In modern industry, aluminum die casting technology is a widely used process for producing various aluminum components. However, recently, experts in the field of aluminum die-casting have raised an important question: why should the machining allowance in the hole of aluminum die-casting ingots not exceed 0.25 millimeters?
Aluminum die-casting is the process of injecting molten aluminum alloy into a specific mold and applying high pressure to manufacture components. During this process, the machining allowance inside the hole becomes a crucial issue. Experts emphasize that controlling the machining allowance in the hole is crucial for ensuring the quality and performance of aluminum die casting components.
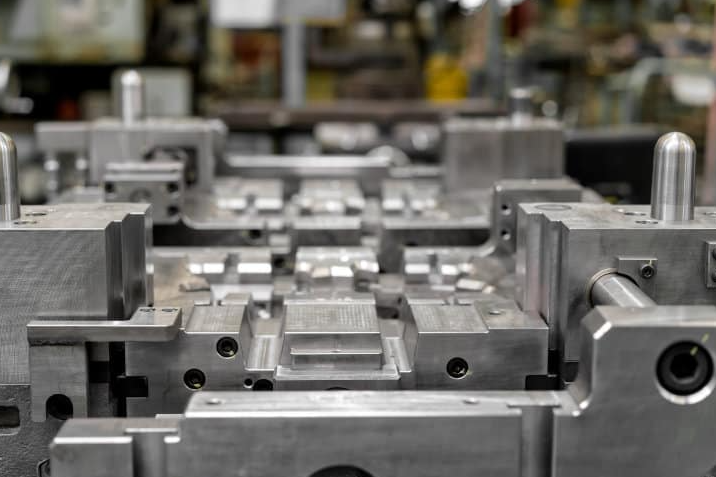
Reasons for Controlling the Machining Allowance in the Hole of Aluminum Die Casting Aluminum Ingots
1. Thermal conductivity: As an excellent thermal conductivity material, aluminum plays a crucial role in many applications. If the machining allowance inside the hole is too large, it may affect the thermal conductivity of the component. Therefore, controlling the margin can ensure that the thermal conductivity is not affected, especially in situations where rapid heat dissipation is required, such as electronic equipment heat sinks.
2. Mechanical properties: Aluminum die-casting components usually have to withstand various mechanical stresses, so their mechanical properties are crucial. Excessive machining allowance in the hole may lead to a decrease in the strength and durability of the components. By controlling the margin, it is ensured that the components perform well under stress, thereby improving their reliability.
3. Lubrication and sealing: In some applications, the holes of components need to be used for lubrication or sealing. If the margin is too large, it may affect the sealing performance or even distribution of lubricants. Therefore, controlling the margin inside the hole can ensure the normal operation of these critical functions.
4. Assembly and matching: Components usually need to be assembled with other components or equipment. If the machining allowance in the hole is not controlled, it may lead to assembly problems and require more time and resources to adjust the components to ensure compatibility. Therefore, controlling the margin can improve the assembly efficiency of components.
Application Fields of Aluminum Die Casting Technology
Automotive parts (aluminum alloy die casting): Die casting manufacturing technology is widely used in the automotive industry. For example, key components such as the cylinder head, cylinder block, and crankcase of automotive engines are often manufactured using die casting technology. Due to the ability of die casting to achieve complex shapes and high-precision manufacturing, it can provide better sealing and structural strength, making automotive components more durable and reliable.
Electronic product shell (aluminum alloy die-casting): Many electronic products, such as mobile phones, computers, cameras, etc., require a lightweight, sturdy, and aesthetically pleasing shell. Die casting manufacturing technology can meet these requirements, and through the die casting process, thin-walled shell structures can be produced while maintaining good strength and surface quality. This enables electronic products to be fully utilized in terms of appearance design and performance.
Home appliance accessories (aluminum alloy die casting): Die casting technology is also widely used in the field of home appliances. For example, many metal components in household appliances such as televisions, washing machines, air conditioners, etc., such as shells, bases, sockets, etc., can be manufactured through die casting technology. Die casting manufacturing technology can provide highly accurate dimensional control and excellent surface quality, making household appliances more beautiful, durable, and easy to assemble.
Kitchen utensils (aluminum alloy die-casting): The die-casting process is also widely used in the manufacturing of kitchen utensils. For example, cooking utensils, oven accessories, coffee machine parts, etc. can all be produced through die-casting technology, which has good heat resistance and durability.
Luggage accessories (zinc alloy die casting): Some luggage accessories, such as zipper heads, fasteners, etc., are often manufactured using die-casting technology. These accessories usually require high strength and durability, while also requiring a beautiful appearance, and the die-casting process can meet these requirements.