White cast iron has been a pivotal material in human history, playing a foundational role in the manufacture of farming tools and weapons. Over time, its applications have grown substantially, finding its place in modern engineering and industrial uses. Here we discusses the composition, properties, and applications of white cast iron, along with its comparison to gray cast iron to help understand its relevance in various industries.
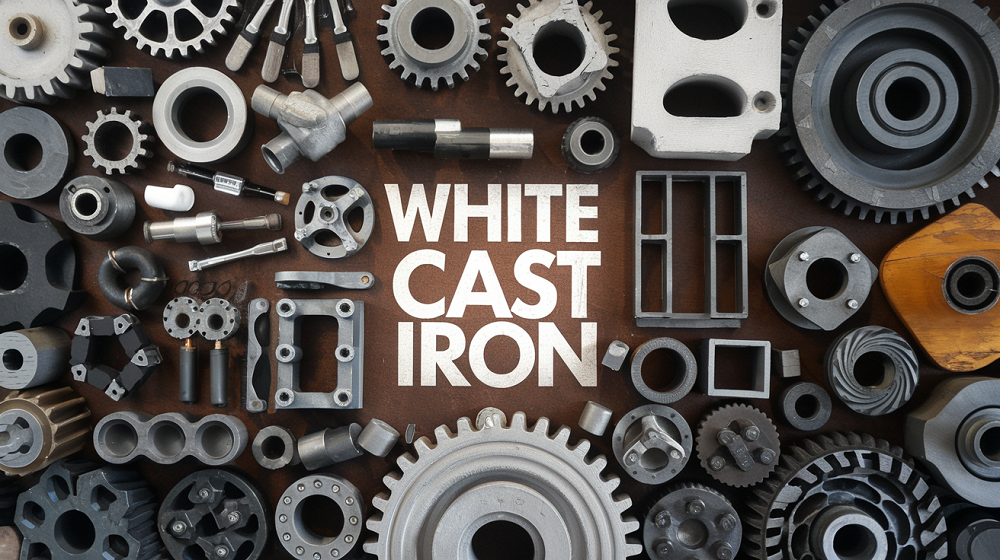
What is White Cast Iron?
White cast iron is a type of cast iron that primarily consists of iron, carbon, silicon, manganese, and phosphorus. Its distinct white appearance is attributed to its microstructure, which largely contains cementite rather than graphite. This characteristic provides white cast iron with high hardness and excellent wear resistance, making it ideal for applications requiring durability under abrasive conditions.
White cast iron is typically categorized into ordinary white cast iron and alloyed white cast iron. While ordinary white cast iron is cost-effective and suitable for low-intensity applications, alloyed white cast iron, enhanced with specific elements, is designed for more demanding environments.
White Cast Iron Composition
Below is the general white cast iron composition percentage:
- Carbon: Between 2.0% and 4.0%, primarily in the form of cementite.
- Silicon: A moderating element present in small amounts.
- Manganese, Phosphorus, and Sulfur: Present in varying proportions depending on the intended application.
- Alloying Elements (in alloyed white cast iron): Chromium, molybdenum, vanadium, titanium, tungsten, and manganese. These elements form carbides that increase hardness and improve wear resistance.
The addition of these elements can improve the mechanical properties of white cast iron, such as hardness, toughness, and corrosion resistance. So the composition of white cast iron directly affects its properties, making it adaptable for specific industrial requirements.
White Cast Iron Microstructure
The microstructure of white cast iron is primarily composed of ferrite and cementite. Cementite (Fe₃C) is responsible for its silvery-white fracture surface, high hardness, and brittleness. Unlike gray cast iron, white cast iron lacks graphite. This absence of graphite contributes to its rigidity and wear resistance, but also makes it less capable of withstanding impact loads.
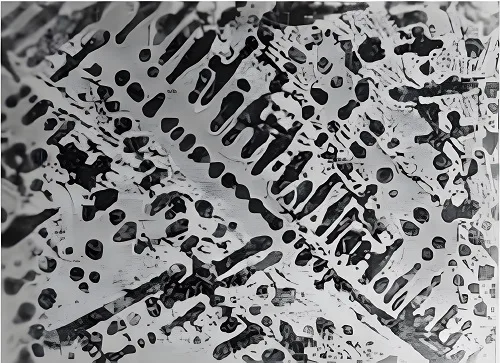
In alloyed white cast iron, carbide-forming elements like chromium and vanadium modify the microstructure. These elements combine with carbon to form metallic compounds, enhancing the material’s strength and resistance to abrasive conditions.
