After Tesla first introduced chassis integrated die-casting, Chinese automakers quickly followed suit in the manufacturing field, moving towards an era of high efficiency. The innovation of ultra-large tonnage die-casting technology began after the “9,000 tons” arms race. This time, Tesla may have given up the integrated die-casting of the chassis and side panels on the Model 2. How should we view this?
The Arms Race of Integrated Die-Casting
The manufacturing technology of new energy vehicles is constantly innovating. Large-tonnage die-casting technology is bringing a new revolution to the manufacturing of new energy vehicles. Ultra-large-tonnage die-casting technology refers to the manufacturing process of using die-casting machines to form large automotive parts in an integrated manner. Die-casting machines of different tonnage levels can complete the manufacturing of automotive parts of different scales and complexities. From 6000T to die-casting machines above 20000T, each level corresponds to different manufacturing capabilities and application ranges.
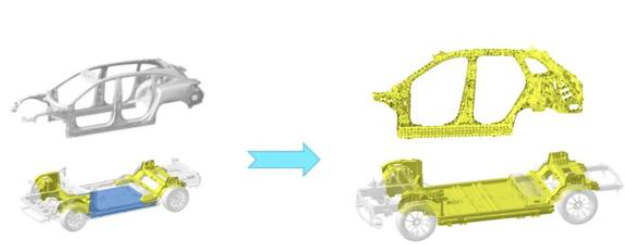
- -6000T-class die-casting machines can produce integrated rear floors, such as the rear floor of Tesla’s Model Y, which is formed by a 6000T-class die-casting machine.
- -9000T die-casting machines can produce larger tonnage front cabins or rear floors, such as the rear floor of Xiaomi and the rear floor of Tesla Cybertruck.
- -12000T die-casting machines can produce integrated battery shells.
- -16000T die-casting machines can achieve integrated molding of chassis for A00-class vehicles.
- -20000T+ die-casting machines will achieve integrated die-casting of chassis and side panels for B-class vehicles and larger models.
Why Did Tesla Abandon the Integrated Die-Casting of the Lower Chassis
Key components such as Tesla’s Model Y rear floor and Cybertruck’s rear floor can be integrated into one, greatly reducing the number of parts. The inherent advantages here are very clear.
- -The number of parts will be greatly reduced: the lower body has more than 100 parts, which are combined into 1 part; the side panel has about dozens of parts on one side, which are combined into 1 part.
- -Reduction in weight reduction of the whole vehicle: the lower body + side panel has a weight reduction of more than 10%.
- -The whole vehicle process reduces the number of welding points: the lower body + side panel has about several thousand welding points, which is reduced by about 80%.
- -The whole vehicle process and the process are reduced: the lower body and side panel have about dozens of processes.
- -The whole vehicle process can reduce a lot of labor and equipment investment: the lower body + side panel has dozens or even hundreds of workers and more than one hundred robots.
- -Reduction in the use of colloid: the amount of glue used is reduced by more than half.
- -The whole vehicle development cycle is greatly shortened.
So why didn’t Tesla continue to develop it? The biggest challenge here is still the yield rate and the transformation of the factory. Tesla previously proposed a new assembly process called “unbox”. Unlike the assembly line operation method of traditional production lines, this new process is more like “assembling Lego bricks”: the car body does not need to be assembled in sequence on a conveyor belt as before. Tesla plans to assemble different parts of the vehicle at the same time in a dedicated area of the factory, and finally assemble these large sub-assemblies together. Compared with traditional car factories with the same output, this new process is expected to halve production costs and reduce the floor space required for manufacturing by more than 40%. Of course, this is not without cost. This process requires factory investment and contains a lot of experimental content.
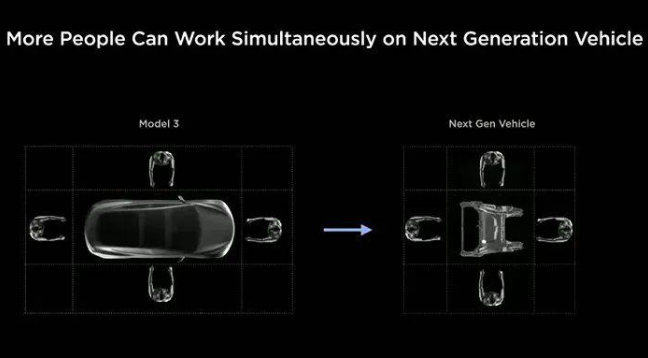
The innovation of ultra-large tonnage die-casting technology marks the entry of new energy vehicle manufacturing into a more efficient and sustainable era. The path pioneered by Tesla may rely on the continuous iteration and development of the Chinese supply chain.