In the world of metal protection and application, two common techniques stand out: zinc plating and galvanizing. Both involve coating steel with zinc to fend off corrosion, but as we’ll discover, their differences run deep and dictate their suitability for various scenarios. Whether you’re considering the construction of a towering skyscraper, the assembly of a delicate household appliance, or anything in between, understanding the differences between zinc-plated and galvanized steel is crucial. In this galvanized vs zinc plated guide, we’ll delve into the details and explore how these two processes shape the durability, appearance, and functionality of the steel we rely on daily.
What’s Zinc Plated Steel?
Zinc-plated is a process in which a layer of zinc is applied to the surface of metal objects, typically steel or iron, to protect them from corrosion and rust. The zinc coating acts as a sacrificial barrier, meaning it corrodes first, thereby safeguarding the underlying metal. This process is commonly done through electroplating, where the metal is submerged in a zinc-containing solution and an electric current is applied to bond the zinc to the metal’s surface. Zinc plating is widely used in automotive parts, hardware, fasteners, and industrial components to enhance durability and longevity while maintaining a clean, shiny appearance.
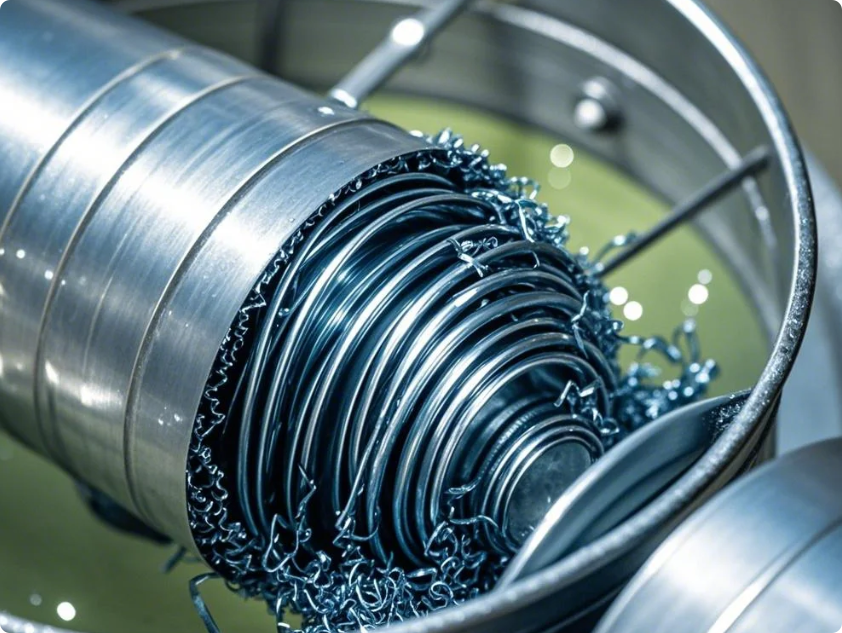
Zinc Plated Steel Applications
Zinc-plated steel is widely used in applications where moderate corrosion resistance and a clean, shiny appearance are desired. Common applications include:
Automotive Parts: Fasteners, bolts, nuts, and brackets to resist corrosion.
Hardware and Fasteners: Screws, nails, hinges, and connectors used in construction and woodworking.
Electrical Components: Conduits and fittings to protect against moisture and corrosion.
Plumbing and Piping: Fittings and connectors that need protection from rust.
Appliances and Household Items: Handles, knobs, and decorative hardware.
Industrial Machinery: Parts and components that need a balance of protection and aesthetic appeal.
Consumer Products: Bicycles, tools, and other metal items that benefit from increased durability.
Zinc Plated Steel Properties
Corrosion Resistance: The zinc coating acts as a sacrificial layer, protecting the underlying steel from rust and oxidation.
Shiny Appearance: It has a bright, smooth, and shiny finish, making it visually appealing for decorative and visible applications.
Moderate Durability: While resistant to corrosion, it is less durable than galvanized steel and is best suited for indoor or mild outdoor environments.
Adhesion and Bonding: The electroplated zinc layer adheres well to the steel surface, forming a uniform coating.
