Looking for a casting material that combines strength, ductility, and versatility? SG Iron, also known as Spheroidal Graphite Iron or Ductile Iron, stands out as a modern engineering marvel. With its unique graphite microstructure, exceptional mechanical properties, and wide-ranging applications, SG Iron is transforming industries such as automotive, construction, and energy. From its carefully controlled composition to its innovative casting process, this material offers robust solutions for demanding environments while bridging the gap between traditional cast iron and steel. Today, let’s talk about everything about SG Iron, including its composition, properties, microstructure, types, grades, casting process, uses, benefits, and how it compares to cast iron.
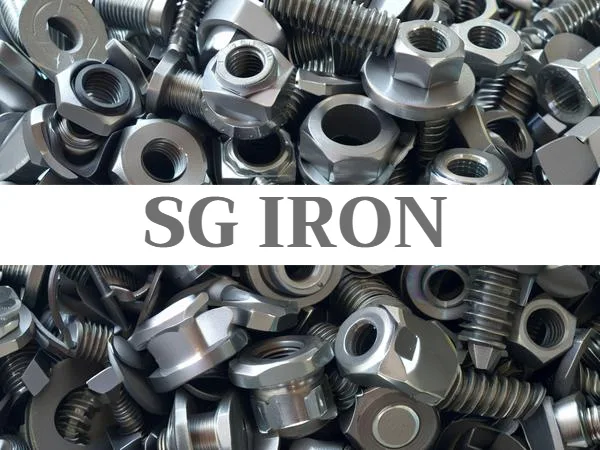
1. What is SG Iron (Spheroidal Graphite Iron)?
SG Iro, full form Spheroidal Graphite Iron, also known as Ductile Iron or Nodular Cast Iron, is a type of cast iron that has improved mechanical properties due to its unique microstructure. Unlike conventional gray cast iron, which contains graphite in flake form, SG Iron has graphite in a spheroidal (nodular) shape. This structure enhances strength, ductility, and impact resistance, making SG Iron a preferred material in engineering applications.
The development of SG Iron dates back to the mid-20th century in the USA, where the addition of magnesium (Mg) or cerium (Ce) to cast iron led to the formation of spherical graphite nodules, reducing brittleness and increasing toughness.
2. SG Iron Microstructure
The microstructure of SG Iron (Spheroidal Graphite Iron or Ductile Iron) features spherical graphite nodules embedded within a metallic matrix, which distinguishes it from gray cast iron with its flake graphite. These nodules, formed by adding magnesium or cerium during casting, minimize stress concentrations, enhancing ductility and toughness. The surrounding matrix can vary—ferritic for high ductility, pearlitic for strength and wear resistance, or a combination of both. Heat treatments can further refine the matrix to bainitic or austempered forms, providing exceptional strength and fatigue resistance. This unique microstructure gives SG Iron its superior mechanical properties.
3. SG Iron Composition
The chemical composition of SG Iron varies based on the grade and required mechanical properties. The general composition includes:
- Carbon (C): 3.2–3.6% – Present as spheroidal graphite, enhancing mechanical performance.
- Silicon (Si): 2.0–2.8% – Promotes graphitization and influences the matrix structure.
- Manganese (Mn): 0.1–0.4% – Improves strength and minimizes sulfur’s negative effects.
- Magnesium (Mg): 0.03–0.06% – The key nodularizing agent responsible for spherical graphite formation.
- Phosphorus (P): <0.05% – Controlled to prevent embrittlement.
- Sulfur (S): <0.02% – Kept low to maintain ductility and ensure proper nodularization.
- Other elements: Copper (Cu), Nickel (Ni), and Chromium (Cr) may be added to improve wear resistance, corrosion resistance, or strength.
4. SG Iron Properties
SG Iron offers a combination of high strength, ductility, and toughness, making it superior to conventional gray cast iron.
