Zinc plating is one of the most commonly used and effective methods for preventing rust and corrosion on metal surfaces. It protects a wide range of materials from mild steel to aluminum through the application of a thin layer of zinc. While the basic protective function remains the same, zinc plating is available in various color options that each offer their own unique advantages depending on application needs and environment. Today, we’re going to find out the differences between yellow, clear, blue, black and green zinc plating.
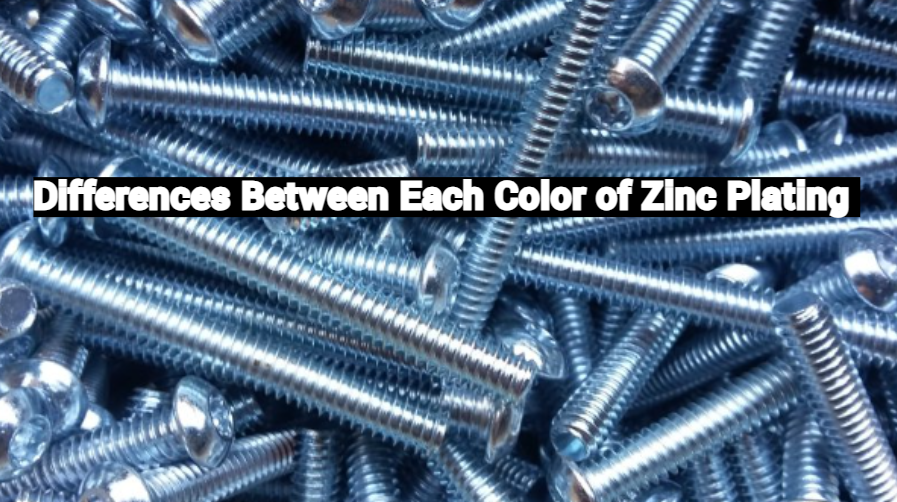
What’s Zinc Plating?
Zinc plating is an electrochemical process that involves applying a thin layer of zinc onto the surface of metal objects, typically made of steel or iron, to protect them from corrosion. This is achieved by immersing the metal parts into a zinc-containing electrolyte solution and passing an electric current through it, causing zinc ions to deposit onto the substrate. The resulting zinc coating acts as a sacrificial barrier, corroding preferentially to the underlying metal and thereby extending the lifespan of the component. Commonly used for small parts like fasteners, crank handles, and springs, zinc plating enhances corrosion resistance and can also improve the aesthetic appearance of metal items.
What’s Zinc Color?
Zinc plating can be finished in various colors, primarily determined by the type of chromate conversion coating applied after the zinc layer. These colors not only enhance the aesthetic appeal but also indicate varying levels of corrosion resistance:
- Clear/Blue: This finish offers a bluish-silver appearance and is commonly used for machine parts, washers, and screws. It provides moderate corrosion resistance and is often chosen for its clean, decorative look.
- Yellow/Gold: Recognized for its bright, shiny gold hue, this finish is valued for both its aesthetic appeal and enhanced corrosion protection. It’s frequently applied to components where appearance and durability are important.
- Black: Achieved through a black chromate coating, this finish ranges from olive drab to pure black. It offers a higher level of corrosion resistance and is often used decoratively, especially in automotive applications.
- Olive Drab Green: This greenish finish provides robust corrosion resistance and is typically used in military and outdoor equipment applications.
The choice of zinc plated color impacts both the visual appeal and the protective qualities of the coated item, with darker finishes generally offering greater corrosion resistance.
Zinc Plating Color Chart
Color | Description | Typical Applications |
---|---|---|
Yellow/Gold | Bright yellow-gold hue. Provides excellent corrosion resistance. | Automotive, heavy machinery, outdoor signs. |
Bright/Clear | Silvery-gray without additives. Good basic protection. | General hardware, industrial parts, appliances. |
Dark/Blue | Darker silvery-blue tone from special additives. | Machined parts, architectural detail, electronics. |
Black | True black finish from carbon additions. Maximizes rust prevention. | Decorative trims, artistic pieces, appliances. |
Green | Olive green from copper in solution. Less common color option. | Art pieces, ornate hardware, specialty industrial. |
Custom/Multi-Tone | Unique patterns or layered colors. More decorative focus. | Signage, trophies, appliances, artistic metalwork. |
Yellow vs Clear vs Blue vs Black vs Green Zinc Plating
Yellow Zinc Plating
Yellow zinc plating provides the highest level of corrosion protection against environmental factors like weathering. The bright yellowish hue makes components visibly stand out. This makes yellow zinc ideal for applications that require durable outdoor protection, such as automotive and heavy machinery parts that face continuous exposure. The bright pigment adds an extra robust layer of shielding compared to clear finishes.