Cost-Effective: Zinc plating is relatively inexpensive compared to other protective coatings, making it an economical choice.
Thin Coating Layer: The coating is typically thin (measured in microns), which helps maintain dimensional accuracy for precision parts.
Conductivity: Zinc-plated steel can conduct electricity, which is useful for some electrical and grounding applications.
What’s Galvanized Steel?
Galvanized steel is steel that has been coated with a protective layer of zinc to prevent rust and corrosion. This coating is typically applied through a process called hot-dip galvanizing, where the steel is submerged in molten zinc, forming a strong metallurgical bond. The zinc layer acts as a sacrificial barrier, corroding before the underlying steel does, which significantly extends the steel’s lifespan, even in harsh environments. Galvanized steel is commonly used in construction, outdoor structures, automotive parts, and household appliances due to its durability, corrosion resistance, and relatively low cost.
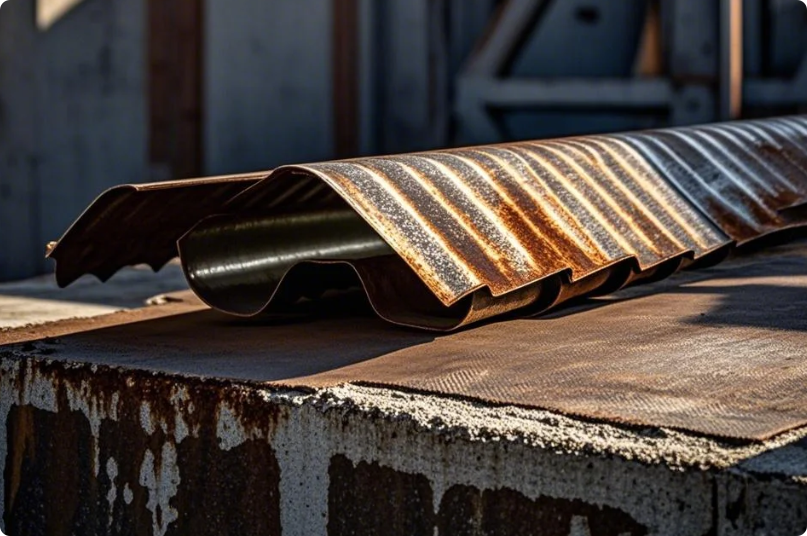
Galvanized Steel Properties
High Corrosion Resistance: The zinc coating protects the underlying steel from rust and oxidation, even in harsh environments.
Durability: The hot-dip galvanizing process forms a metallurgical bond that makes the coating tough and long-lasting.
Self-Healing Capability: If the coating is scratched or damaged, the zinc continues to protect the exposed steel by sacrificing itself (galvanic protection).
Matte to Shiny Finish: Depending on the process and thickness of the coating, it can have a dull gray or shiny silver appearance.
Longevity: Can last for decades without significant maintenance, especially in non-aggressive environments.
Temperature Resistance: Performs well under a wide range of temperatures, making it suitable for outdoor and industrial applications.
Cost-Effective Maintenance: Requires minimal upkeep over its lifespan, reducing long-term costs.
Adhesion and Bonding: Coating bonds strongly to the steel surface, reducing the risk of peeling or flaking.
Galvanized Steel Applications
Construction and Infrastructure: Used for beams, frames, guardrails, fences, and roofing to protect against weather and corrosion.
Automotive Industry: Used for body panels, chassis parts, and frames to enhance rust resistance.
Utility and Power Transmission: Utility poles, towers, and transmission line hardware are commonly galvanized to withstand outdoor exposure.
Agriculture and Farming Equipment: Protects machinery, fencing, and storage tanks from corrosion.
Household Appliances: Washing machine parts, water heaters, and HVAC ducting to enhance longevity.
Outdoor Structures: Street lamps, signposts, playground equipment, and bike racks to resist weathering.
Marine Applications: Suitable for docks, buoys, and coastal structures where high humidity and salt exposure occur.
Galvanized steel is favored when long-lasting durability and re
Zinc-Plated vs Galvanized Steel: What’s the Difference?
When it comes to galvanized steel vs zinc plated, both zinc-plated and galvanized steel are coated with zinc to protect against corrosion, but they differ significantly in their coating methods, durability, and applications.
