel | 4140 Steel |
---|---|---|
Shock Resistance | Exceptional | Moderate |
Hardenability | Air-hardening (minimal distortion) | Oil-hardening (may warp during quenching) |
Corrosion Resistance | Limited | Limited (can be improved with coatings) |
Wear Resistance | Moderate | Moderate |
Cost | Higher | Lower |
Differences in Applications
S7 Tool Steel: Designed for tools exposed to repeated shock and heavy loads. Common applications: Punches and Dies, Chisels and Shear Blades, Jackhammer Bits, Plastic Molds and Die-Casting Dies, Air Hammer Tools
4140 Steel: A versatile, general-purpose steel used in structural and mechanical components. Common applications: Gears and Shafts, Bolts and Fasteners, Automotive and Aerospace Components, Hydraulic Parts, Forgings
Differences in Heat Treatment
Process | S7 Tool Steel | 4140 Steel |
---|---|---|
Hardening | Heat to 1725°F, air-cool | Heat to 1530-1600°F, oil-quench |
Tempering | 400-1000°F for desired hardness | 400-1100°F for desired hardness |
Annealing | 1550°F, slow cool to 1000°F | 1450-1550°F, furnace cool |
4140 Steel requires oil quenching, which increases the risk of distortion.
Differences in Pros and Cons
Advantages & Disadvantages of S7 Tool Steel:
- ✔️Superior toughness and impact resistance.
- ✔️Minimal distortion during heat treatment.
- ✔️Retains hardness after repeated impacts.
- ❌Higher cost.
- ❌Less wear resistance compared to high-carbon or high-speed steels.
Advantages & Disadvantages of 4140 Steel:
- ✔️More economical.
- ✔️Versatile for a wide range of mechanical applications.
- ✔️Good balance of strength and toughness.
- ❌Lower impact resistance compared to S7.
- ❌Requires oil quenching, which may lead to warping.
S7 Tool Steel vs 4041 Steel, Which is Better To Choose?
Choose S7 tool steel when:
- The tool or component must endure high shock loads
- Dimensional stability during heat treatment is important
- The application involves intermittent high-temperature exposure
- You require a balance of hardness and toughness
Choose 4140 alloy steel when:
- You’re building structural or mechanical parts
- High strength with good machinability is required
- Cost is a concern, and extreme toughness is not essential