White Cast Iron Properties
White cast iron is distinguished by a combination of physical and mechanical properties that make it suitable for applications requiring wear resistance and durability. The properties of white iron are presented clearly in the below table:
Property | Value (Range/Specific Example) | Notes |
---|---|---|
Density | 7.0–7.2 g/cm³ | Varies with alloy content. |
Melting Point | 1420°C–1470°C | Higher for alloyed variants. |
Thermal Conductivity | 30–50 W/m·K | Lower than gray cast iron. |
Specific Heat Capacity | ~460 J/kg·K | Standard for iron-based materials. |
Electrical Resistivity | 0.8–1.0 µΩ·m | Higher due to carbon and cementite. |
Hardness | ≥HB500 (ordinary); ≥HB600 (alloyed) | High wear resistance but brittle. |
Tensile Strength | 150–300 MPa (ordinary); ≥218 MPa (alloyed) | Lower than gray or ductile iron. |
Compressive Strength | 600–1200 MPa | Excellent for compressive loads. |
Yield Strength | ≥834 MPa (alloyed) | Higher in alloyed variants like KmTBCr20Mo. |
Impact Toughness | ≥23 J (alloyed) | Limited; improved by alloying elements. |
Elongation | <1% (ordinary); ≥21% (alloyed) | Alloying improves ductility. |
Below we explain mechanical properties and physical properties in more detail:
White Cast Iron Physical Properties
Learning the physical properties of white cast iron can help you understand its behavior under various environmental conditions:
- Density: White cast iron typically has a density of about 7.0 g/cm³, although alloyed variants such as KmTBNi4Cr2-GT can reach 7.2 g/cm³.
- Melting Point: The melting point ranges from 1420°C to 1470°C, depending on the composition and the presence of alloying elements.
- Thermal Conductivity: White cast iron has a relatively low thermal conductivity compared to gray cast iron, with values generally around 30–50 W/m·K at room temperature. This lower conductivity makes it less efficient in heat dissipation.
- Thermal Expansion Coefficient: The thermal expansion coefficient is 11.0×10⁻⁶/K between 20°C and 200°C, indicating moderate dimensional changes under thermal stress.
- Specific Heat Capacity: The specific heat capacity of white cast iron is approximately 460 J/kg·K, which is typical for iron-based materials.
- Electrical Resistivity: Due to its high carbon content and cementite structure, white cast iron exhibits relatively high electrical resistivity, around 0.8–1.0 µΩ·m.
White Cast Iron Mechanical Properties
The mechanical properties of white cast iron define its application in high-stress and abrasive environments. These include hardness, tensile strength, compressive strength, fatigue resistance, and impact toughness:
- Hardness: Ordinary white cast iron has a hardness over HB500, while alloyed variants like KmTBNi4Cr2-GT can reach HB ≥600 or HRC ≥56 in the hardened state. This exceptional hardness enhances wear resistance but limits machinability.
- Tensile Strength: The tensile strength of white cast iron ranges between 150–300 MPa for ordinary types. For alloyed white cast iron such as KmTBCr20Mo, tensile strength can exceed 218 MPa.
- Compressive Strength: The compressive strength of white cast iron is significantly higher than its tensile strength, with values ranging from 600 to 1200 MPa, depending on the alloy content and heat treatment. This makes it ideal for applications involving compressive loads.
- Yield Strength: Alloyed white cast iron like KmTBCr20Mo exhibits a yield strength of ≥834 MPa, showcasing its ability to withstand substantial stress before permanent deformation.
- Fatigue Resistance: White cast iron has low fatigue resistance due to its brittle nature, making it unsuitable for cyclic loading applications. However, alloying elements such as chromium and molybdenum can slightly improve this property.