Mechanical Properties:
- Density: 7.0 g/cm³ – 7.3 g/cm³, exact value can vary slightly depending on the specific composition and microstructure of the SG Iron grade (e.g., ferritic, pearlitic, or austempered).
- Tensile Strength: 350–900 MPa (comparable to cast steel).
- Yield Strength: Varies based on grade but generally exceeds 250 MPa.
- Elongation: Ranges from 2% to 25%, significantly higher than traditional cast iron.
- Impact Resistance: Greater toughness than gray iron, reducing failure under dynamic loads.
- Fatigue Strength: Over 50% higher than gray iron, making it ideal for cyclic load applications.
Other Properties:
- Wear Resistance: Spheroidal graphite reduces stress concentration, improving wear performance.
- Vibration Damping: Retains cast iron’s inherent damping capacity, making it suitable for machine bases.
- Machinability: Excellent machinability, though harder grades require special tooling.
- Weldability: Possible but requires preheating and post-weld treatment.
5. SG Iron Types
SG Iron is classified based on matrix structure and mechanical properties:
1. Ferritic SG Iron (EN-GJS-400-18):
- Example Grades: SG 400/15, SG 400/18
- Properties: High ductility and excellent impact resistance, good machinability, and used where toughness and elongation are required.
- Applications: Pipe systems, automotive suspension components, and pressure vessels.
2. Ferritic-Pearlitic SG Iron (EN-GJS-500-7):
- Example Grades: SG 500/7
- Properties: Balanced strength and elongation, and better wear resistance than purely ferritic grades.
- Applications: Machinery, gears, hydraulic components, and general engineering applications.
3. Bearlitic SG Iron (EN-GJS-600-3):
- Example Grades: SG 600/3
- Properties: High strength and moderate ductility, and improved hardness and wear resistance.
- Applications: Crankshafts, heavy-duty gears, and mechanical components subject to high stress.
4. Bainitic SG Iron
- Example Grades: SG 700/2
- Properties: Superior strength and hardness, and lower elongation but excellent fatigue resistance.
- Applications: High-load structural components, railway parts, and construction equipment.
5. Austempered Ductile Iron (ADI)
- Example Grades: SG 900/2, SG 1200/1
- Properties: Extreme strength-to-weight ratio, and high wear resistance and impact strength.
- Applications: Aerospace, automotive, and wind energy sectors.
6. SG Iron Grades Chart (Chemical Composition & Mechanical Properties)
Grade | C (%) | Si (%) | Mn (%) | Mg (%) | P (%) | S (%) | Other Elements | Tensile Strength (MPa) | Yield Strength (MPa) | Elongation (%) |
---|---|---|---|---|---|---|---|---|---|---|
SG Iron 400/15 | 3.2–3.6 | 2.2–2.8 | 0.1–0.4 | 0.03–0.05 | <0.05 | <0.02 | Cu, Ni (optional) | 400 | 250 | 15% |
SG Iron 400/18 | 3.2–3.8 | 2.0–2.6 | 0.1–0.3 | 0.03–0.05 | <0.05 | <0.02 | Small amounts of Cr, Mo | 400 | 250 | 18% |
SG Iron 500/7 | 3.1–3.6 | 2.1–2.6 | 0.2–0.5 | 0.03–0.06 | <0.05 | <0.02 | Cu, Mo (optional) | 500 | 320 | 7% |
SG Iron 600/3 | 3.0–3.5 | 2.0–2.5 | 0.2–0.6 | 0.03–0.06 | <0.05 | <0.02 | Mo, Ni for strength | 600 | 370 | 3% |
SG Iron 700/2 | 2.9–3.4 | 1.8–2.5 | 0.3–0.7 | 0.03–0.06 | <0.05 | <0.02 | Ni, Cr for wear resistance | 700 | 420 | 2% |
This table provides an overview of both the chemical composition and mechanical properties of Spheroidal Graphite Iron Iron grades, making it easier to compare different grades for specific applications.
