Zinc alloy die casting is a kind of precision casting method, which uses high pressure to force metal melt into complex metal mold. Now the parts manufactured by zinc alloy die casting service are widely used in all kinds of decoration, such as furniture accessories, building decoration, bathroom accessories, automotive accessories, toys, metal buckle, etc. Therefore, the casting surface quality is required to be high, and the good surface treatment performance is required. The most common defect of zinc alloy die castings is surface forming bubbles. It mainly appear that there are protuberant bubbles on the surface of zinc alloy die casting parts, which are found after die casting process, exposed after polishing or machining, and appeared after oil spraying or electroplating. Below we detail zinc alloy die casting blistering defect causes and provide the solutions.
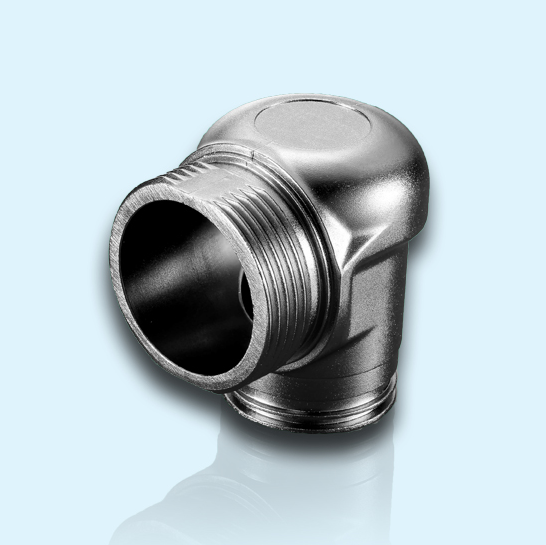
What Cause Bubbles In Zinc Alloy Die Casting
1. Porosity
It is mainly caused by pores and shrinkage mechanism. Pores are often round, and shrinkage is mostly irregular.
The causes of porosity are as follows:
● In the process of filling and solidification of molten metal, due to the invasion of gas, the surface or interior of the casting will produce holes.
● The gas volatilized from the paint invades.
● The gas content of alloy liquid is too high and precipitates during solidification. When the gas in the mold cavity, the gas emitted from coating and the gas precipitated from alloy solidification are not good at exhausting in the mold, the air hole formed in the casting is finally formed.
The causes of shrinkage cavity are as follows:
● During the solidification process of molten metal, shrinkage cavity is produced due to the reduction of volume or the lack of liquid metal feeding at the final solidification position.
● The uneven thickness of the zinc alloy die casting or the local overheating of the casting results in the slow solidification of a certain part, and the concave position is formed on the surface when the volume shrinks. Due to the existence of blowholes and shrinkage cavities, water may enter into the holes during surface treatment of die castings. When baking after painting and electroplating, the gas in the holes will expand due to heat; or the water in the holes will change into steam and expand in volume, resulting in foaming on the surface of zinc ally die castings.
2. Intergranular corrosion causes
Harmful impurities in zinc alloy composition: lead, cadmium and tin will gather at the junction of grains, causing intergranular corrosion, and the metal matrix will be broken due to intergranular corrosion. Electroplating accelerates this disaster. The parts affected by intergranular corrosion will expand and jack up the coating, resulting in bubbles on the casting surface. Especially in humid environment, intergranular corrosion will make the zinc die casting deformed, cracked and even broken.
3. Cracks: water marks, cold cracks, hot cracks
Water mark and cold shut off line:
● During the filling process, the molten metal that enters first contacts the mold wall and solidifies prematurely, and then the molten metal cannot be fused with the solidified metal layer, resulting in overlapping lines and strip defects at the butt joint of the casting surface. Generally, the water marks are shallow on the surface of the casting, while the cold insulation may penetrate into the inside of the casting.
Hot crack:
● When the casting thickness is uneven, the solidification process will produce stress.
● If the casting is pushed out prematurely, the metal strength is not enough.
● When the casting is ejected, the stress is uneven
● If the mold temperature is too high, the grain will be coarse.
● Harmful impurities exist.
The above factors may cause cracks. When there are water marks, cold cracks and hot cracks in the zinc alloy die casting, the solution will penetrate into the cracks during electroplating, and it will be converted into steam during baking, and the air pressure will lift the electroplated coating to form bubbles.
Solutions To Bubble Defects
– The key to control porosity is to reduce the amount of gas mixed into the casting. The ideal metal flow should be continuously accelerated from the nozzle through the splitter cone and runner into the mold cavity to form a smooth and consistent metal flow. The conical runner design is adopted, that is, the pouring flow should be gradually reduced from the nozzle to the gate, which can achieve this goal. In the filling system, the mixed gas is due to the mixing of turbulence and liquid metal to form pores. From the study of simulating zinc alloy die casting process of molten metal from the casting system into the cavity, it is obvious that the sharp transition position in the gate and the increasing cross-section area of the gate will make the metal flow turbulent and air entrained, and the stable molten metal is conducive to the gas from the gate and cavity to the overflow groove and exhaust groove out of the mold.
– For shrinkage cavity: to make all parts of zinc alloy die casting solidification process at the same time, uniform heat dissipation and solidification at the same time. The shrinkage cavity can be avoided by reasonable nozzle design, gate thickness and location, mold design, mold temperature control and cooling. For intergranular corrosion, it is mainly to control the content of harmful impurities in alloy raw materials, especially lead < 0.003%. Pay attention to impurity elements brought by waste.
– For water marks and cold shut-off marks, the mold temperature can be increased, the speed of inner gate can be increased, or the overflow groove in the cold shut-off area can be increased to reduce the appearance of cold shut-off pattern.