- Impact Toughness: Standard white cast iron has low impact toughness due to the presence of cementite, which promotes brittleness. For instance, KmTBCr20Mo demonstrates an impact absorption energy of ≥23 J, but this remains lower than that of ductile or gray cast iron.
- Elongation: Elongation in white cast iron is minimal, typically below 1% for ordinary types. In alloyed versions like KmTBCr20Mo, elongation can reach ≥21%, thanks to improved ductility from alloying and heat treatment.
- Cross-Sectional Shrinkage: Shrinkage in alloyed white cast iron, such as KmTBCr20Mo, is measured at ≥42%, which reflects its ability to maintain structural integrity during deformation.
- Wear Resistance: White cast iron is highly wear-resistant due to the presence of hard carbides like cementite and secondary phases introduced by alloying elements such as chromium or vanadium.
- Creep Resistance: In high-temperature applications, alloyed white cast iron demonstrates good creep resistance due to stabilizing elements like molybdenum, which improve its performance under sustained high loads.
White Cast Iron Advantages & Disadvantages
Advantages:
- Exceptional wear resistance.
- High hardness, making it ideal for tools and machinery components.
- Long service life in demanding conditions.
Disadvantages:
- High brittleness limits its applicability in situations requiring impact resistance.
- Greater shrinkage during solidification, leading to a higher likelihood of cracks.
- Higher cost compared to gray cast iron or ductile iron.
White Cast Iron Applications
White cast iron is widely utilized across various industries, including:
- Mechanical Parts: Manufacturing of machine tool components, gears, and pump housings.
- Machine Tools: Cutting tools and dies.
- Wear-Resistant Components: Grinding blocks, sleeves, and high-speed bearings.
- Construction: Used in metal doors, windows, and other structural components.
- Piping Systems: Valves and pipes in chemical and petroleum industries.
- High-Temperature Equipment: Furnaces and heat-resistant parts in industrial applications.
- Agricultural Equipment: Plowshares and other wear-prone components.
White Cast Iron vs. Gray Cast Iron: What Are the Differences?
White and gray cast irons differ significantly in their composition, properties, and applications:
White Cast Iron | Gray Cast Iron | |
---|---|---|
Composition | High carbon (2.0%-4.0%), low silicon, contains elements like Mn, P, S, Cr, Mo, Cu, Al | High carbon (2.8%-4.0%), contains Si, Mn, P, S |
Carbon Form | Carbon mainly exists as cementite (Fe3C) | Carbon mainly exists as flake graphite |
Structure | Contains more free cementite and coarse grains | Contains fine flake graphite, discontinuous and straight or curved |
Fracture Appearance | Silvery white | Dark gray |
Hardness | High hardness (30~50% higher than gray cast iron) | Lower hardness |
Brittleness | High brittleness, difficult to cut | Lower brittleness, better cutting processability |
Toughness | Low impact toughness | Good toughness, not prone to fracture |
Wear Resistance | High wear resistance | Good wear resistance |
Corrosion Resistance | Good corrosion resistance | Not as good as white cast iron |
Melting Point | Higher melting point | Lower melting point |
Machinability | Difficult to machine due to high hardness and brittleness | Better machinability due to graphite acting as chip breakers |
Casting Fluidity | Lower casting fluidity | Good casting fluidity |
Shock Absorption | Lower shock absorption | Better shock absorption due to graphite |
Tensile Strength | Higher tensile strength | Lower tensile strength due to graphite |
Application | Used for high-strength machine tools, wear-resistant parts, and as a raw material for steelmaking | Widely used in mechanical parts, automotive parts, pipes, etc. |
Cost | More expensive than gray cast iron | Cheaper than white cast iron |
Types | Ordinary, High-hardness, High-wear-resistant, High-temperature, Hollow | Based on the matrix structure: Ferritic, Pearlitic, Martensitic, etc. |
This table highlights the key differences between white cast iron and gray cast iron, which can help in selecting the appropriate material for specific applications.
White Cast Iron vs. Gray Cast Iron: Which Is Better?
The choice between white and gray cast iron depends on the specific requirements of the application. White cast iron is better suited for high-wear and abrasive environments, while gray cast iron is ideal for components requiring good machinability and toughness. Each material has its strengths and limitations, making the selection process dependent on factors such as load, temperature, and impact resistance.