7. SG Iron Applications
Due to its excellent mechanical and wear properties, spheroidal graphite iron is widely used in various industries:
- Automotive Industry: Engine blocks, crankshafts, suspension parts, differential housings.
- Pipeline Systems: Water and gas distribution pipes, pressure fittings.
- Heavy Machinery: Gears, hydraulic components, pump casings.
- Energy Sector: Wind turbine components, power generation equipment.
- Construction: Bridge bearings, earthquake-resistant structures.
8. SG Iron Casting Process
The Spheroidal Graphite Iron casting process involves several key steps to ensure proper graphite nodularization and mechanical performance.
1. Melting & Alloying
Raw materials (pig iron, scrap steel, and alloys) are melted in an electric or cupola furnace.
2. Nodularization (Magnesium Treatment)
Magnesium (Mg) or cerium (Ce) is added to molten iron to promote spheroidal graphite formation.
3. Inoculation (Graphite Refinement)
Silicon-based inoculants (e.g., FeSi) are added to control graphite size and prevent carbide formation.
4. Pouring & Solidification
Molten iron is poured into molds at controlled temperatures (typically 1350–1450°C) to maintain nodularity.
5. Heat Treatment (Optional)
- Annealing: Used for ferritic grades to enhance ductility.
- Quenching & Tempering: Applied for pearlitic and bainitic grades to improve strength.
Key Process Controls: Sulfur and phosphorus content must be strictly controlled, rapid pouring after nodularization prevents Mg loss, cooling rate affects matrix structure (ferritic vs. pearlitic).
9. SG Iron vs Cast Iron: What is the Difference?
Cast iron and SG iron is two common metal materials with important application value in the fields of industry and construction. In actual production, cast iron and spheroidal graphite iron are often used to manufacture parts, mechanical equipment, and structural parts to meet the needs of various projects. Here we use a table to show the main differences between cast iron and SG iron
Feature | SG Iron (Ductile Iron) | Cast Iron |
---|---|---|
Graphite Shape | Spheroidal (Nodular) Graphite | Flake Graphite |
Tensile Strength | 350–900 MPa (Comparable to cast steel) | 150–400 MPa (Lower than SG Iron) |
Elongation | 2–25% (High ductility) | <1% (Very brittle) |
Impact Resistance | High (Withstands dynamic loads) | Low (Brittle under impact) |
Fatigue Strength | 50% higher than Gray Cast Iron | Moderate (Prone to fatigue failure) |
Wear Resistance | Good (Spheroidal graphite reduces stress concentration) | Moderate |
Heat Resistance | Better than Gray Iron | Good for high-temperature applications |
Vibration Damping | Excellent | Very good |
Machinability | Good, but harder grades require special tooling | Excellent |
Weldability | Possible, but requires preheating and post-weld heat treatment | Difficult (Prone to cracking) |
Applications | Structural components, gears, pipes, automotive parts | Engine blocks, machine bases, cookware |
Cost | Higher (due to nodularization treatment) | Lower (easier and cheaper to manufacture) |
Which One Should You Choose For Your Casting Project?
- Choose SG Iron if you need: High strength, ductility, impact resistance, and fatigue strength (e.g., automotive parts, structural components, heavy machinery).
- Choose Cast Iron if you need: High vibration damping and cost-effectiveness (e.g., engine blocks, cookware, machine bases).
10. More FAQs About Spheroidal Graphite Iron
To help you get know SG iron better, here we present some of the most frequently asked questions (FAQs) about SG Iron (Ductile Iron):
- Why Was SG Iron Developed?
Originally invented in the 1940s in the USA, SG Iron was a breakthrough material for industrial applications. By adding magnesium (Mg) or cerium (Ce) to molten iron, metallurgists transformed graphite flakes into round nodules, significantly improving ductility and strength, making it a cost-effective alternative to steel in engineering applications.
