Tensile stress refers to the internal stress induced in a material when it is pulled or stretched. It is the opposite of compressive stress.
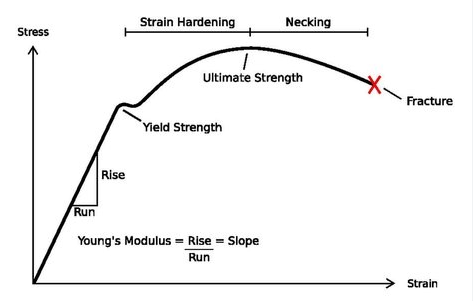
What Can Be Calculated When Tensile Stress Acts on a Material
When a tensile stress is applied, you can calculate the resulting elongation, strains, strength limits, stiffness, and factor of safety for the material based on its mechanical properties. This helps determine if the material will yield, deform, or fracture under the given loading conditions.
- -Elongation/Extension
The increase in length of the material due to the applied tensile force. This depends on the elastic modulus of the material.
- -Strain
The ratio of elongation to the original length. This is a dimensionless quantity.
- -Poisson’s Ratio
The ratio of transverse contraction strain to longitudinal extension strain in the direction of stretching force.
- -Yield Strength
The stress at which material starts deforming plastically.
- -Ultimate Tensile Strength
The maximum stress the material can withstand before fracture.
- -Modulus of Elasticity
Ratio of the stress to strain in the elastic deformation region. Indicates stiffness of the material.
- -Fracture Point
The stress level at which fracture occurs.
- -Safety Factor
Ratio of fracture stress to working stress. Indicates how much stronger the material is than the expected load.
How To Calculate Tensile Stress
Measure the applied force, find the perpendicular cross-sectional area, and divide the force by the area to obtain the tensile stress value. Check this value against material limits to ensure it does not fail.
- Step1: Identify the forces applied on the material that cause the tensile stress. This would usually be a force that pulls or stretches the material from both ends. Measure the magnitude of this applied force (F).
- Step 2: Determine the cross-sectional area (A) perpendicular to the applied force. This can be found by measuring width and thickness and multiplying them. For circular cross-sections, use the formula A = πr2.
- Step 3: Use the formula for tensile stress:
σ = F /A
σ – Tensile stress (Pa or N/m2)
F – Applied force (N)
A – Cross-sectional area (m2)
- Step 4: Substitute the values of force and area into the formula to calculate the tensile stress.
- Step 5: The unit for tensile stress is Pascals (Pa) or Newtons per square meter (N/m2). Convert units if necessary.
- Step 6: Compare the calculated tensile stress to the ultimate tensile strength of the material. The tensile stress should be lower for safe design.
What Are the Examplesof Tensile Stress?
- – Tension in a rope
When you hang an object from a rope, the suspended weight puts the rope under tensile stress. The rope elongates slightly under the applied tensile force.
- – Pulling on a rubber band
Stretching a rubber band causes tensile stress. The molecular chains in the rubber experience forces trying to separate them lengthwise.
- – Tightening bolts
Tightening nuts and bolts induces axial tensile stress in the bolt shank. This clamping force holds the parts together.
- – Loading a fishing line
Reeling in a big fish applies large tensile forces on the fishing line. This can cause the line to snap if the tensile strength is exceeded.
- – Tension in cables
Suspension cables in bridges carry the deck’s weight through axial tension forces. The cables are under constant tensile stress.
- – Loading machine parts
Gears, pulley belts, and other machine parts undergo tension when transmitting torque or power. The tensile stress must be below the yield strength.
- – Stretched springs
The coil of a stretched spring experiences tensile stress proportional to the displacement from its relaxed length.
- – Wire drawing
Pulling metal wire through a die reduces its diameter and subjects it to tensile stresses. This strengthens the wire.
- – Tension in fabrics
Fabrics experience tensile stresses when stretched or pulled. Clothing needs to withstand such stresses during wear.
How Does Tensile Stress Relate to Die Casting
Controlling tensile stress through die design and process parameters is important in die casting to avoid hot tearing defects and achieve high-quality castings. Understanding how tensile stress develops guides the design.
- – During the die-casting process, the molten metal is injected into the mold under high pressure. This causes tensile stresses to develop in the solidifying casting.
- – If the tensile stresses exceed the material’s tensile strength, it can lead to hot tearing – cracks that form in the casting as it solidifies. This defects the casting.
- – The location of holes, thickness of walls, and geometry of the die casting affect how tensile stress develops. Sharp corners and thin sections tend to have higher tensile stresses.
- – Alloys used for die casting, like aluminum and zinc, have a relatively low tensile strength in the molten state. So minimizing tensile stresses is critical.
- -The cooling rate of the die also affects tensile stress. Faster cooling leads to higher thermal gradients and tensile stress. Slower cooling reduces this.
- – Tensile properties can be improved by heat treatment like solution treatment and aging after die casting. This relieves some residual stresses.
- -The design of the die casting has to balance the flowability of metal with minimizing tensile stress. Computer simulation is used to optimize this.