- Coating Process:
Zinc-Plated Steel: Coated using an electroplating process, where a thin layer of zinc is applied to the steel surface.
Galvanized Steel: Coated through hot-dip galvanization, where the steel is submerged in molten zinc, forming a thicker and more durable layer. - Coating Thickness:
Zinc-Plated: Thin coating, usually around 0.2–0.5 mils (5–12 microns), providing moderate corrosion resistance.
Galvanized: Thicker coating, typically 1.0–4.0 mils (25–100 microns), offering superior protection. - Corrosion Resistance:
Zinc-Plated: Suitable for indoor or mild environments, as it corrodes relatively quickly when exposed to harsh conditions.
Galvanized: Ideal for outdoor and harsh environments due to its thick, rugged coating. - Appearance:
Zinc-Plated: Bright, shiny, and smooth finish.
Galvanized: Dull gray or spangled appearance, with a slightly rough texture. - Durability:
Zinc-Plated: Less durable, prone to rust if the coating is damaged.
Galvanized: More durable and resistant to scratches, with self-healing properties if damaged. - Applications:
Zinc-Plated: Indoor hardware, fasteners, and small automotive parts.
Galvanized: Outdoor structures, construction materials, utility poles, and marine applications.
Aspect | Zinc-Plated Steel | Galvanized Steel |
Coating Process | Electroplating – thin zinc layer | Hot-dip galvanization – thick zinc layer |
Coating Thickness | 0.2–0.5 mils (5–12 microns) | 1.0–4.0 mils (25–100 microns) |
Corrosion Resistance | Moderate – suitable for indoor use | High – suitable for outdoor and harsh environments |
Appearance | Bright, shiny, smooth finish | Dull gray or spangled, rough texture |
Durability | Less durable, prone to rust if damaged | Highly durable, self-healing if damaged |
Applications | Indoor hardware, fasteners, small automotive parts | Outdoor structures, construction materials, marine applications |
What Lasts Longer Zinc vs Galvanized?
When zinc vs galvanized steel, galvanized steel lasts significantly longer than zinc-plated steel, especially in outdoor or harsh environments. This is because galvanized steel has a much thicker zinc coating (typically 1.0–4.0 mils or 25–100 microns) compared to zinc-plated steel (0.2–0.5 mils or 5–12 microns).
The thicker coating in galvanized steel provides superior protection against corrosion, rust, and environmental factors, allowing it to last for decades (often 20–50 years or more) without significant deterioration. Zinc-plated steel, on the other hand, is more suitable for indoor applications and may start corroding within a few years when exposed to moisture or outdoor conditions.
When to Use Galvanized Steel or Zinc Plated Steel?
The choice between galvanized steel and zinc-plated steel largely depends on the environment and the level of protection needed:
Use Zinc-Plated Steel When:
Indoor Applications: Zinc plating is best for dry, indoor environments where exposure to moisture and harsh conditions is minimal.
Aesthetic Appeal: It has a bright, shiny finish that is more visually appealing than galvanized steel, making it suitable for decorative hardware and fittings.
Light Protection Needs: When you only need superficial corrosion resistance and aesthetic value, like in household appliances, fasteners, and indoor hardware.
Cost Efficiency: Zinc plating is cheaper than galvanizing and suitable for less demanding conditions.
Use Galvanized Steel When:
Outdoor or Harsh Environments: Ideal for areas exposed to moisture, rain, or corrosive substances, such as construction materials and outdoor structures.
Heavy-Duty Applications: Suitable for applications where longevity and robust corrosion resistance are critical, like utility poles, guardrails, and marine environments.
High-Temperature Exposure: Hot-dip galvanized steel can withstand higher temperatures (up to 200°C), while zinc plating may peel at elevated temperatures.
Structural Components: Use when you need a thicker, more durable coating that can last decades without significant maintenance.
Avoid Cold Galvanizing:
Cold galvanizing, which is essentially painting with zinc-rich primer, offers minimal protection and is prone to rust if scratched. It’s not true galvanizing and should be avoided for critical applications.