SG Iron vs. Other Materials (Steel & Gray Iron)
Material | Graphite Structure | Tensile Strength (MPa) | Elongation (%) | Impact Resistance | Cost |
---|---|---|---|---|---|
SG Iron (Ductile Iron) | Spheroidal | 350–900 MPa | 2–25% | High | Medium |
Gray Cast Iron | Flake | 150–400 MPa | <1% | Low (Brittle) | Low |
Steel (Carbon/Alloy) | No Graphite | 450–1200 MPa | 10–40% | Very High | High |
- Why is SG Iron called Ductile Iron?
SG Iron is called Ductile Iron because it has high ductility and toughness, unlike gray cast iron, which is brittle due to its flake-shaped graphite structure. The spheroidal (nodular) graphite in SG Iron enhances its elongation and impact resistance, making it more flexible and less prone to cracking under stress.
- What are the main advantages of SG Iron over Gray Cast Iron?
SG Iron has several advantages over Gray Cast Iron, including:
- Higher tensile strength (350–900 MPa vs. 150–400 MPa).
- Better ductility and elongation (2–25% vs. <1%).
- Increased impact resistance and fatigue strength.
- Greater weldability and machinability for complex applications.
- Improved pressure tightness, making it ideal for pipes and pressure vessels.
- Can SG Iron be welded?
Yes, SG Iron can be welded, but it requires special precautions:
- Preheating (150–300°C) is recommended to reduce thermal stress.
- Post-weld heat treatment is necessary to restore mechanical properties.
- Nickel-based electrodes are often used for improved weldability.
- Is SG Iron corrosion-resistant?
SG Iron has moderate corrosion resistance, but it can be improved by adding Nickel (Ni) and Chromium (Cr) to enhance corrosion resistance, applying protective coatings such as galvanization or epoxy layers, or using austempered ductile iron (ADI) for extreme environments.
- What is Austempered Ductile Iron (ADI), and how does it compare to SG Iron?
Austempered Ductile Iron (ADI) is a heat-treated version of SG Iron that offers:
- Higher strength (up to 1,200 MPa).
- Superior wear resistance for gears and high-load applications.
- Better toughness and fatigue resistance than standard SG Iron.
- Lower weight-to-strength ratio, making it competitive with steel.
- Why is SG Iron preferred for automotive components?
SG Iron is widely used in the automotive industry because it reduces weight while maintaining strength, improves fuel efficiency by replacing heavier steel parts. It also has excellent fatigue resistance, ideal for high-stress components like crankshafts and suspension arms, and offers better damping properties, reducing vibrations and noise.
- How does SG Iron perform under extreme temperatures?
SG Iron performs well under moderate temperature conditions (-40°C to 300°C). However, at very high temperatures (>500°C), SG Iron loses strength due to oxidation; at sub-zero temperatures, ductility decreases, but impact resistance remains better than gray iron. And heat-treated SG Iron (e.g., ADI) improves high-temperature strength and wear resistance.
- Is SG Iron recyclable?
Yes, SG Iron is fully recyclable, making it an environmentally friendly material. It is commonly used in circular manufacturing to reduce waste and energy consumption.
- What is the lifespan of SG Iron components?
SG Iron components have a long lifespan, often exceeding 20–50 years, depending on: environmental conditions (corrosion exposure, temperature), load-bearing requirements and maintenance, and proper alloying and heat treatment.
- Why is SG Iron used in wind turbines?
SG Iron is commonly used in wind turbine components, such as:
- Hubs and bearing housings, due to its high fatigue strength.
- Gearboxes and transmission components, where wear resistance is crucial.
- Structural supports, because of its good strength-to-weight ratio.
- How does SG Iron compare to Aluminum in terms of weight and strength?
Feature | SG Iron | Aluminum |
---|---|---|
Density | ~7.1 g/cm³ | ~2.7 g/cm³ |
Tensile Strength | 350–900 MPa | 100–400 MPa |
Corrosion Resistance | Moderate | High |
Machinability | Good | Excellent |
Weight | Heavier | Lightweight |
SG Iron is stronger and more wear-resistant than aluminum, but alum