Tack Welding is a common welding process. Tack welding refers to a welding process that uses metal wires or small ingots to locally heat and melt metal parts at specific points or positions so that the solder melts and combines between the points. It is a type of real welding that forms a rope welding process by allowing the solder to melt at the solder joint and mix and combine with the base metal. Through the above overview, we have a preliminary understanding of tack welding. Next, we will introduce other important information about Tack Welding.
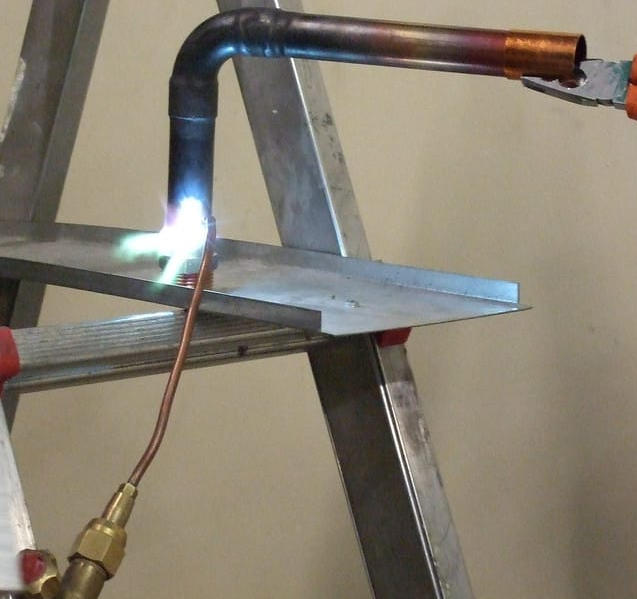
What Is Tack Welding and Its Purpose?
Tack welding is a local welding method. The purpose of tack welding is to connect two or more components through local thermal effects. It works by using wires or small spindles to locally heat and melt them at the specific locations where connections are needed.
The main characteristics and purposes of tack welding are:
- 1. Connect parts of the area. Compared with comprehensive welding, tack welding only connects the specific locations required and will not affect other surrounding components.
- 2. Small processing range. Tack welding only operates on the points that need to be connected, and the processing range is very small.
- 3. Little impact on components. Because it is a locally heated connection, it has little impact on the shape of the overall component.
- 4. Suitable for different materials. Tack welding is suitable for the connection of metal materials and can also be applied to certain non-metallic materials.
- 5. The connection is firm. Tack welding creates a strong rope weld connection by causing the solder to melt at the connection point and mix and combine with the substrate.
- 6. Easy to process. Compared with other welding, tack welding is less difficult to operate and is especially suitable for connections that need to be made in small or difficult-to-reach areas.
What Are the Types of Tack Welding Processes?
Tack welding can be classified according to different heating methods:
Type | Features |
Manual tack welding | Use a manually operated tack welding gun to heat and weld the joints to be welded. |
Automatic tack welding | Realize positioning, heating and welding of welding tacks through robots or automatic control systems. |
Resistance tack welding | Use resistance as an energy source, and uses the heat generated by the resistance to heat and weld the joints to be welded. |
Parametric tack welding | Use pulse current to heat the tack welding position at high temperature for a short time through a tack welding gun to complete the welding. |
Spark tack welding | Use a high-voltage power source to generate an arc and melt the solder joint at high temperature for a short period of time to complete the welding. |
Laser tack welding | Use a laser beam to precisely position and heat the solder joints to complete the welding. |
Soldering iron tack welding | Use a soldering iron to press the welding rod against the area to be welded to heat and melt to complete the connection. |
How Does Tack Welding Work?
The working principle and practical process of tack welding are as follows:
1. Preparatory work
-Clean the parts to be welded and remove surface dust and grease to ensure good thermal conductivity
– Load the welding rod or wire into the tack welding gun
-Adjust tack welding gun output power
2. Positioning
-Position the points to be connected according to the design drawing, and accurately align the points to be welded. The length of the weld is between ½ inch and 3/4 inch, but the length is less than 1 inch.
-Some automatic tack welding will use positioning systems to assist positioning
3. Heating
– Operate the tack welding gun to aim the welding rod or wire needle at the tack to be soldered, and output power to heat the solder and the tack to be soldered.
-Manual tack welding is operator controlled with heating time and position
-Automatic tack welding is provided by a control system with consistent heating parameters
4. Welding
After the temperature of the solder joints and solder material rises, they melt and mix together to form a whole.
5. Ending
-After the heating output is completed, wait for the solder joint to cool and solidify naturally to become a permanent connection.
-Check the connection quality and make repairs if necessary in subsequent processes
What Are the Pros, Cons, Application and Importance of Tack Welding?
Pros:
- -Small processing range, little impact on other parts
- -Easy to process, suitable for welding hard-to-reach or limited parts
- -Fast processing and high output
- -Low cost, low power consumption
Cons:
- -Requires high-precision positioning and heating control systems
- -Easy to produce thermal stress and deformation
- -Suitable for structures with small welding area
Application and Importance:
1. Widely used in automatic production lines, such as automatic assembly lines
The main applications of tack welding technology in automatic production lines include:
- -Robotic tack welding
- -Contactless tack welding
- -Intelligent tack welding system
- c inspection and other intelligent equipment to perform fixed-point real-time monitoring and parameter adjustment.
- -Continuous tack welding
- -PCB automatic tack welding
- -Battery assembly line
- -Mobile phone body assembly line
2. Used in model assembly in the vehicle industry
The main applications of tack welding technology in the vehicle industry include:
- -Tack welding of automobile body structure
- -Tack welding of automotive engine components
- -Tack welding of automobile transmission system
- -Tack welding of automobile exhaust system
- -Automotive Inner Trim tack welding
- -Tack welding of automotive electronic systems
- -Tack welding of electric vehicle battery pack
- -Tack welding of new energy vehicle system components
3. Repair or solder individual components in electronic products
The main applications of tack welding technology in electronic products include:
- -Semiconductor chip packaging.
When interconnecting different components such as chips, resistors, etc. inside the IC module, micro-spot welding technology is used for positioning connections.
- -Integrated circuit module connections.
- -Printed circuit board repair.
- -Battery assembly.
- -Automatic assembly line.
- -Power conversion module.
- -Mobile phone case assembly.
- -Connect pins.
When making a permanent connection between pad and pin, precision spot welding technology is usually used between components.
Applicable Materials:
Materials | Application Examples |
Steel | vehicle frame tack welding |
Aluminum | aircraft frame tack welding |
Copper | wire joint tack welding |
Ceramic | Semiconductor Package Tack Welding |
How to Adjust the Output Power and Pulse Time of The Tack Welding?
- Adjust output power:
- -Most tack welding guns have a power setting knob. Turn counterclockwise for smaller power and clockwise for larger power.
- – Depending on the material and dot size, first choose a medium power to start with, such as 200-300 watts.
- -If the solder joints are scorched, reduce the power by 20-50 watts and continue trying. On the contrary, if the solder liquid is insufficient, the power can be increased appropriately.
2. Adjust pulse time:
- -The pulse tack welding gun has a pulse on time setting.
- -Generally speaking, 0.05-0.1 seconds is preferred as the trial period.
- -If the solder joint is dark in color or there is too much solder liquid, it can be shortened by a few milliseconds.
- -On the contrary, if the welding effect is not obvious, you can try increasing it by a few milliseconds.
- -For some materials, you can also try multiple short pulse joining effects.