When metal components require protective finishes or enhancing properties like conductivity, nickel and copper plating are two common and effective metal plating options to consider. Both nickel and copper coatings provide corrosion resistance and aesthetic benefits, but each also carries unique advantages tailored for specific applications. Today, we discuss zinc vs copper plating, to find out which is better copper plating or zinc plating.
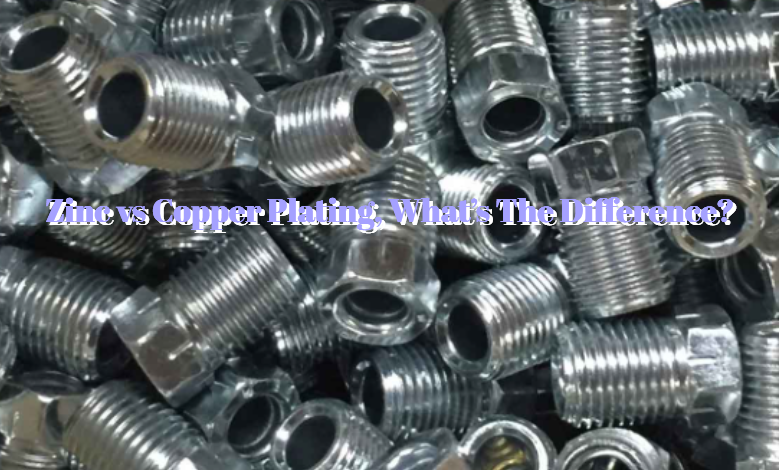
Zinc Plating vs Copper Plating, What’s The Difference?
Zinc plating typically provides better corrosion protection while copper offers increased durability, conductivity and tolerance to higher heats but requires extra protective sealing.
1. Appearance: Zinc plating produces a dull, slightly grey finish. Copper plating has a shiny bronze or golden brown color.
2. Corrosion Resistance:Zinc plating provides better corrosion resistance than copper and protects the base metal better. Copper needs a protective clear coat.
3. Durability: Zinc plating is more abrasion and impact resistant than copper. But copper bonds very well to metals and is less prone to cracking.
4. Chemical Resistance: Zinc is resistant to acids and alkalis while copper can be damaged by these and salt water environments.
5. Temperature Tolerance: Zinc maintains its protective properties up to 400°F. Above this it breaks down. Copper withstands higher continuous temperatures up to 1,000°F.
6. Conductivity: Copper is a better conductor of electricity and heat than zinc. Zinc is minimally electrically conductive.
7. Cost: Zinc plating is usually less expensive than copper plating due to material and processing costs.
8. Used For: Zinc for industrial/machinery parts, nails, hardware. Copper more common for decorative purposes, roofing, piping due to appearance.
What’s Nickel Plating?
Nickel Plating is a process in which a layer of nickel is deposited onto the surface of a material, usually metal, to enhance its properties such as corrosion resistance, hardness, and aesthetic appeal. This is typically achieved through electroplating, where the object to be plated is submerged in an electrolyte solution containing nickel salts, and an electric current is applied to reduce nickel ions onto the surface of the object. Nickel plating is widely used in various industries, including automotive, electronics, and manufacturing, for applications ranging from decorative finishes to improving wear resistance and reducing friction.
What’s The Advantage Of Zinc Plating?
Corrosion resistance – Zinc forms a protective layer that inhibits corrosion of the base metal underneath. This makes zinc plating very effective at preventing rust and corrosion damage over time.
Low cost – The process of zinc plating and the zinc material itself are relatively inexpensive compared to other metal finishing options like chrome or nickel plating. This makes it affordable.
Durability – When applied correctly, a zinc coating can withstand wear, weathering, chemicals and general use for years without cracking or peeling from the base metal.
Aesthetics – Zinc takes on a dull, silvery-grey appearance that looks attractive and hides minor imperfections or scratches in the underlying metal. It has an industrial appeal.
Easy repairs – Should the zinc coating become damaged, repairs are simple and inexpensive to do by just re-plating the exposed base metal areas.
Heat resistance – Zinc retains its protective properties and bonding strength up to approximately 400°F, withstanding moderate heating.
Environmental benefit – The zinc coating actually protects the base metal from further corrosion, reducing environmental impacts versus uncoated metals rusting away.
Copper Plating
Applicability – Zinc plating works on a wide variety of base metals like steel, iron, aluminum and more, providing uniform protective finishes.
What’s Copper Plating?
Copper Plating involves coating a substrate, typically a metal, with a layer of copper to improve conductivity, provide a base layer for additional plating, or enhance corrosion resistance. Similar to nickel plating, copper plating is commonly done through electroplating, where the object to be coated is immersed in a solution containing copper ions, and an electric current is used to deposit a uniform layer of copper onto the surface. Copper plating is particularly valuable in the electronics industry for creating conductive layers on circuit boards, as well as in the manufacturing of various components that require excellent thermal and electrical conductivity.
What’s The Advantage Of Copper Plating?
Appearance – Copper has an attractive golden-brown or reddish color that provides an aesthetically pleasing decorative finish.
Conductivity – Copper is a very good conductor of electricity and heat. This makes it suitable for electrical and electronic components where conductivity is important.
Machinability – Due to its softness, copper plates can be easily machined, stamped, formed or tooled after plating for different shapes without damage.
Solderability – Copper promotes strong, durable joints when soldered. This is useful in plumbing, electronics and other applications involving soldered connections.
Bonds strongly – Copper chemically bonds very well to various metal substrates, forming an integral part of the material rather than just a surface layer.
Corrosion resistant – When properly sealed with a transparent top coat, copper plates provides good long-term protection against corrosion from various environmental factors.
Low friction – The smooth copper surface has a low coefficient of friction, reducing wear for sliding mechanical connections and parts.
Long-lasting – Attractively aged copper finishes can develop a beautiful patina over decades rather than degrading like other coatings.
Reusable -surplus copper can be reclaimed and recycled for further industrial and manufacturing applications.
Which One Should You Choose, Copper or Nickel Plating?
When deciding between nickel and copper plating, it’s important to consider the intended application and desired properties as nickel and copper each have their own advantages. Nickel produces a bright silver finish and offers better durability and corrosion resistance, making it suitable for applications that require withstanding wear, weathering and harsh environments. However, copper has an attractive reddish-brown tone and higher conductivity, so it may be a better choice when heat transfer or electrical conductivity is important.
Copper is also softer and easier to machine after plating. Meanwhile, nickel can withstand higher temperatures. Though copper has a lower upfront cost, it requires a protective top coat for long-term corrosion protection. So nickel is typically a better choice for outdoor use or food contact surfaces, while copper can be a better functional material indoors where appearance is also a priority and the surface can be sealed.