Toyota Motor Corporation’s mold design and manufacturing technology has many unique features in management and technology. This article makes a preliminary discussion on mold production and manufacturing technology and may provide some reference and inspiration for domestic automotive mold colleagues who are eager to improve production methods, promote scientific management, and improve manufacturing technology levels.
Japan’s manufacturing skills are a long-standing myth that has been circulated in the economic and automotive circles. Toyota, we believe everyone is familiar with it, has reached world-class mold design and manufacturing technology, and is unique in both management and technology. The world’s automotive mold manufacturing technology is developing in these directions: operations in front of computers are gradually replacing on-site operations, high-precision processing is replacing manual labor, the design and manufacturing of molds are highly standardized, single-piece production methods are developing towards assembly line production methods, etc.
Mold design is divided into three parts: stamping process design, die surface design, and structural design. Combined with China’s domestic mold manufacturing situation, Toyota is very different from us in the following aspects.
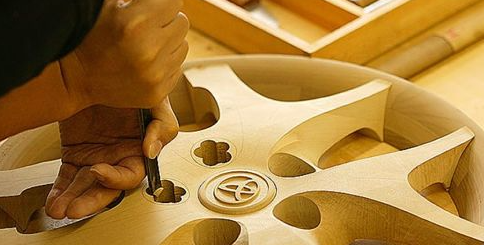
Toyota’s Stamping Process Design and Die Surface Design
- Fine Mold Surface Design:
Toyota completes the fine design of the mold surface through computer-curved surface modeling during the design stage. For example: various draw beads are designed for different feed amounts, draw beads have different cross-sections in different parts of the same mold set, anti-rebound, over-draw processing, minimum pressing surface design, unequal gap design of convex and concave molds, etc. The result of fine mold surface design can greatly reduce mold surface processing, reduce clamp repairs, and reduce mold trial man-hours. Its role is of no small importance. In contrast, domestic mold design is still in the structural design stage, and the backwardness of mold design has caused the backwardness of manufacturing.
- Application of Sheet Metal forming Analysis Technology:
Toyota has established a library of analysis results of various typical parts of the entire vehicle body. For parts of a new car model, if the formability does not change much, the original process will only be referred to without analysis. Only special new shapes will be analyzed for sheet metal forming. When Toyota’s new cars are prototyped, in addition to sheet metal forming analysis, simple molds are usually made for verification of parts with special shapes.
- Mold Surface Design Experience Accumulation Mechanism:
In addition to manual sketches, Toyota’s design department has all designs computerized. In addition to a workstation, general designers also have a laptop computer. However, truly creative design still relies on the human brain, especially on the accumulation of human experience. Toyota places special emphasis on the experience accumulation mechanism: there is only collective experience and not individual experience. Toyota’s mold design and debugging process is truly a closed-loop manufacturing system. With the help of this self-improving experience accumulation mechanism, the design of the mold is More and more refined, more and more accurate.
- Gap Diagram Design:
In Toyota, die surface design is completed in two parts: surface modeling and NC programming. To convey and describe the die surface design ideas, a third type of design besides the DL diagram and mold diagram was produced. Diagram— A Gap diagram is also called a quality assurance diagram.
- The Impact of Mass Production on Design:
Toyota’s production scale is world-class, and it has extensive experience in how mold design adapts to the requirements of mass production.
Tips:
-Improve material utilization
-Reduce stamping process
-Quick replacement of molds
Toyota’s Mold Structure Design
- Design has two purposes: one is for the design itself, and the other is for manufacturing. Designers gradually improve their design ideas during the drawing process. On the other hand, design should be oriented to manufacturing, with the ultimate goal of improving production efficiency.
- Solid design: Separation of mold surface design and structural design: Toyota completely separates mold structural design and mold surface design. The former is a solid design, while the latter is still a curved surface design. In the structural design, the mold surface part is only schematic and can be used for real-shaped processing, but not for mold processing. This division of labor greatly simplifies mold physical design.
- Real-shape CNC processing: At Toyota, real-shape production employees have completely transformed from manual production to a large number of CNC programming. Simple manual bonding and trimming work on site are performed by temporary workers. The CNC production of real shapes directly benefits the physical design and improves the accuracy of castings, which brings great advantages to subsequent fine processing.
- CNC machining of structural surfaces: Mold structural surfaces are machined surfaces other than the mold surface, such as guide surfaces, insert mounting surfaces, screw holes, other surfaces that need to be processed, etc. These are also programmed and CNC processed at Toyota. Processed. Solid design brings the possibility of CNC programming processing of the construction surface of the mold. Toyota has truly achieved CAD/CAM integration on the mold structure through physical design. Only through integration and eliminating the constraints of drawing two-dimensional drawings can physical design show its value. The two should develop simultaneously and complement each other.
Tips:
-High-precision processing of profiles
-High-precision machining of two-dimensional cutting edges
-The effect of high-precision machining
The mold industry has a strong tendency to move to the third world. Through the development of Toyota, we have some new understandings. Mold production relies more and more on high technology, which can completely reduce manual labor to a very low level. The most important needs of automobiles for mold production are high quality and short cycle. In large-scale automobile production, the cost of the mold itself is far less important than the cost of using the mold.
Toyota’s technology tells us: Good molds should be designed; molds can also be produced on assembly lines; high-tech applications are the driving force for the development of mold manufacturing technology; there is still a big gap between the domestic automotive mold industry and the world’s advanced level. If we don’t work hard, this gap will Instead of shrinking, it will expand. There are not many domestic automobile mold manufacturers, but they are not enough. Our high-quality mold market is occupied by mold factories in neighboring countries and regions. If we do not learn from the most advanced mold technology in the world, survival will become a big problem.