Zinc Plated vs Galvanized for Outdoor Use
Is zinc or galvanized better for outdoor use, galvanized steel is undoubtedly the better choice compared to zinc-plated steel. The primary reason lies in the difference in coating thickness and durability. Galvanized steel undergoes a hot-dip galvanizing process where the steel is immersed in molten zinc, forming a thick, robust coating that typically measures around 50 microns or more. This coating not only provides long-lasting protection but also forms a metallurgical bond with the steel, making it resistant to weathering, moisture, and corrosion. As a result, galvanized steel can last for 30 to 40 years or even longer without significant deterioration, making it ideal for outdoor applications.
One of the most significant advantages of galvanized steel is its self-healing property. Even if the coating gets scratched or damaged, the zinc continues to protect the exposed steel through a process called galvanic protection. This makes galvanized steel especially suitable for environments prone to abrasion or harsh weather, such as outdoor structures, utility poles, fences, guardrails, and marine applications. Its ability to withstand rain, snow, humidity, and salt spray ensures that it remains durable and reliable over extended periods.
On the other hand, zinc-plated steel is not suitable for outdoor use. The zinc coating, applied through an electroplating process, is much thinner—usually around 3 microns. While it gives a shiny and attractive finish, this thin coating wears off quickly when exposed to outdoor conditions. Once the coating is compromised, the underlying steel is vulnerable to rust and corrosion. Unlike galvanized steel, zinc-plated steel does not possess self-healing properties, meaning that even minor damage can lead to rapid deterioration.
Zinc Coated vs Galvanized, Which is Better
The terms “zinc-coated” and “galvanized” are often used interchangeably, but there’s a subtle difference—and which one is better depends on your needs.
Zinc-Coated simply means a layer of zinc has been applied to the surface of the metal, often through a process like electroplating. This layer is typically thinner and smoother, providing moderate corrosion resistance. It’s ideal for indoor applications or areas with less exposure to harsh weather.
Galvanized metal, on the other hand, typically refers to hot-dip galvanizing, where the metal is submerged in molten zinc. This results in a thicker, rougher coating that offers stronger, longer-lasting protection against rust and corrosion, especially in outdoor or industrial environments.
So, which is better?
- For heavy-duty, long-term protection, especially outdoors: Galvanized is better.
- For lighter, more aesthetic or indoor applications: Zinc-coated might be sufficient and more cost-effective.
Is Zinc Plated Rust Proof
Zinc plating is not entirely rust-proof, but it does provide good corrosion resistance. The zinc coating acts as a sacrificial layer, meaning it corrodes before the underlying metal (usually steel or iron) does.
However, zinc-plated items can still rust over time, especially if:
- The plating gets scratched or damaged, exposing the base metal.
- They are exposed to harsh environments, like saltwater or acidic conditions.
- The coating is too thin or poorly applied.
Is Galvanized Plated Rust Proof?
Galvanized plating (or galvanization) significantly improves rust resistance but is not entirely rust-proof. It involves coating steel or iron with a thick layer of zinc, usually through a process called hot-dip galvanizing.
Why Galvanized Plating Resists Rust:
Sacrificial Protection: The zinc layer corrodes before the underlying steel, protecting it.
Barrier Protection: The thick zinc layer physically shields the steel from moisture and oxygen.
Self-Healing Property: If the coating gets scratched, the zinc can still protect nearby exposed steel through cathodic protection.
Limitations:
Corrosion in Harsh Environments: In highly acidic, alkaline, or saltwater environments, the zinc coating can still corrode over time.
Long-Term Wear: Over decades, even galvanized coatings can wear away, exposing the base metal to rust.
High-Quality Zinc Die Casting and Color Electrophoresis at Junying
Get high-quality zinc die casting services and color electrophoresis at Junying, a leading manufacturer specializing in precision casting and surface finishing solutions. With advanced die casting techniques, Junying produces durable and accurate zinc parts suitable for automotive, electronics, and industrial applications. Their color electrophoresis process provides a smooth, uniform, and corrosion-resistant coating, available in various colors to meet aesthetic and functional requirements. Whether you need complex zinc components or protective and decorative coatings, Junying offers reliable, cost-effective solutions tailored to your specifications.