Clear Zinc Plating
Clear zinc plating results in an inconspicuous silvery-gray tone. While it offers good foundational rust prevention, the corrosion resistance is not quite as strong as yellow zinc. However, its subtle appearance works well for general purpose uses where low visibility is preferable over maximizing resistance. It is often used as the default option due to having the most economical upfront cost compared to colored variants.
Blue Zinc Plating
Blue zinc plating contains special additives that produce a darker silvery-blue hue. This provides corrosion protection on par with clear zinc. The slightly darker shade also helps parts blend into backgrounds more easily. As such, blue zinc is commonly utilized for indoor applications and machinery where drawing attention is unnecessary. Its protective qualities combine utility with subtlety.
Black Zinc Plating
When paired with a black oxide undercoating, black zinc plating maximizes rust prevention through a synergistic barrier effect. The true black coloration also does an excellent job concealing wear marks and scratches over the service life. As a result, it sees extensive use in decorative trim, signs, and other applications where an dark aesthetic and intense resistance are valued.
Difference Between Yellow, Clear, Blue, Black and Green Zinc Plating Color
The choice of zinc plating color impacts both the visual appeal and the level of corrosion protection of the coated item. Darker finishes, such as black and olive drab, generally offer greater corrosion resistance compared to lighter finishes like clear or blue. Selecting the appropriate type depends on the specific requirements of the application, including environmental exposure and desired aesthetics.
Color | Appearance | Corrosion Resistance | Typical Applications |
Clear/Blue | Silvery with a blue tint | Moderate | Machine parts, washers, screws, ornamental purposes |
Yellow/Gold | Bright yellow-gold | High | Automotive components, heavy machinery, outdoor equipment |
Black | Deep black finish | High | Decorative trims, appliances, artistic pieces |
Green (Olive Drab) | Olive green | Very High | Military equipment, outdoor applications |
What Are The Advantages Of Each Zinc Plating?
Yellow/Gold Zinc Plating
- Provides excellent long-term corrosion resistance
- Bright color helps parts stand out and be identifiable
- Durable finish holds up well in harsh outdoor environments
Bright/Clear Zinc Plating
- Effective basic corrosion protection
- Subtle appearance suits applications where visibility is unimportant
- Inexpensive default option for general-purpose use
Dark/Blue Zinc Plating
- Offers good rust prevention while blending in visually
- More aesthetically subtle than bright finishes
- Suitable for applications where attention is unwanted
Black Zinc Plating
- Maximizes corrosion resistance when combined with a black oxide undercoat
- Hide scratches and wear better than lighter colors
- Attractive dark appearance works well for decorative uses
Green Zinc
- Provides aesthetic variation as an alternative to standard colors
- Durable formula withstands weathering
- Suitable color for specific industries or artistic applications
Custom/Multi-Tone Zinc
- Allows uniquely designed patterns and visual effects
- Creative finishes suitable for decorative/ornamental applications
- Enables specialized solutions for niche industrial needs
Prices For Each Zinc Plating Colour
Clear zinc tends to be the most budget-friendly due to its simplicity, while color variants entail higher costs relative to pigment usage and processing complexities. However, longer-lasting colorfully plated parts could prove more economical over the total lifecycle through reduced maintenance. Application needs ultimately dictate which zinc coating provides the best value.
Yellow Zinc Plating
Medium cost – More expensive than clear zinc due to pigment additions required.
Clear Zinc Plating
Lowest cost – Basic zinc plating without pigments, making it the most affordable option.
Blue Zinc Plating
Comparable to clear zinc – Similar protection to clear with minor pigment additions, so pricing is around the same level.
Black Zinc Plating
Higher than blue/clear, lower than yellow – Pigments for true black hue increase cost over clear/blue zinc.
Green Zinc Plating
Higher than standard colors – Custom pigments drive up cost of this less common option.