There are many types of mold casting, including gravity casting molds and high-pressure die casting molds (die casting). So what is the difference between these two casting processes?
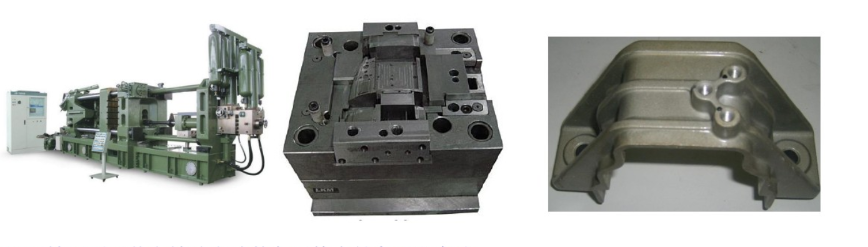
Gravity Casting
Gravity casting refers to a process in which molten metal enters the mold cavity under the action of gravity and is poured into the mold. It is also called gravity casting. In a broad sense, gravity casting refers to sand casting, metal mold casting, investment casting, lost foam casting, etc. In a narrow sense, gravity casting also refers to metallic pouring.
Characteristics of Gravity Casting
- 1. There are few pores inside the casting and it can be heat treated. The strength of the treated product can be greatly improved, even exceeding that of die-cast products.
- 2. The product has low density. Relying on liquid self-gravity molding, the density of the product is lower than that of die casting, and its strength is also slightly worse, but its elongation is higher.
- 3. The surface finish of the product is not high. After cooling and shrinkage, the surface of cast products is prone to pits similar to shot blasting.
- 4. Filling is slow and production efficiency is low. Its production efficiency is only about 1/4 of that of high-pressure casting, resulting in high product costs.
- 5. The mold life is longer than that of die casting, and the mold cost is low.
- 6. The process is relatively simple.
- 7. Not suitable for producing thin-walled parts.
High-pressure Casting
High-pressure casting is a casting method that introduces molten alloy liquid into a pressure chamber, fills the cavity of the steel mold at high speed, and solidifies the alloy liquid under pressure. The main features that distinguish high-pressure die casting from other casting methods are high pressure and high speed.
The molten metal fills the mold cavity, crystallizes, and solidifies under higher pressure. Common pressures are 15-100MPa. The molten metal fills the mold cavity at a high speed, usually 10-50 meters per second, and some can exceed 80 meters per second. Therefore, the filling time of the molten metal is very short, and the mold cavity can be filled in about 0.01-0.2 seconds.
Characteristics of High-pressure Casting
- 1. Fast filling and extremely high production efficiency.
- 2. Molding under high pressure, the product has high density, high product strength and surface strength, but the product has low elongation.
- 3. The surface finish of the product is good, generally reaching Ra6.3, or even Ra1.6.
- 4. It can produce parts with thin wall thickness, and the thinnest wall thickness of aluminum die-casting can reach 0.5mm.
- 5. The filling is fast, a lot of gas is involved inside, and the porosity of the product is poor.
- 6. Not heat treatable. During heat treatment, the internal gas will expand, causing defects such as bulges or cracks in the product.
- 7. The processing allowance is small (try to be less than 0.25mm). Excessive processing amount will destroy the surface dense layer and expose the internal pores, resulting in low product strength.
- 8. The mold cost is high and the mold life is short.
Advantages and Disadvantages of Gravity Casting and High-Pressure Casting
In terms of strength, the strength differences are also large due to the different raw materials of the aluminum alloys involved. Since die-cast products are formed under high pressure, the products have high density and high strength. For example, the strength of A380 die-cast products can reach 360MPa, but its elongation can only reach about 3.7%. Gravity casting products generally have lower strength than die casting. The better material ZL101A can only reach 310MPa after heat treatment, but its elongation is higher, reaching 5-6%. There are also materials whose strength can reach above 380MPa, such as ZL201A and ZL204A.
Craftsmanship | Mold Cost | Mold Life | Porosity | Heat treatment | Machining Allowance | Smooth Surface | Suitable Product | Productivity | |
High Pressure Casting | Complex | High | Short | Poor | No | Small | High | Thin Wall Parts | High |
Low Pressure Casting | Simple | Low | Long | Good | Yes | Big | High | Middle | Middle |
Gravity Casting | Simple | Low | Long | Good | Yes | Big | Low | Thick Wall Parts | Low |
It can be seen from the above that when we choose which process to use for product production, as long as we choose based on the thick wall of the product, high-pressure casting should be the first choice as long as the production process and product performance can meet the requirements because the production efficiency of high-pressure casting is extremely high. . When the thickness of the product is greater than 8mm, the strength of the high-pressure cast product may not meet the expected requirements due to too many internal pores. Gravity casting or low-pressure casting can be considered.
Applications of Gravity Casting and High Pressure Casting in the Automotive Industry
Gravity casting is used for large, complex component housings while high-pressure casting enables more intricate, smaller parts with thinner walls and complex internal features.
Gravity Casting:
- – Engine blocks and heads: Gravity casting is commonly used to produce the large, complex shapes of engine blocks and heads. It allows for intricate coolant passages.
- – Transmission cases: Gravity casting is well-suited for the large transmission casings found in automatic and manual transmissions.
- – Differential housings: Differential cases for rear- and front-wheel drive systems are often gravity cast due to their size and complexity.
High Pressure Casting:
- – Cylinder heads: The increased pressure of HPDC casting allows for thinner walls and more complex coolant passages in cylinder heads compared to gravity casting.
- – Transmission components: Smaller transmission parts like housings and gear sets are increasingly produced via HPDC for their dimensional accuracy.
- – Wheels: Automotive wheels are commonly HPDC cast for their intricate design and thinner-walled features impossible with gravity casting. – Other suspension and steering components: Items like knuckles, and control arms can leverage HPDC for strength and precise dimensions.