As an important covering part of the automobile, the shape and quality requirements of the tailgate inner panel are constantly increasing. Its large curvature, deep depth, and complex shape determine that it is difficult to form deep drawings and is prone to problems such as cracking and wrinkling. Determining the drawing plan for the inner panel of the tailgate is the first problem to be solved. The drawing plan not only determines whether satisfactory parts can be formed but also affects the process supplement and the arrangement of each drawing process.
Deep Drawing Analysis
- 1. Upward convex single-action deep drawing plan
Depending on the shape of the part, due to the large curvature in both directions, an upward convex single-action deep drawing scheme is usually used, which is conducive to the inflow of material and the forming of the part. However, there are deep holes in the lower part of the tailgate and on the left and right sides. The reverse drawing, and the draft angle is small, and there is a risk of cracking.
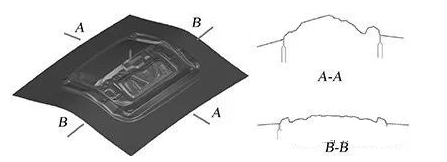
The sheet blank size is 1505mm × 1600mm, the pressing force is 1700kN, and the drawing stroke is 180mm. AutoForm software is used to analyze the drawing plan. In the three deep reverse drawing positions, cracking areas appear, such as shown in Figure 3. Reverse drawing also makes it difficult for the material to flow into the middle profile, and many features in the middle of the part also have obvious cracks.
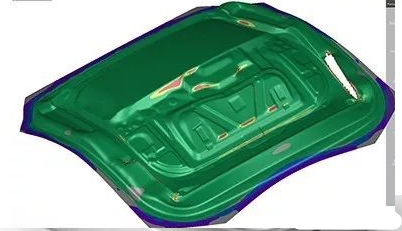
Due to the limitations of the stamping production line, the stamping direction of the parts cannot be turned 180° during the stamping production. When punching in the subsequent punching process of this drawing scheme, the punching burrs are directed into the car, causing the buckle to be difficult to jam when assembling the tailgate interior panel. into the mounting hole.
- 2. Concave double-action deep drawing solution
If there is no problem with the formability of the upward single-action deep drawing solution, and it is just to solve the problem of the punching burr direction, so that the punching direction is from the inside of the car to the outside of the car, you can choose to deep-draw the part in the direction shown in Figure 4. In the single-action press, a nitrogen gas spring is used to provide pressing force for the upper molding edge ring to achieve a double-action deep drawing of a single-action press.
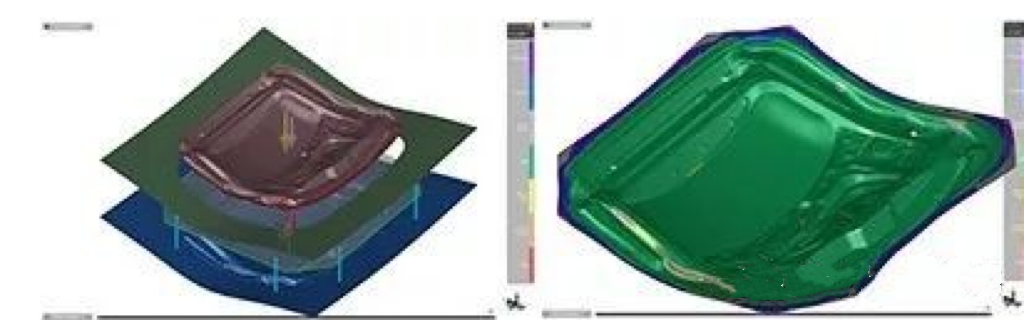
This solution only solves the problem of punching burrs. Its essence is that the punching direction of the upward-convex single-action solution is rotated 180°, which does not improve the formability of the part. It also brings two problems: ① Since both the upper and lower parts of the part need to be For hook wedge trimming, considering the strength and aspect ratio of the subsequent trimming knife, the drawing replenishment will be larger than the single-action scheme design, as shown in Figure 5, resulting in a reduction in material utilization; ② The press ring uses a nitrogen spring As a pressure source, the pressure usually exceeds 1500kN. When the slider rises from the bottom dead center after the drawing is completed, since the nitrogen spring does not have a locking function, the nitrogen spring has enough force to push the slider upward, and the main motor changes from an electric motor to a The generator generates feedback current, causing the system to take braking action, resulting in unnecessary wear of the brake pads.
In production, if unexpected wear occurs, the problem can be solved by modifying the PLC control program of the press and hydraulic die pad.
- 3. Concave single-action deep drawing plan
From the analysis results of the above drawing scheme, it can be seen that the deep reverse drawing on three sides caused serious cracking of the part. In order to improve the formability of the part, the part was drawn in a concave direction.
Due to the convex shape of the windshield and the large curvature of the part in the Z and Y directions, in order to avoid wrinkling of the sheet when the press ring is closed and during the drawing process, the press surface is ensured in both the X and Y directions. The included angle is larger than the included angle of the punch surface.
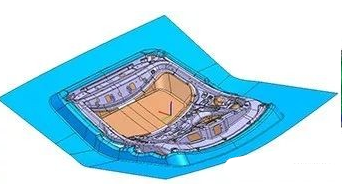
The blank size of the material is 1655mm × 1580mm. Considering the state of the blank when the pressing ring is closed, the entire pressing surface is designed according to the wind window curved surface, resulting in a deeper drawing depth on both sides. In the concave single-action deep drawing scheme, the punch is saddle-shaped and the middle die protrudes very high. During the forming process, the protruding part of the die first contacts the sheet material, and the low part of the punch saddle does not support the material. The effect aggravated the sliding of the materials at both ends toward the lower part of the saddle, causing serious wrinkling and stacking of materials in the circle position of the parts.
- 4. Concave three-action deep drawing plan
It can be seen from the CAE analysis results of the concave single-action deep drawing scheme that although all three schemes have problems, at least two conclusions can be drawn: ① The rear wind window must use a small pressure ring, but the small pressure ring It is not necessary to press the material at the same time as the outer pressing ring, and the pressing surface does not need to be designed as a pressing surface; ② The concave drawing direction is most conducive to the deep drawing and forming of the parts, and can ensure the formability of the parts to the greatest extent, but it needs to be solved Wrinkling problem during deep drawing process.
Based on the above two conclusions, when designing the drawing profile, design the pressing surfaces of the small pressing ring and the outer pressing ring into two. The pressing surface of the rear wind window should ensure the shallowest drawing depth and the outer pressing surface. The surface and the small pressing ring are not the same pressing surface, and the depth is reduced by 20mm to improve material utilization and reduce the peripheral drawing depth of the part.

From the concave single-action forming process, it can be seen that the parts have serious wrinkles during the drawing process. The main reason is that the reverse forming of the concave die encounters the saddle-shaped punch. Therefore, the process parameters are set.
Part Name | Stroke/mm | Pressing force/kN | pressure source |
External pressure ring (lower mold) | 80 | 1100 | Press ejector |
Small press ring (lower mold) | 80 | 500 | Press ejector |
External pressure ring (upper mold) | 100 | 1000 | Nitrogen gas spring |
It can be seen from the pressure that the action sequence of the three-action deep drawing scheme is: 180mm external pressure ring (upper mold) and external pressure ring (lower mold) are closed before the bottom → nitrogen spring compression of the external pressure ring (upper mold), achieving Double-action drawing → 80mm before the bottom, the outer pressing ring (upper mold) and the lower pressing ring (lower mold) are closed, and the double-action drawing of the upper mold is completed → the mold switches to single-action drawing → the drawing is completed.