Car lights are the most important finishing touch in a car’s appearance, integrating optical function and appearance. With the development of the automobile industry, light-emitting parts have more applications inside and outside the car, such as ambient lights, light-emitting interiors, logo lights, etc. At the same time, the car lamp mold is relatively special among all injection mold types. It has a large gap in size and needs to take into account the microstructure. The design and processing requirements of the mold are extremely demanding.
Next, we take the typical car light model of “manual valve V-6 throttle body” as an example to briefly introduce how to implement an efficient and safe programming solution in the software environment.
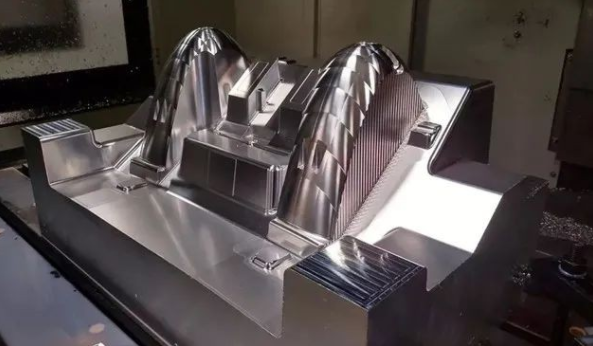
Seamless connection between CAD and CAM
Before programming begins, CAM programmers usually import graphics into WORKNC and then use the advantages of WORKNC CAD to make minor modifications to the original design during the programming process. Thanks to the seamless connection between WORKNC CAD and CAM, modifications to the CAD model made by CAM programmers are automatically reflected and saved in the CAM program.
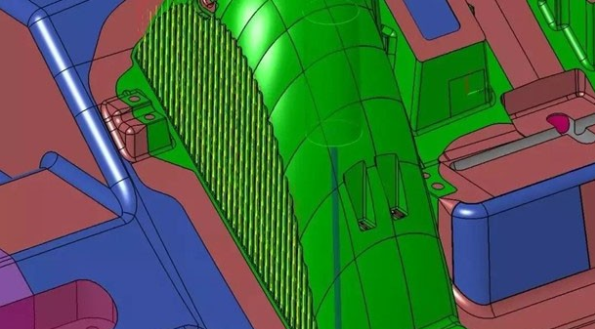
Batch computing improves computing efficiency
Many software cannot perform multi-core calculations at the same time, but WORKNC can. This is a powerful feature of WORKNC. By using the batch calculation function of WORKNC to program parts and simultaneously calculate multiple tool paths on different stock models, time is effectively saved. In practical applications, WORKNC can edit multiple tool paths at the same time, and it is common for a company to automatically calculate 16 tool paths at the same time. The WORKNC batch calculation function allows users to put the calculation steps in the background and run them in batches after programming. At the same time, the user interface can still handle other work and make full use of the PC’s processing power. WORKNC’s multi-core parallel computing function allows multiple tool paths in the working directory to be calculated simultaneously, as long as there is no inheritance relationship between them.
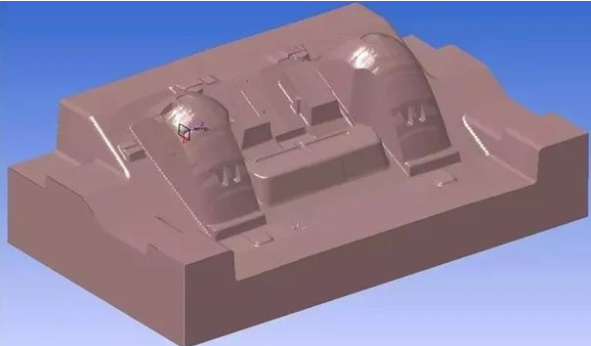
Automatic feature recognition function makes processing more flexible
WORKNC’s automated feature recognition function saves programmers time in identifying and defining workpiece types, features, and dimensions, and greatly saves the CAM programming department additional time. Once the CAD model is imported into WORKNC, WORKNC can automatically identify the features of the parts and process them. Automatic feature recognition recognizes all hole types, whether threaded, drilled, or otherwise.
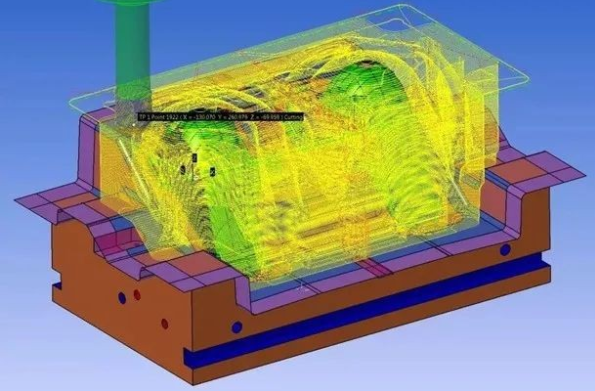
For CAM engineers, the use of WORKNC’s working directory for template programming is another time-saving feature. The WORKNC working directory is simple to operate, maintains the integrity of the entire programming process, and allows multiple programmers to work on a program in different locations. In most cases, roughing tools are done by programmers on the shop floor, while finishing tools are done by experienced programmers. After the programmer completes the roughing tool path editing, he exports the template with new parameters and then passes it to other programmers. After using WORKNC, the machining efficiency of CAM programmers has been significantly improved. It used to take a week to complete only part of a V-6 throttle body model equipped with a manual valve. Now it only takes 90 minutes to complete it using WORKNC.